Off we go with the things we already had on February 24th: A Block diagram, some crude models and basic size considerations.
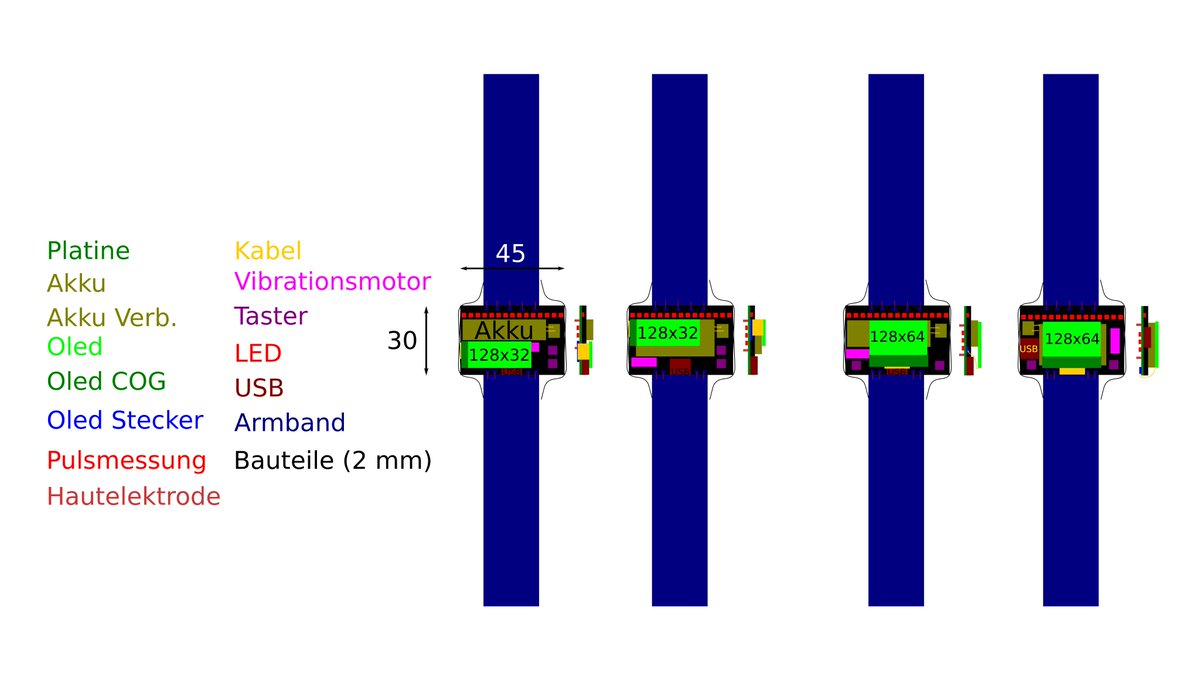
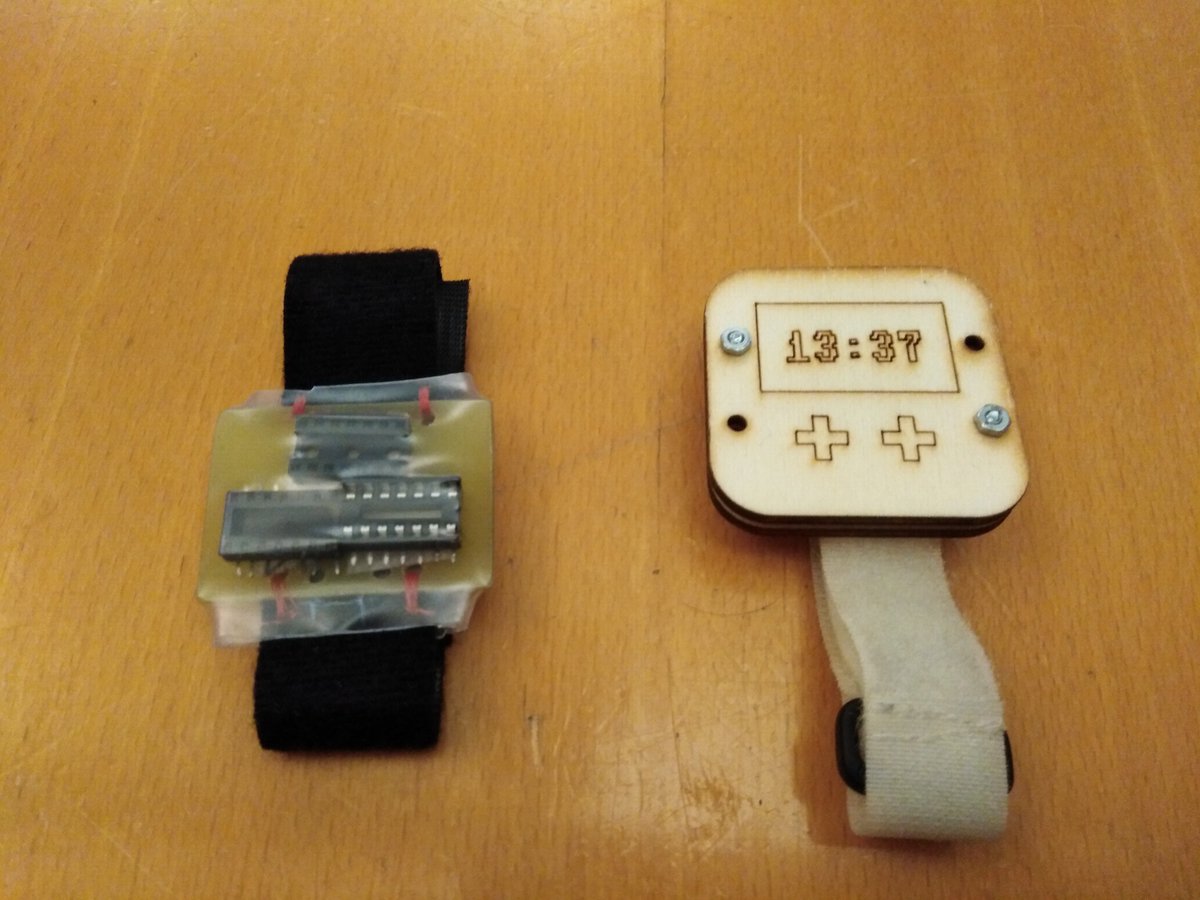
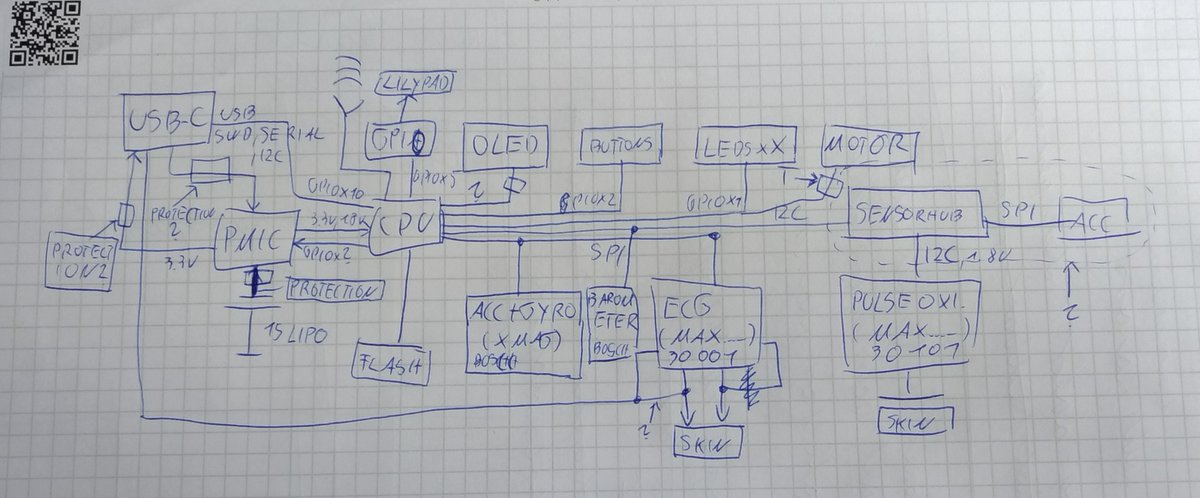
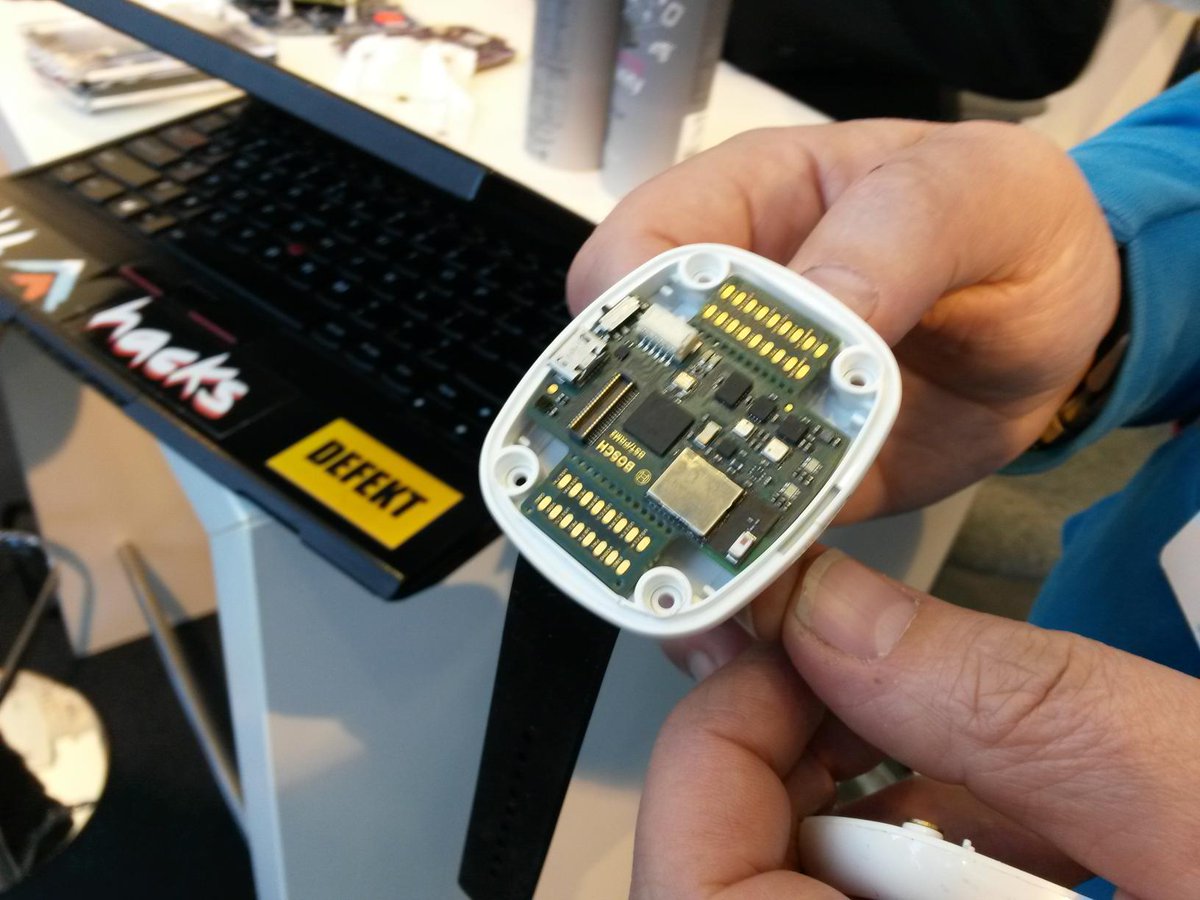
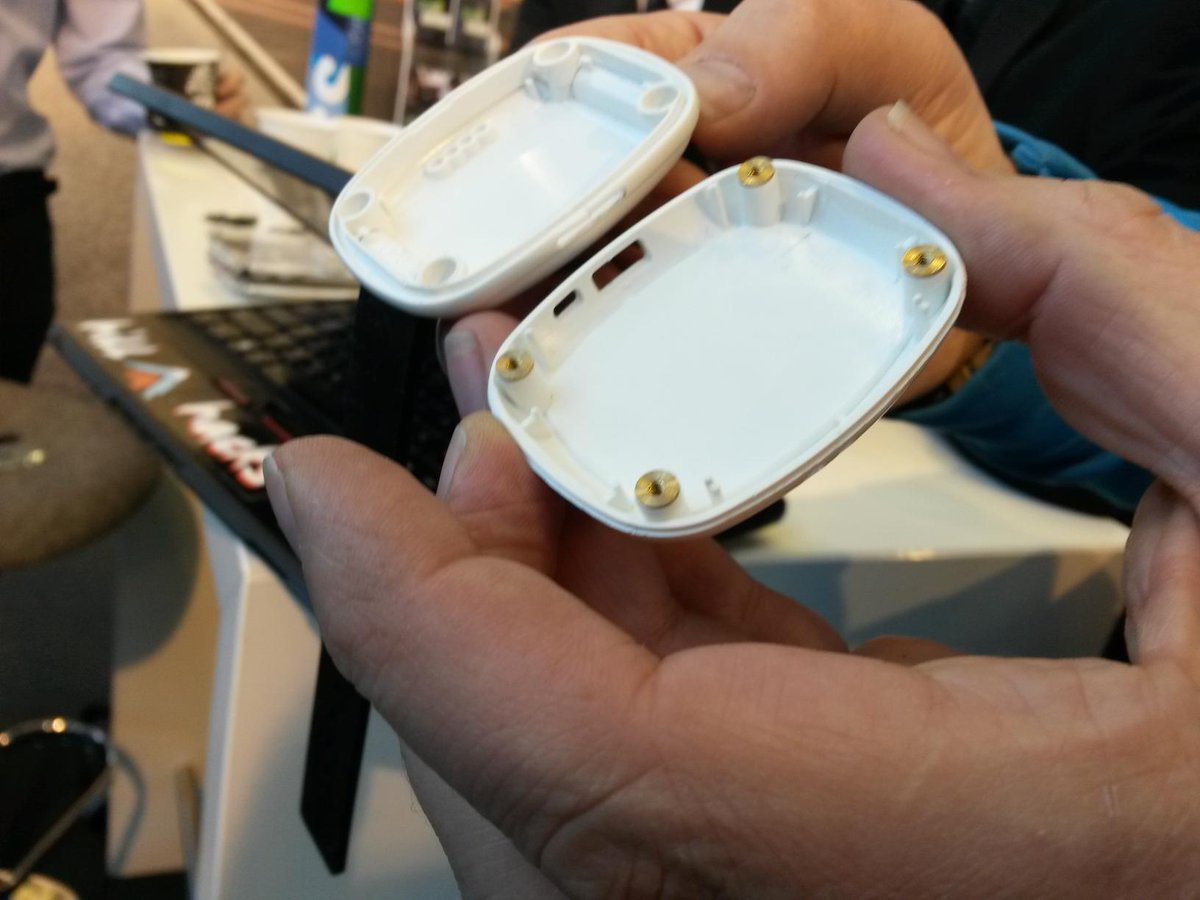
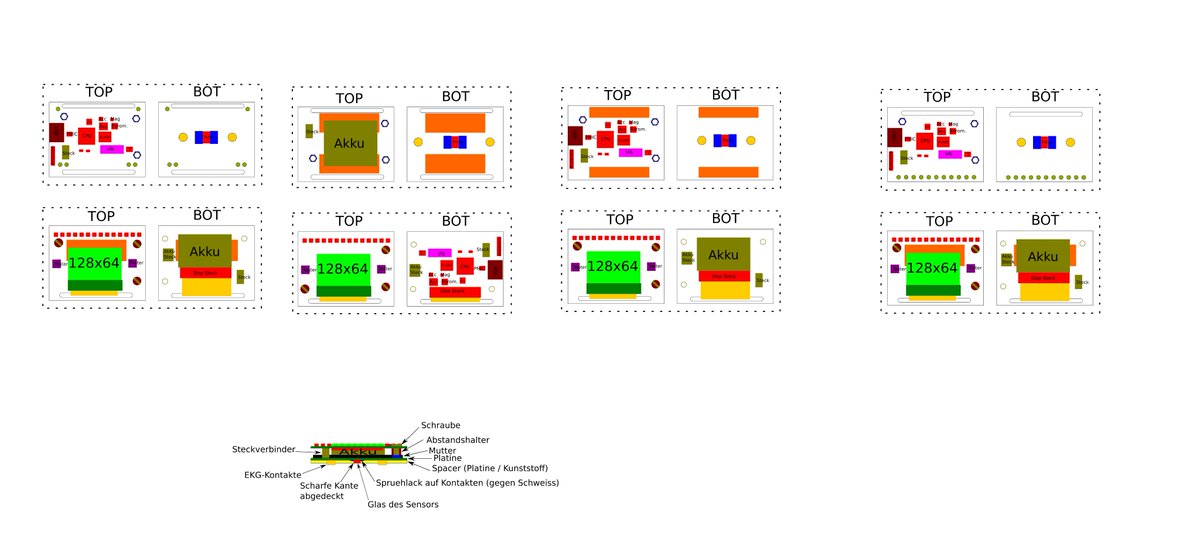
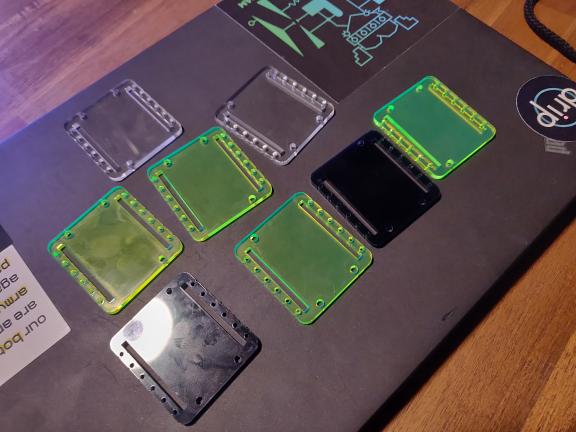
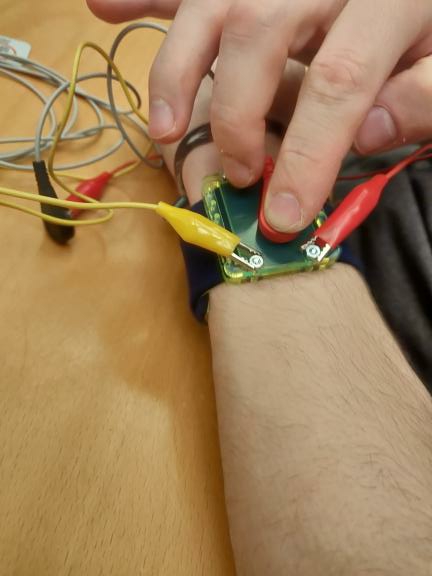
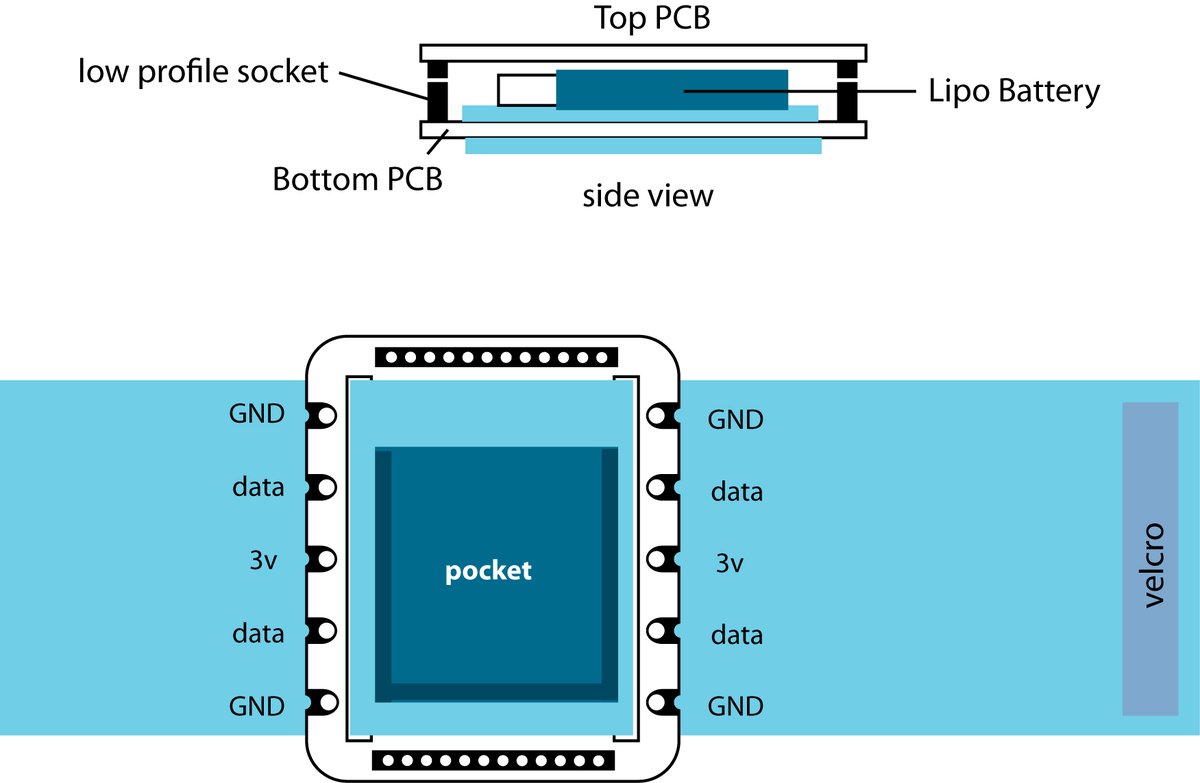
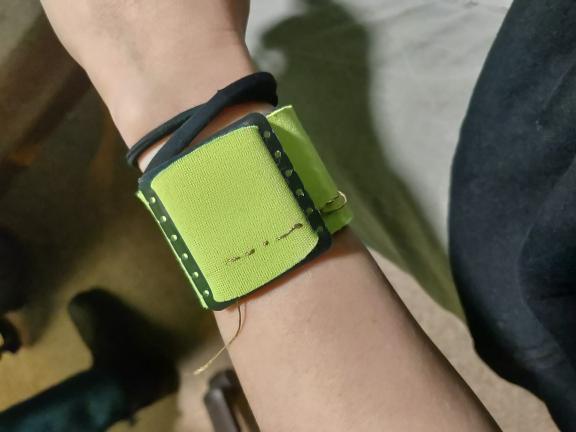
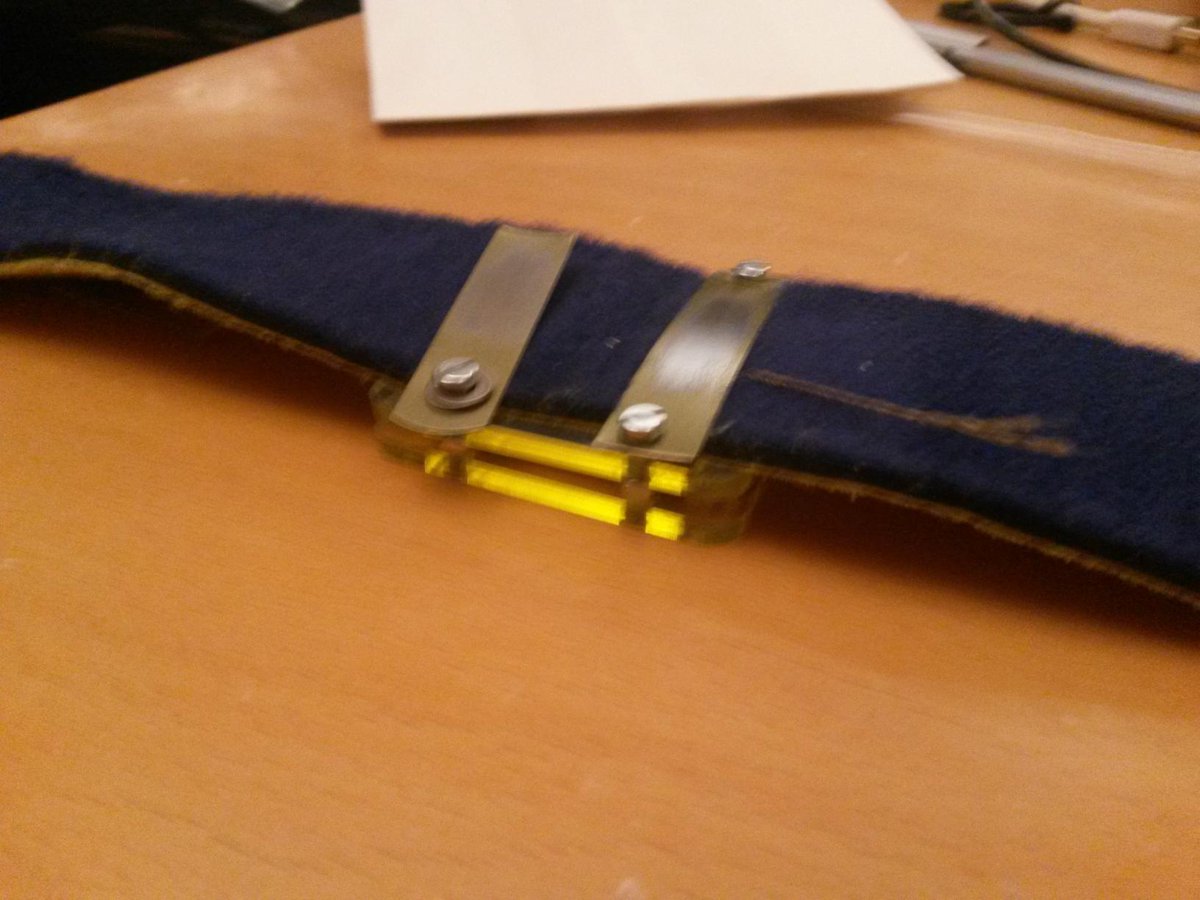
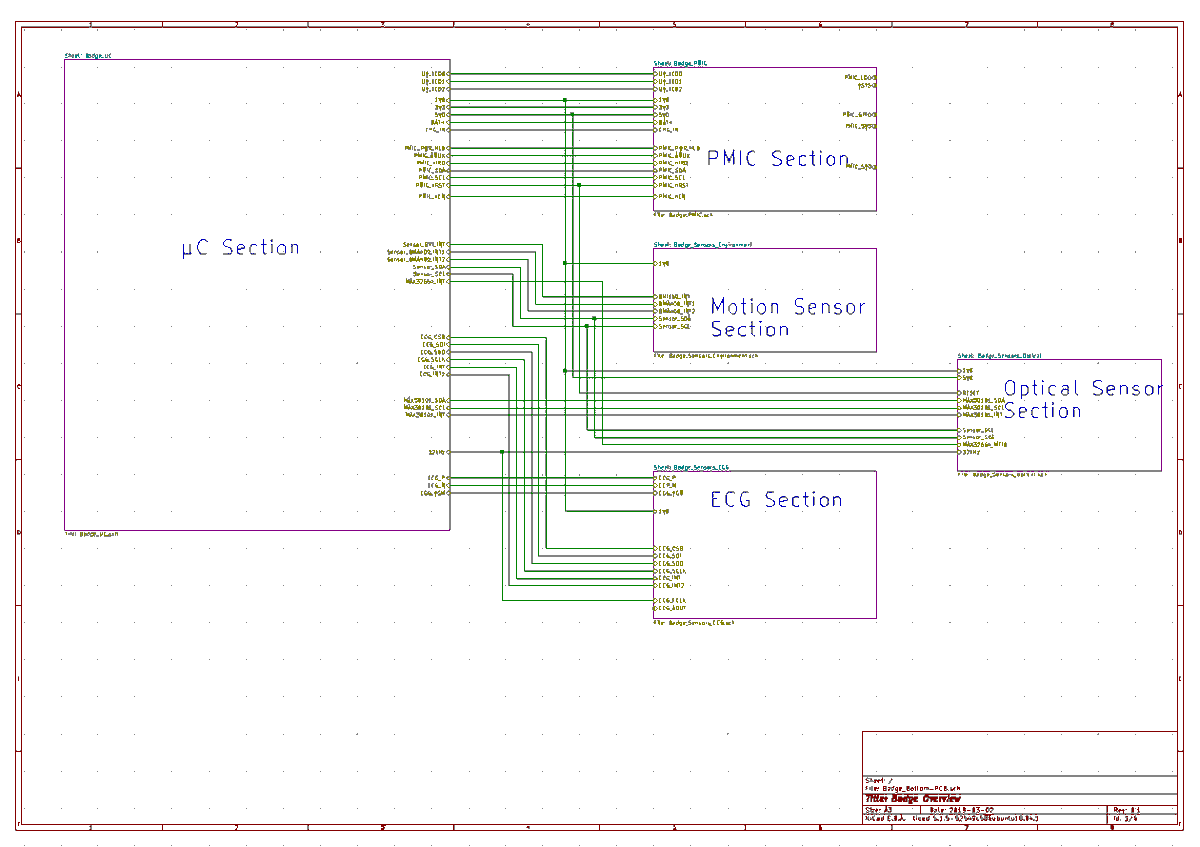
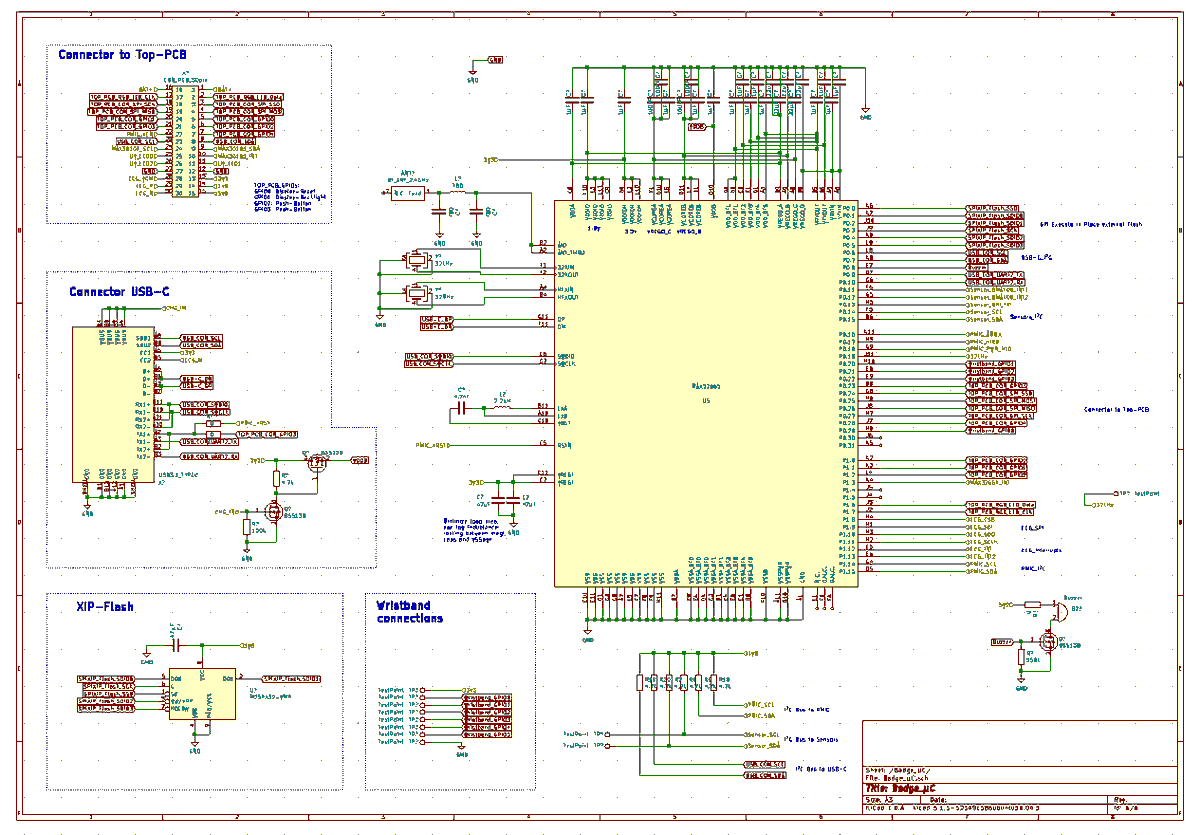
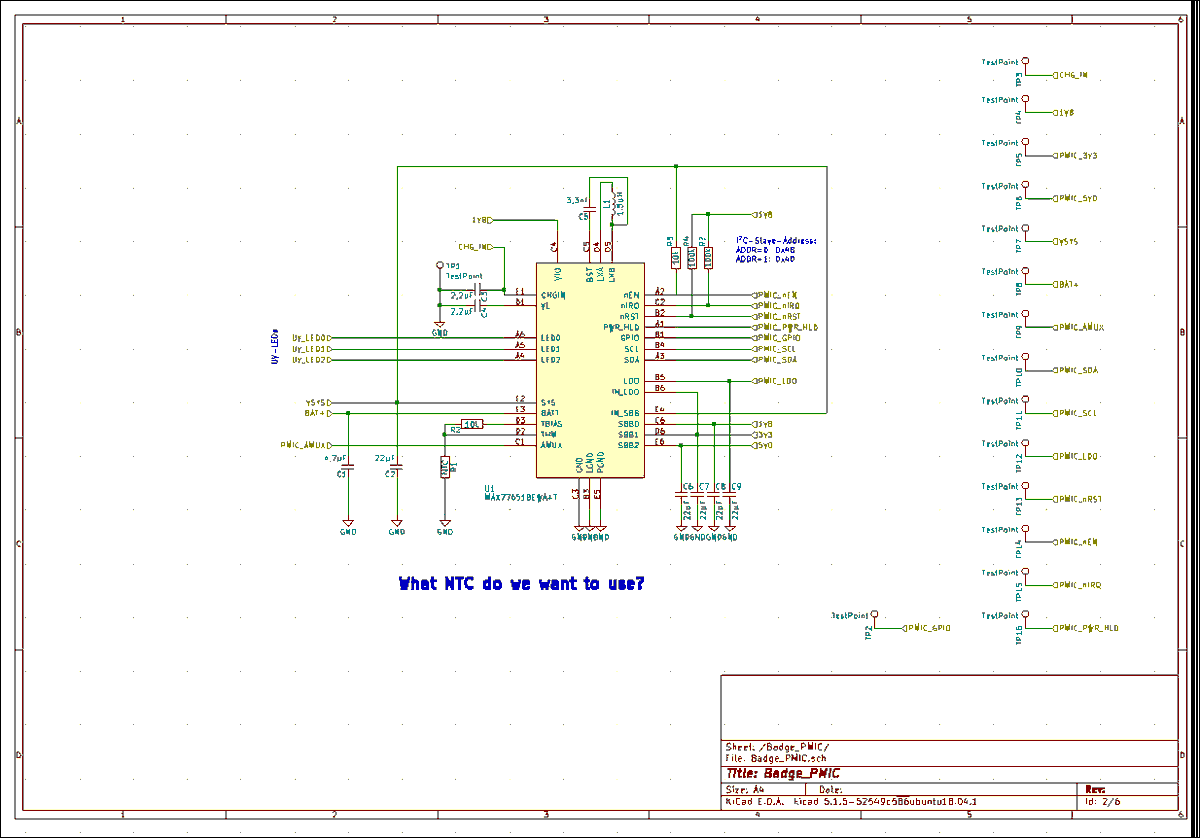
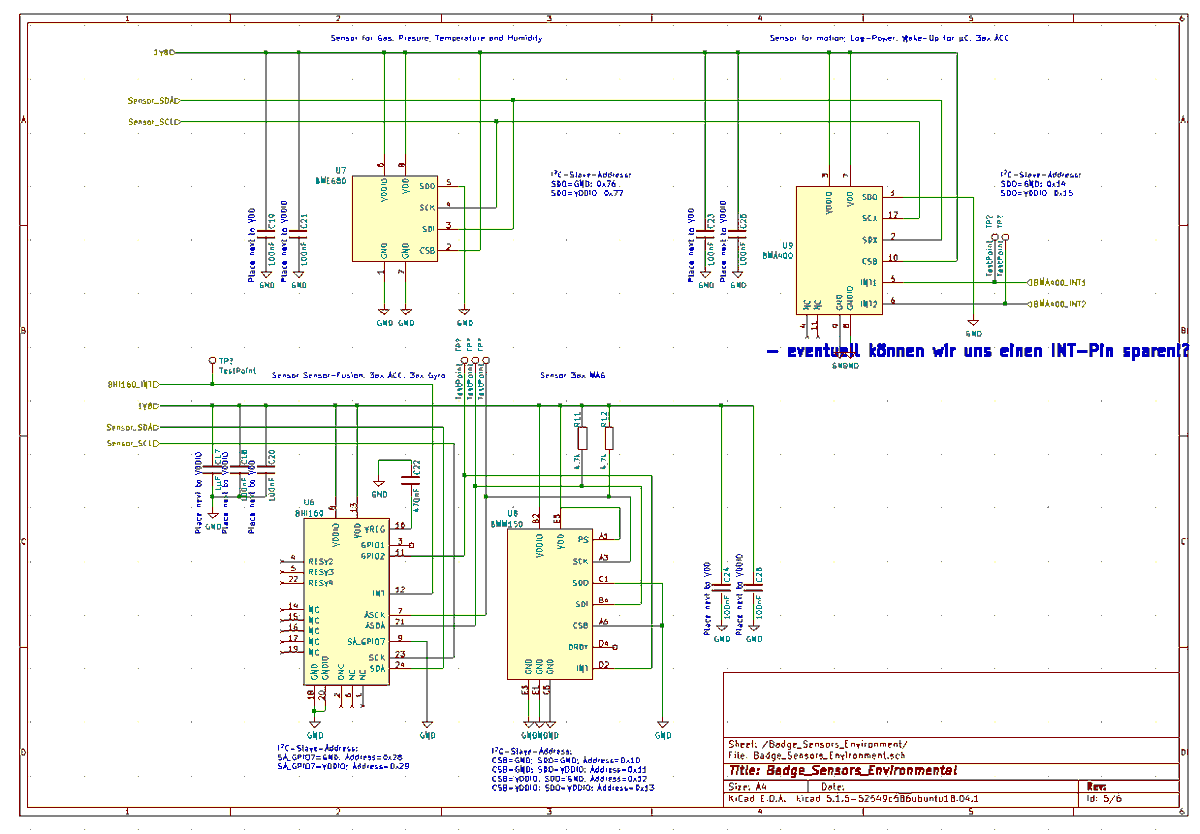
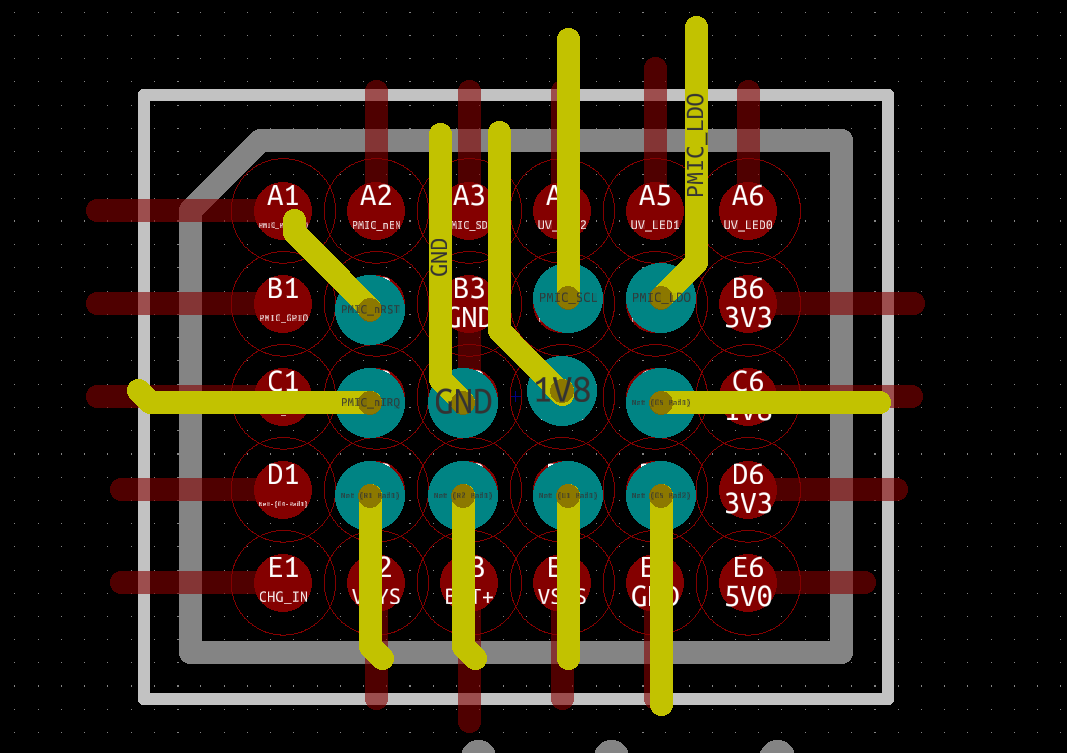
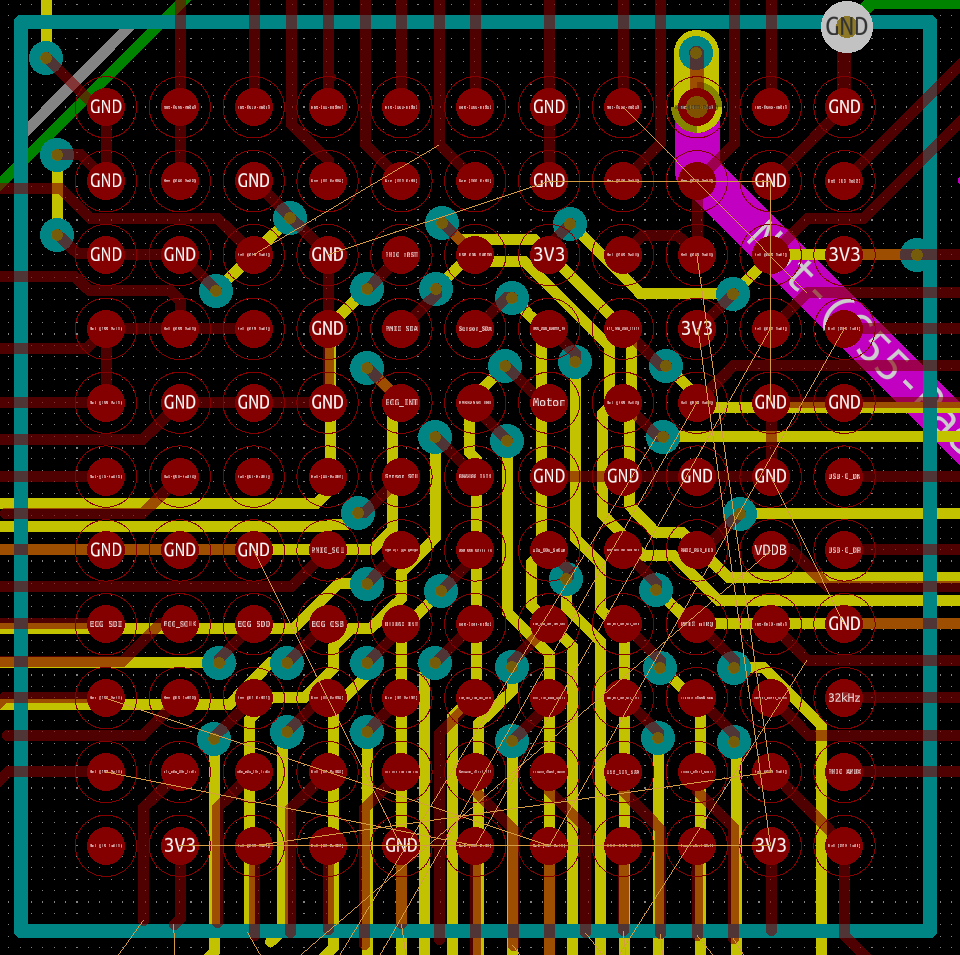
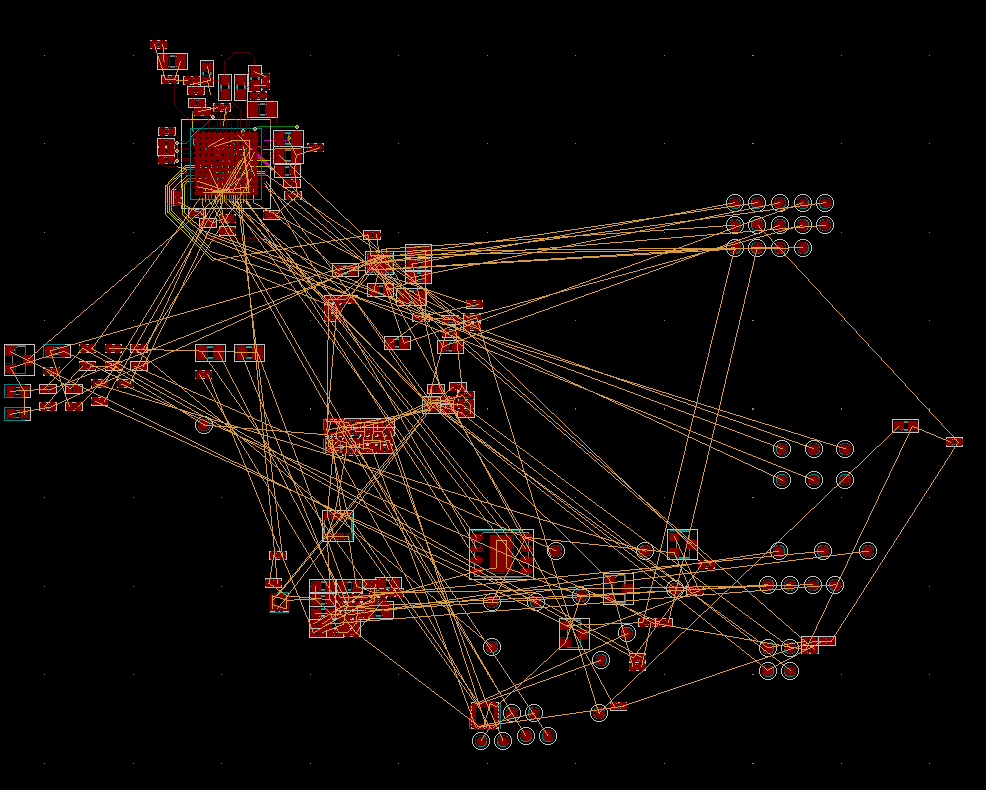
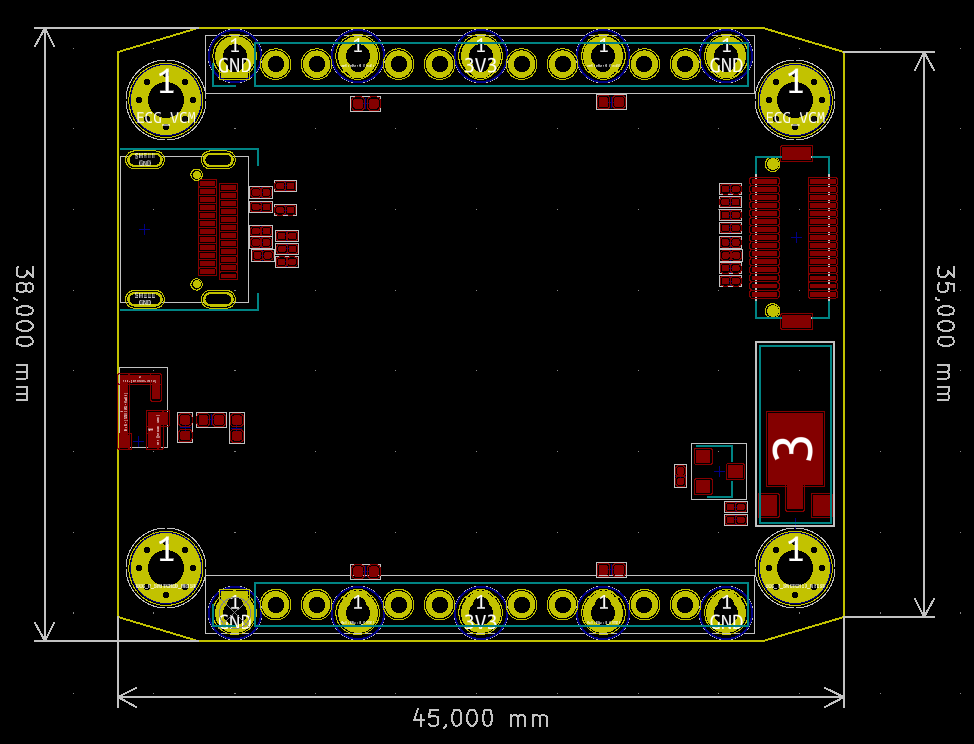
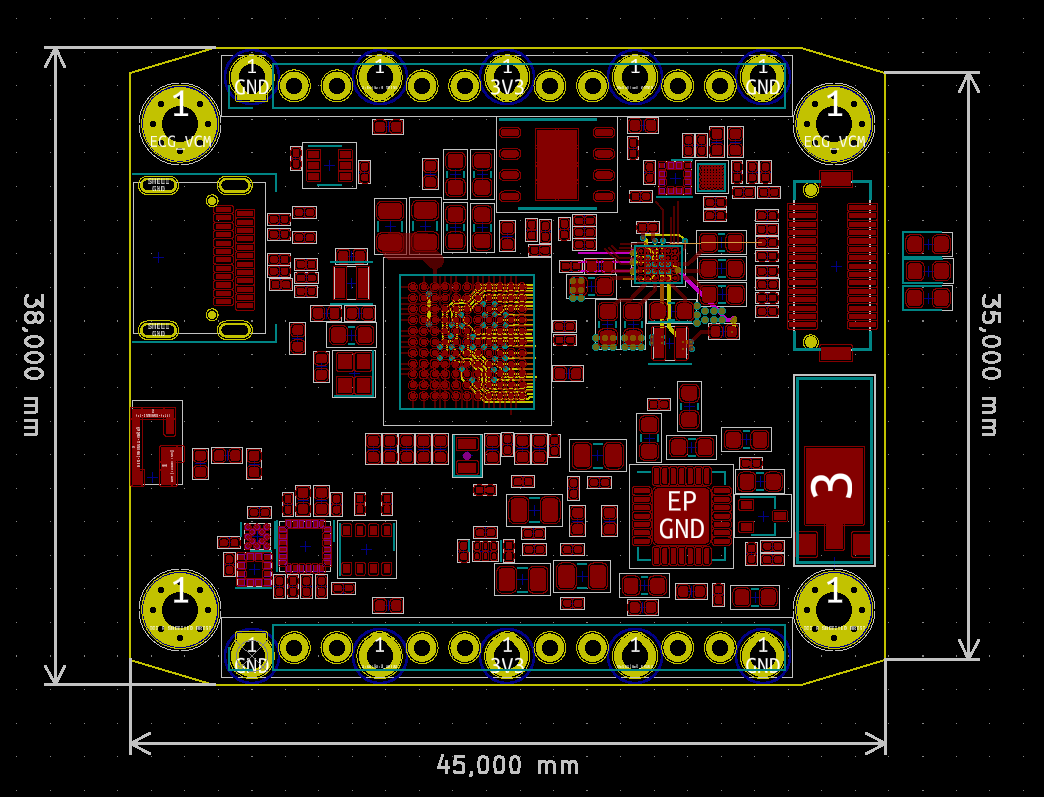
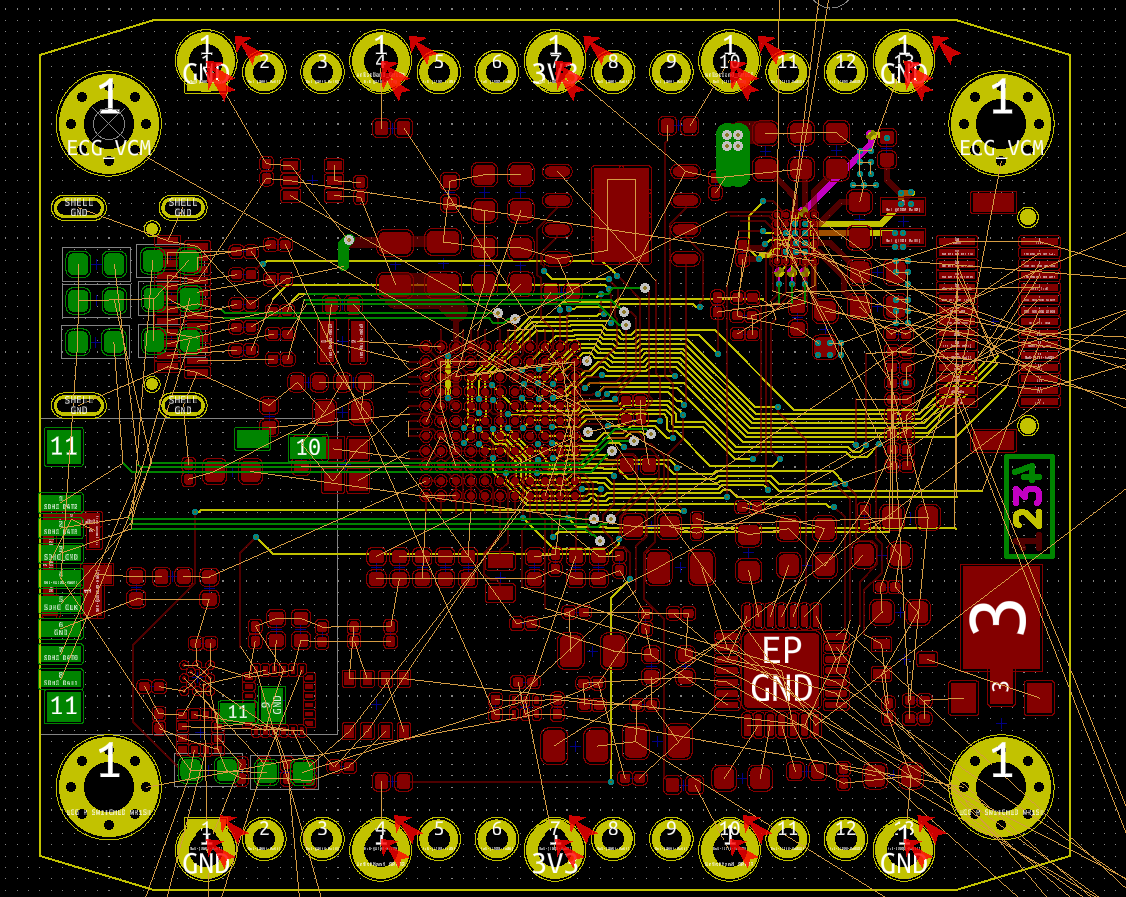
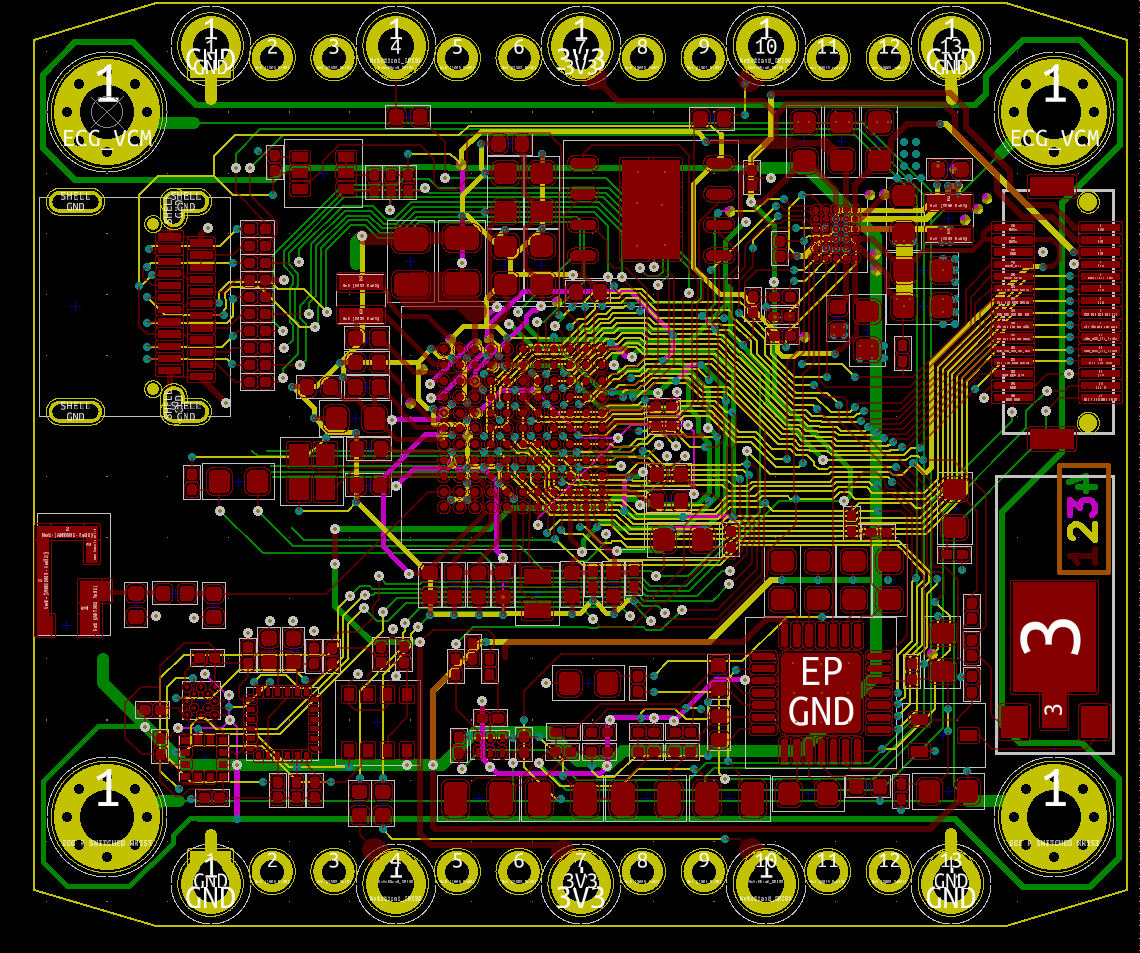
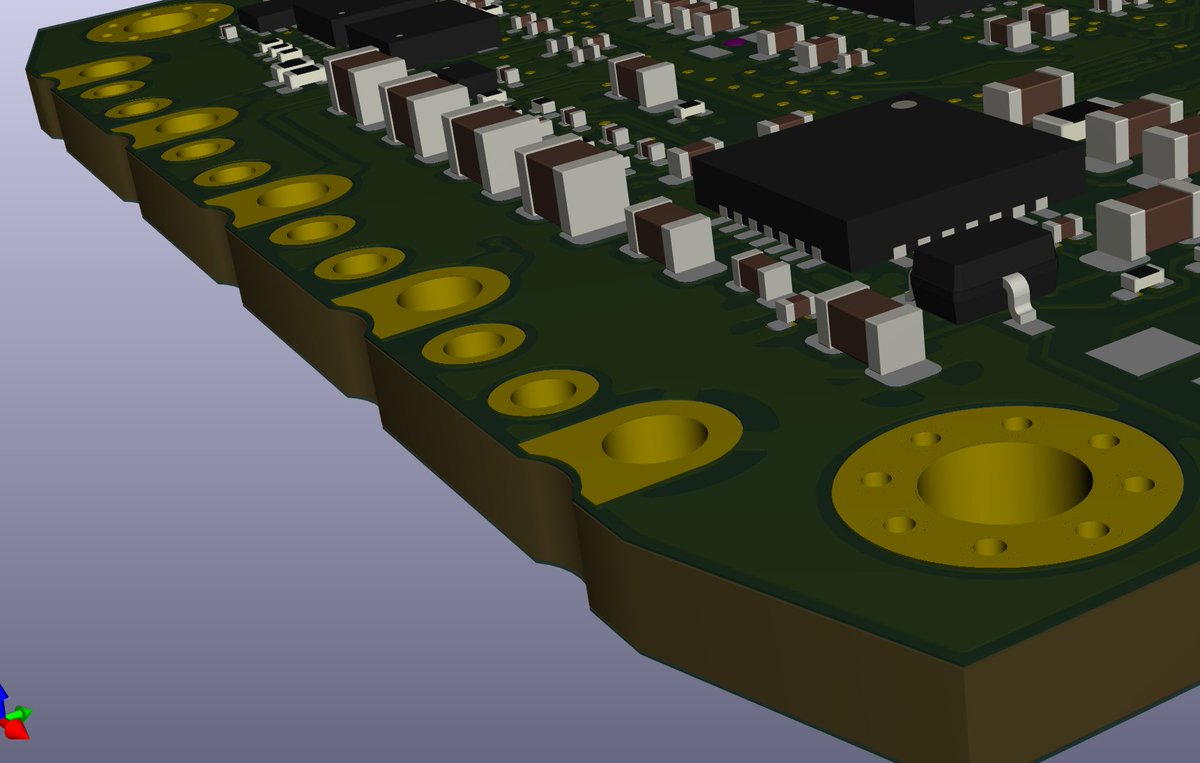
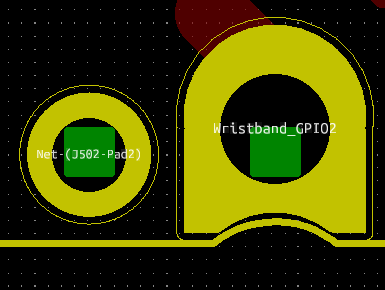

We know that if the prototypes don't work, we might have to cancel the project. HDI PCB lead times indicate that there might be no second chance. @card10badge
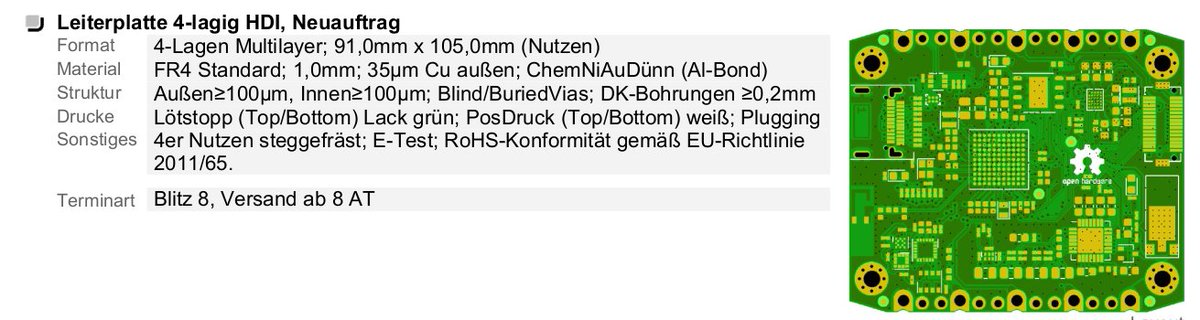
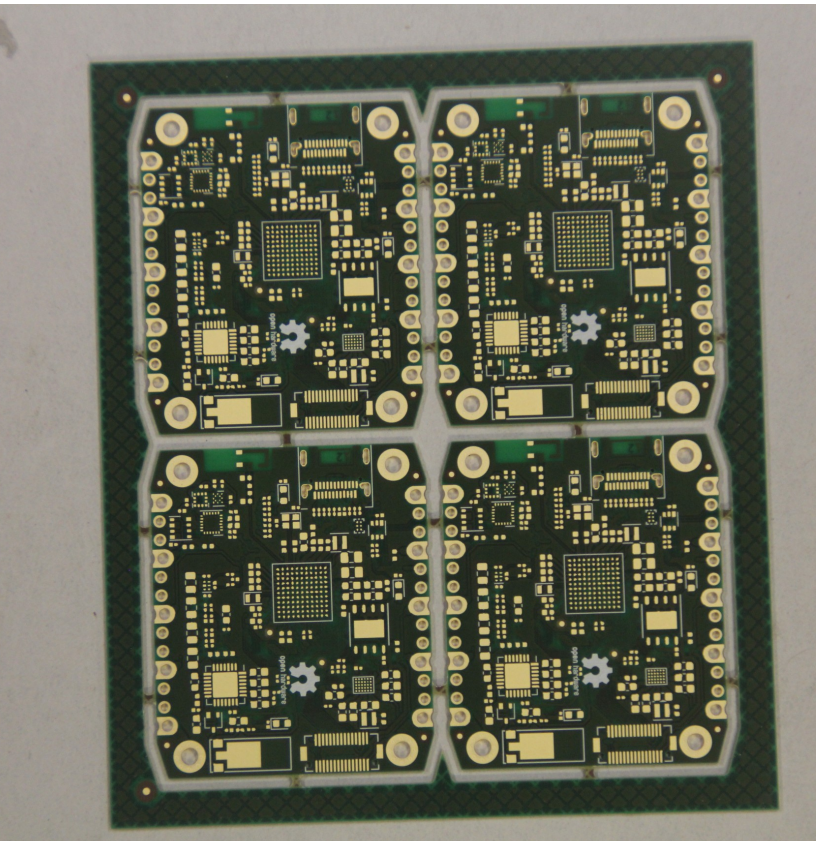
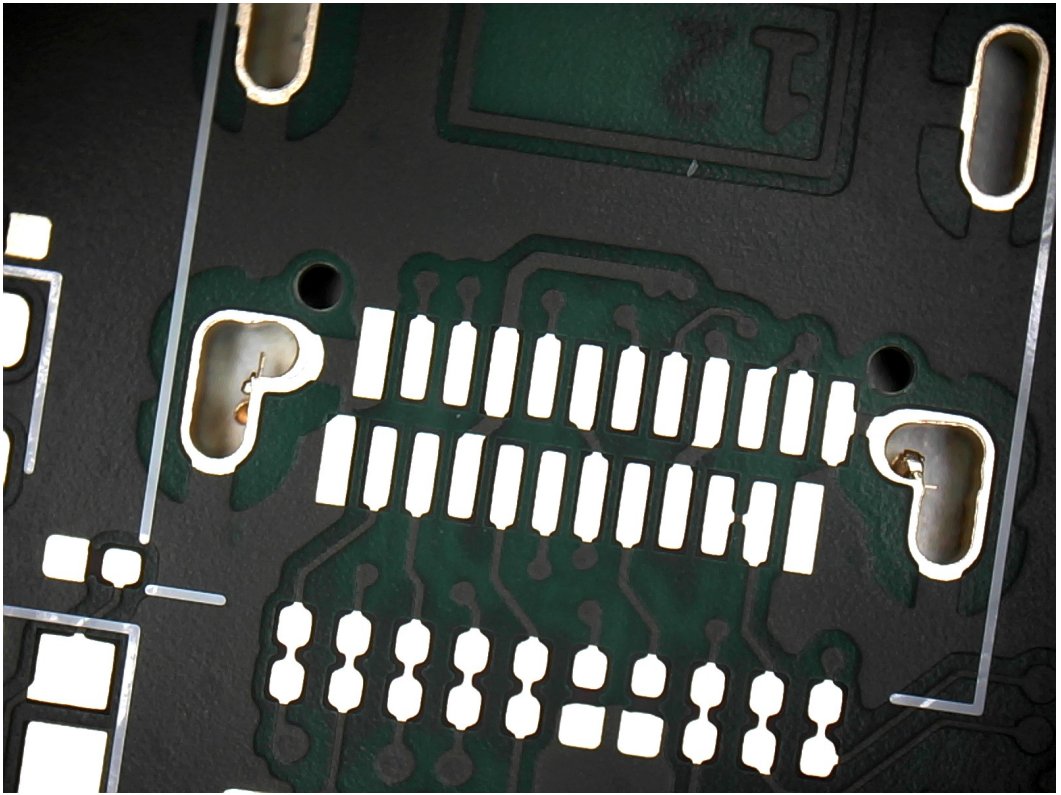
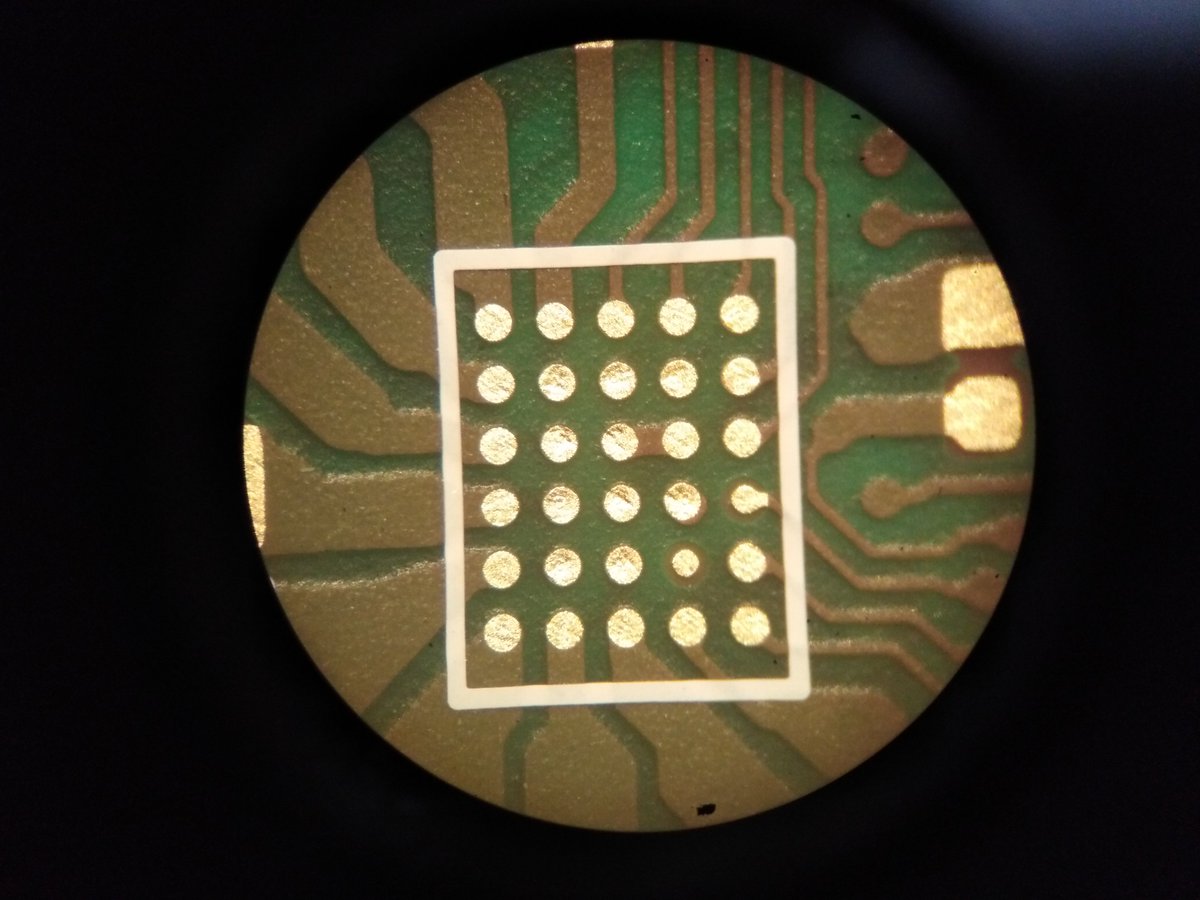

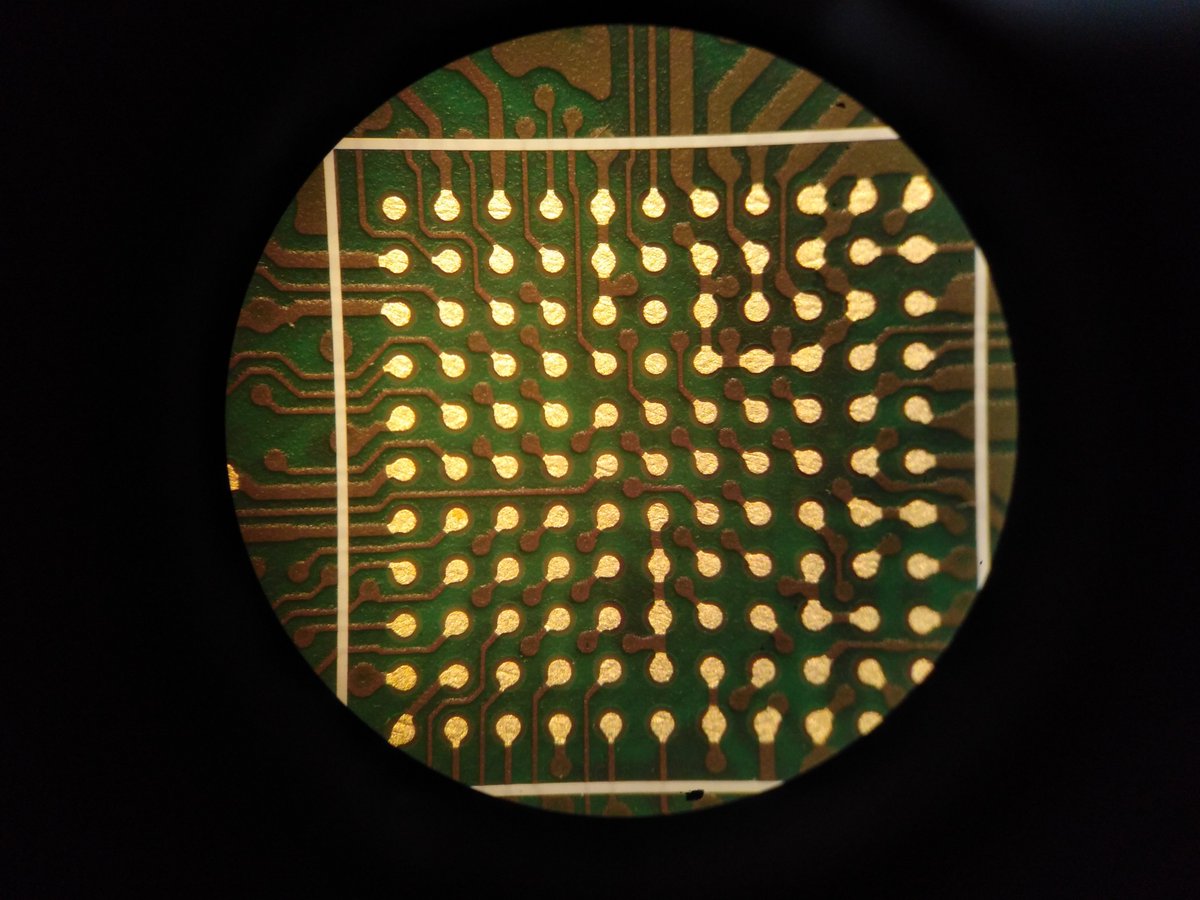
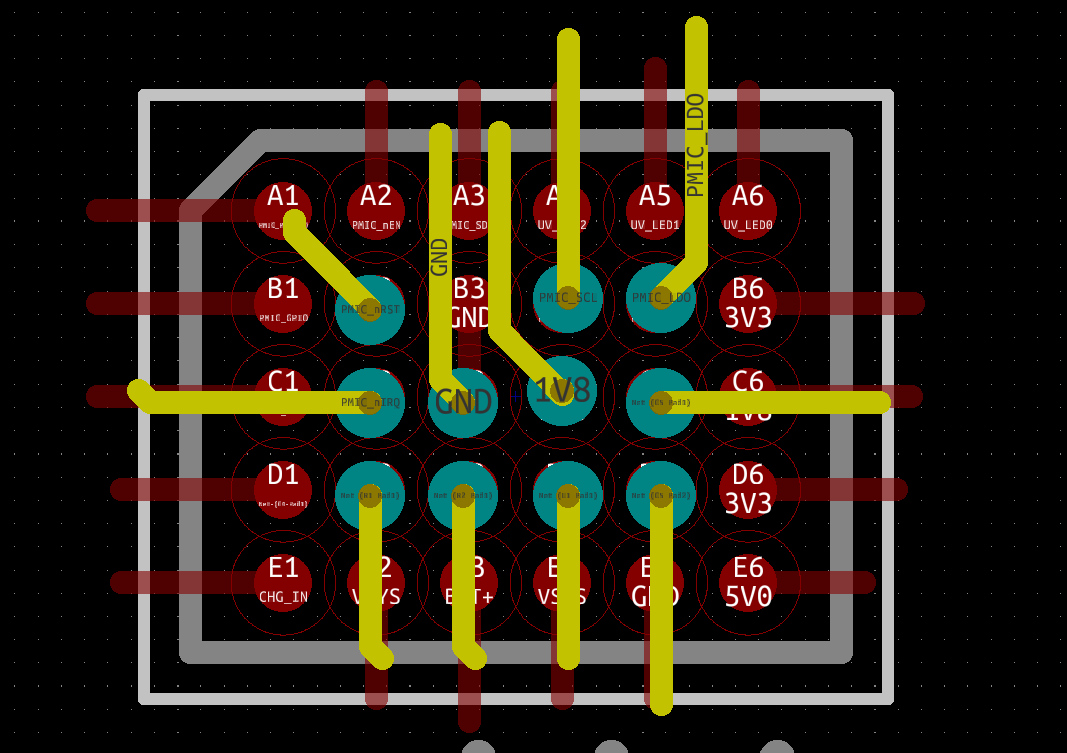
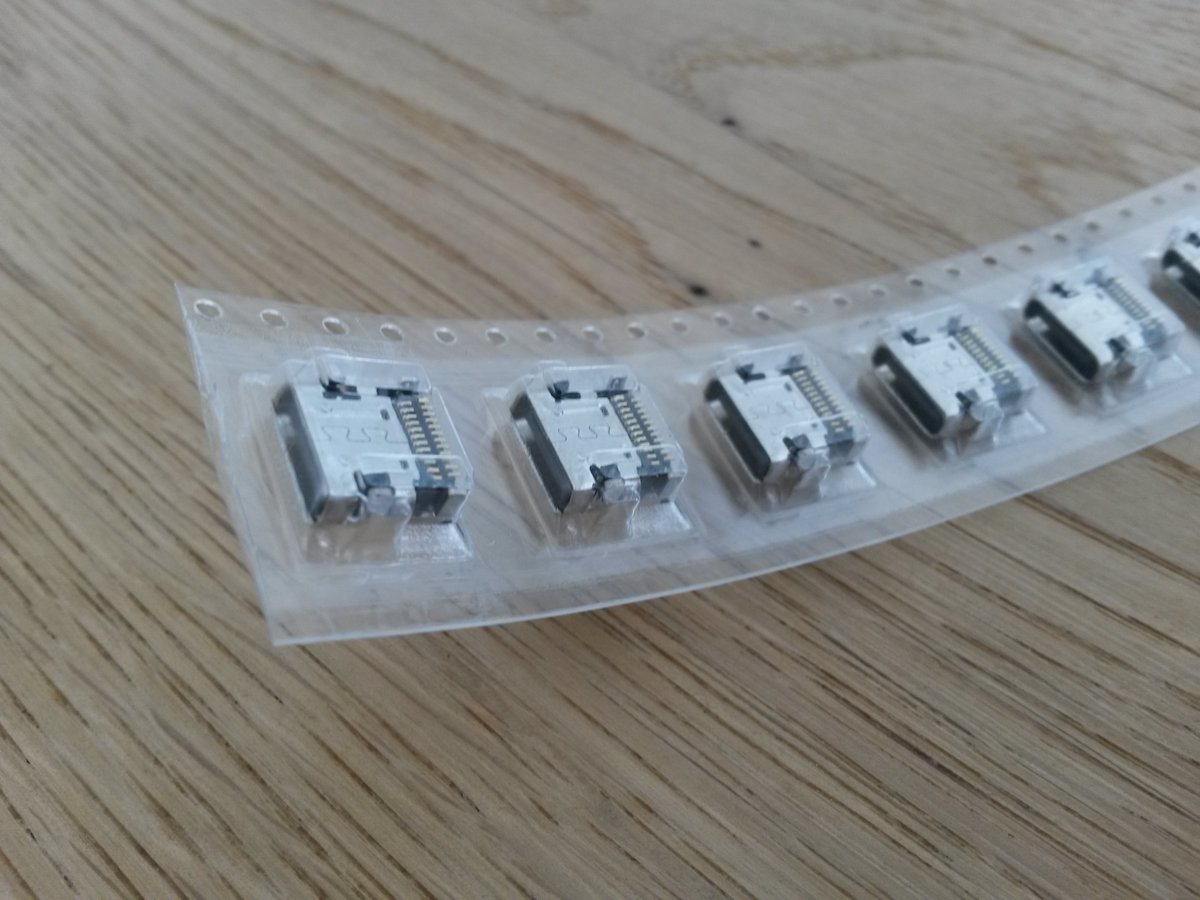
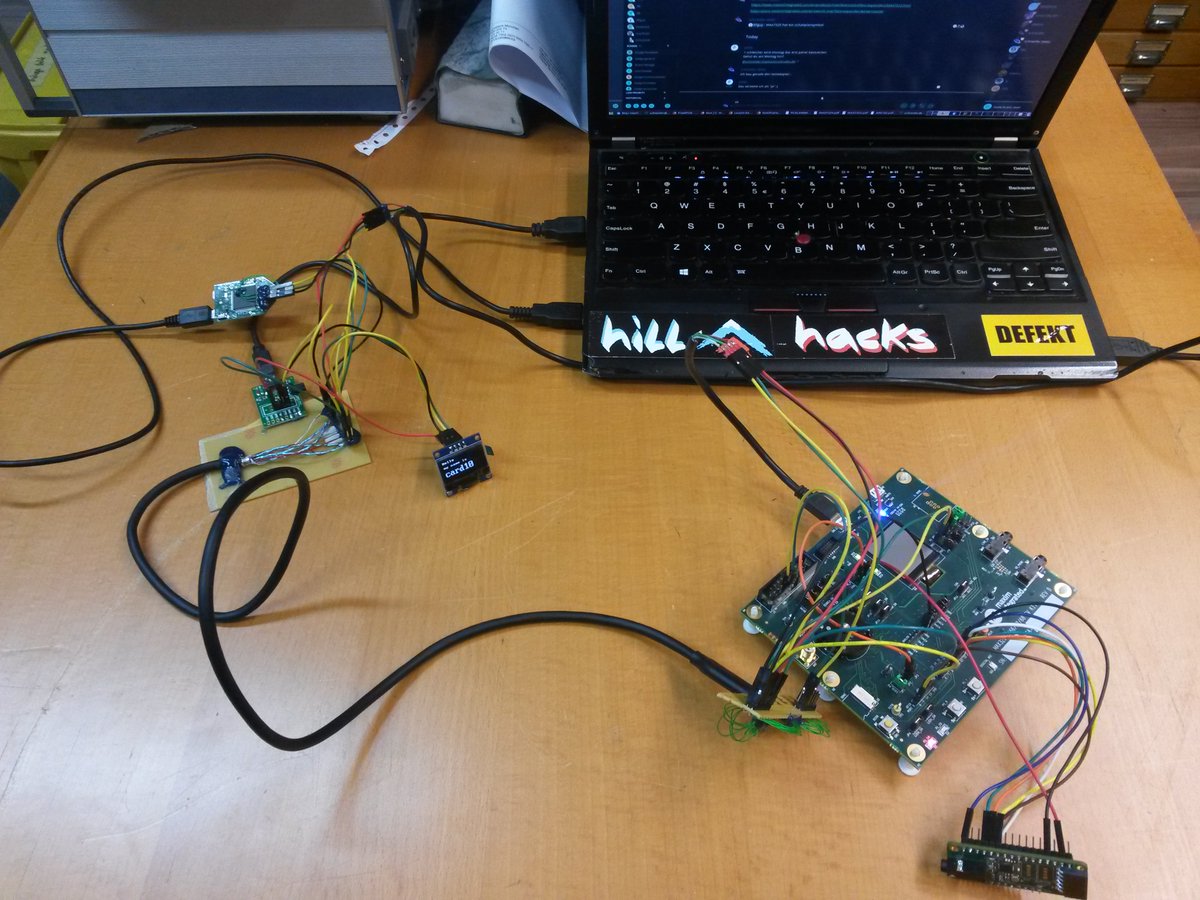
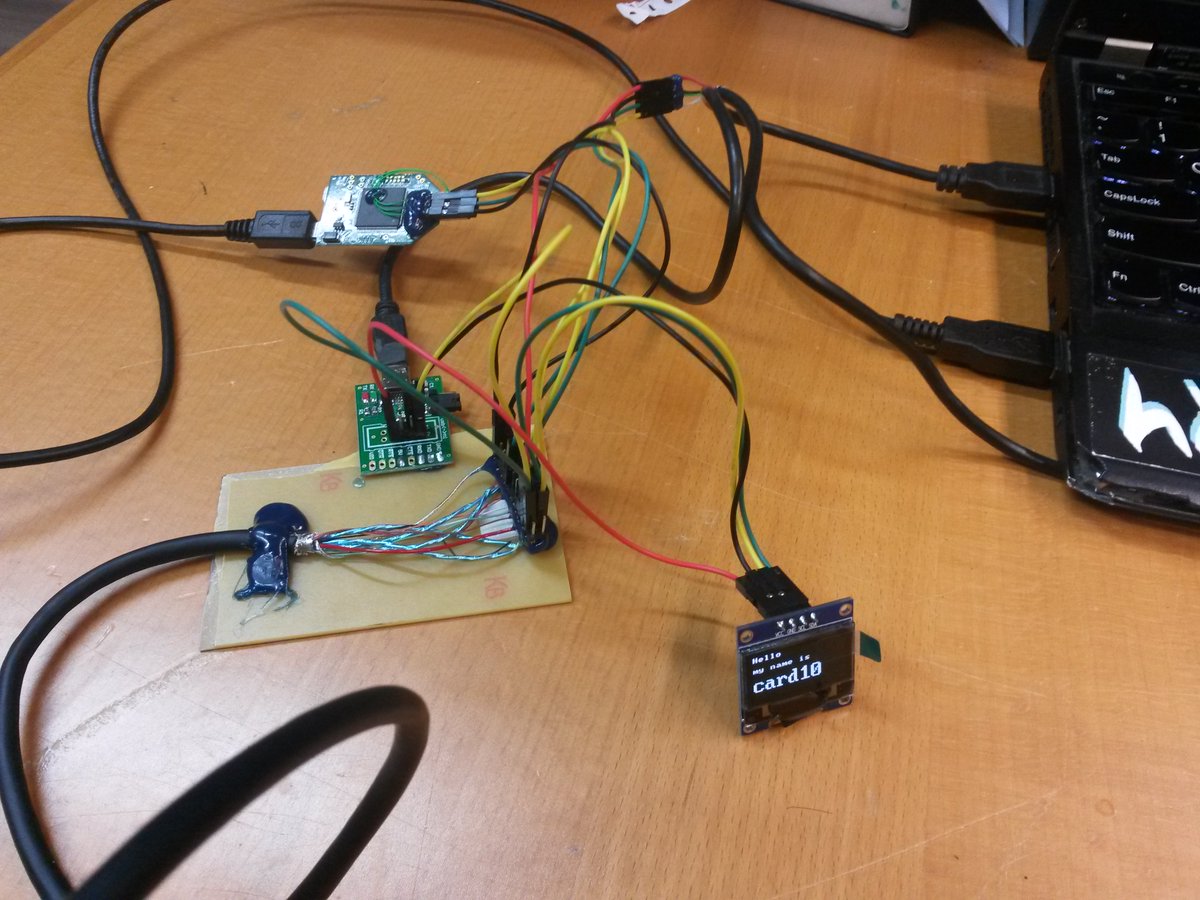
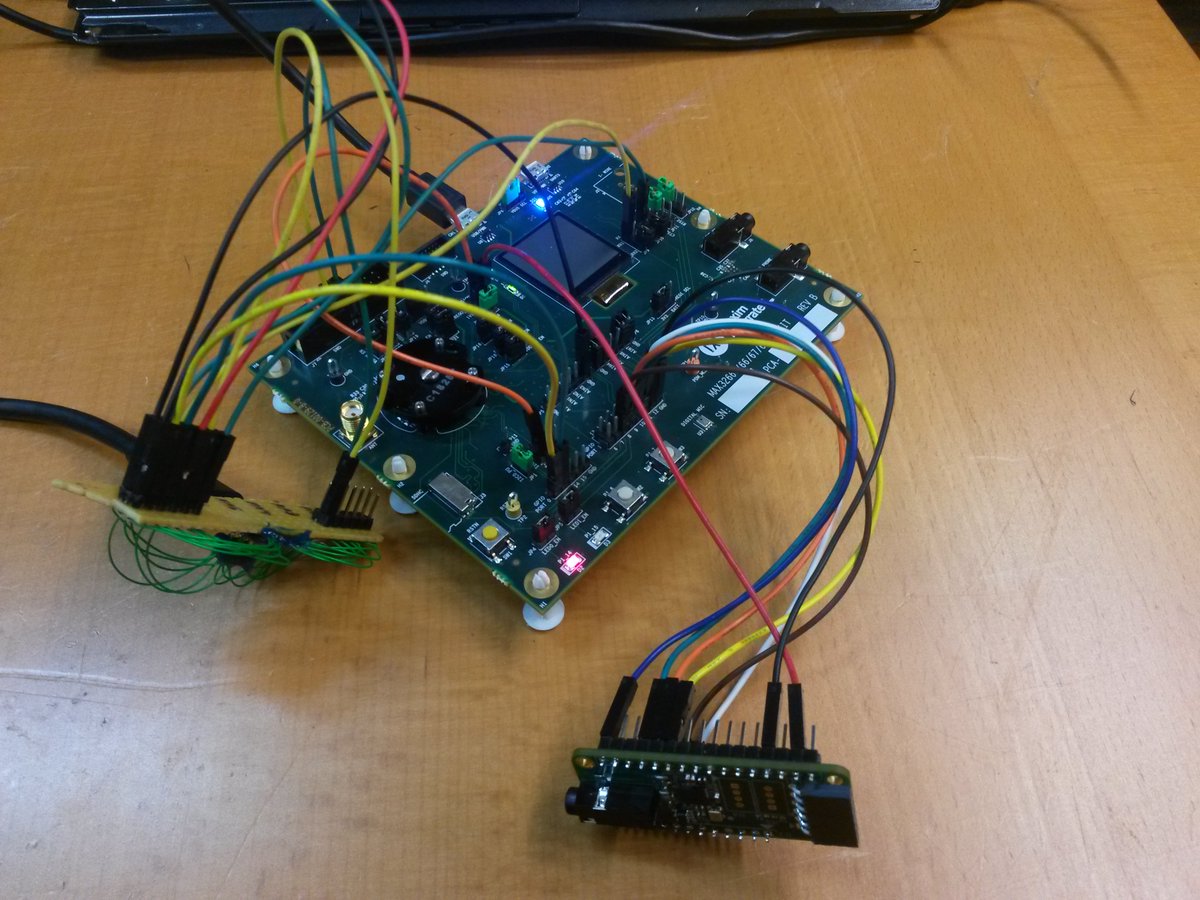
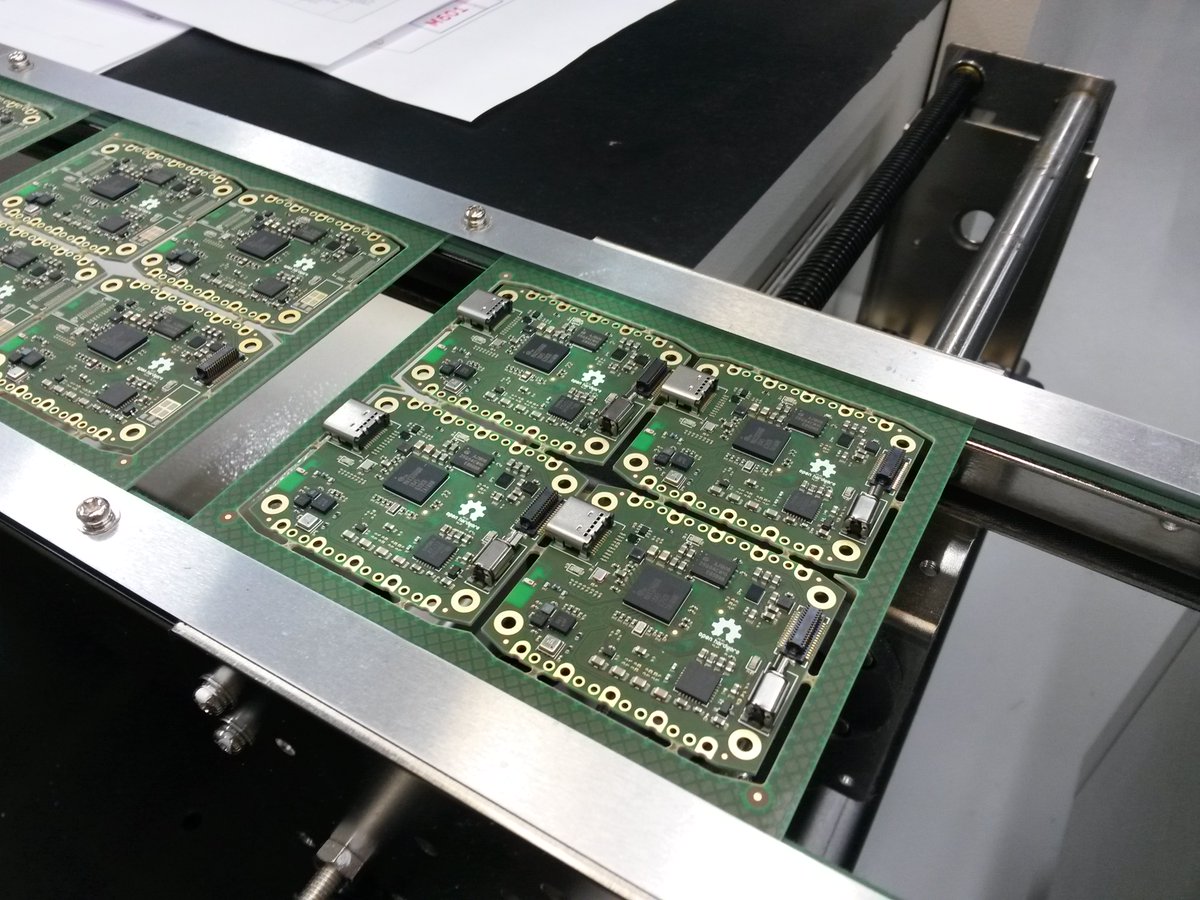
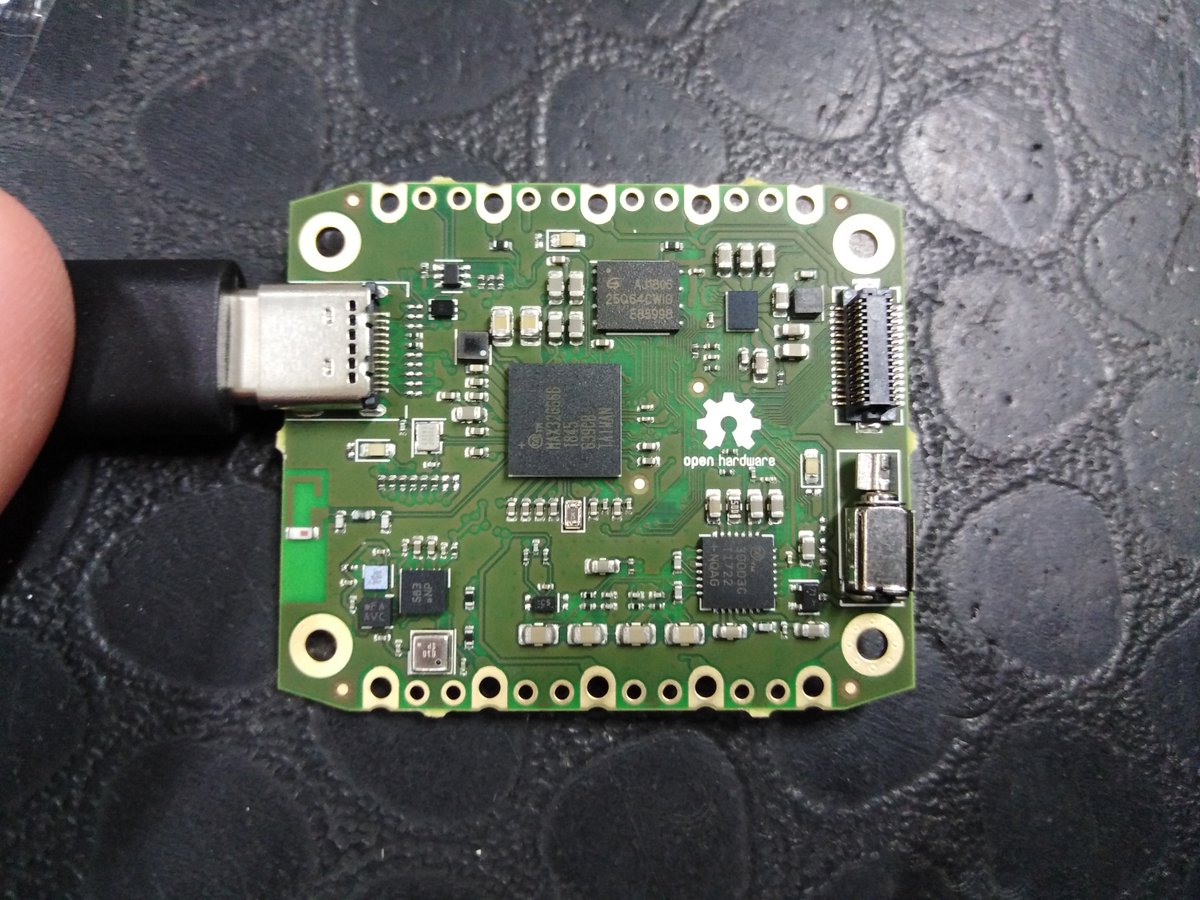
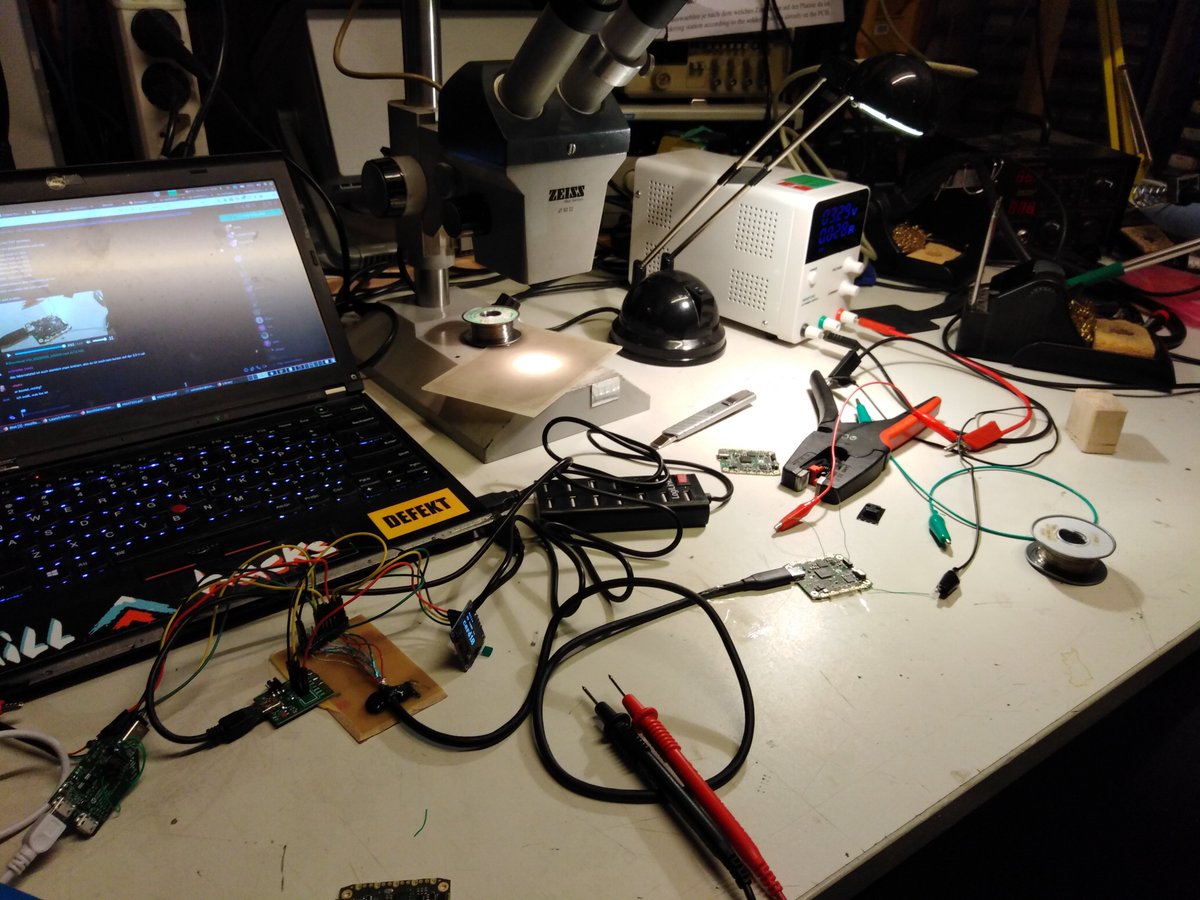
We know that if we are not able to find a solution in which we have very high confidence, the @card10badge project will fail. There is no time for a second prototype.
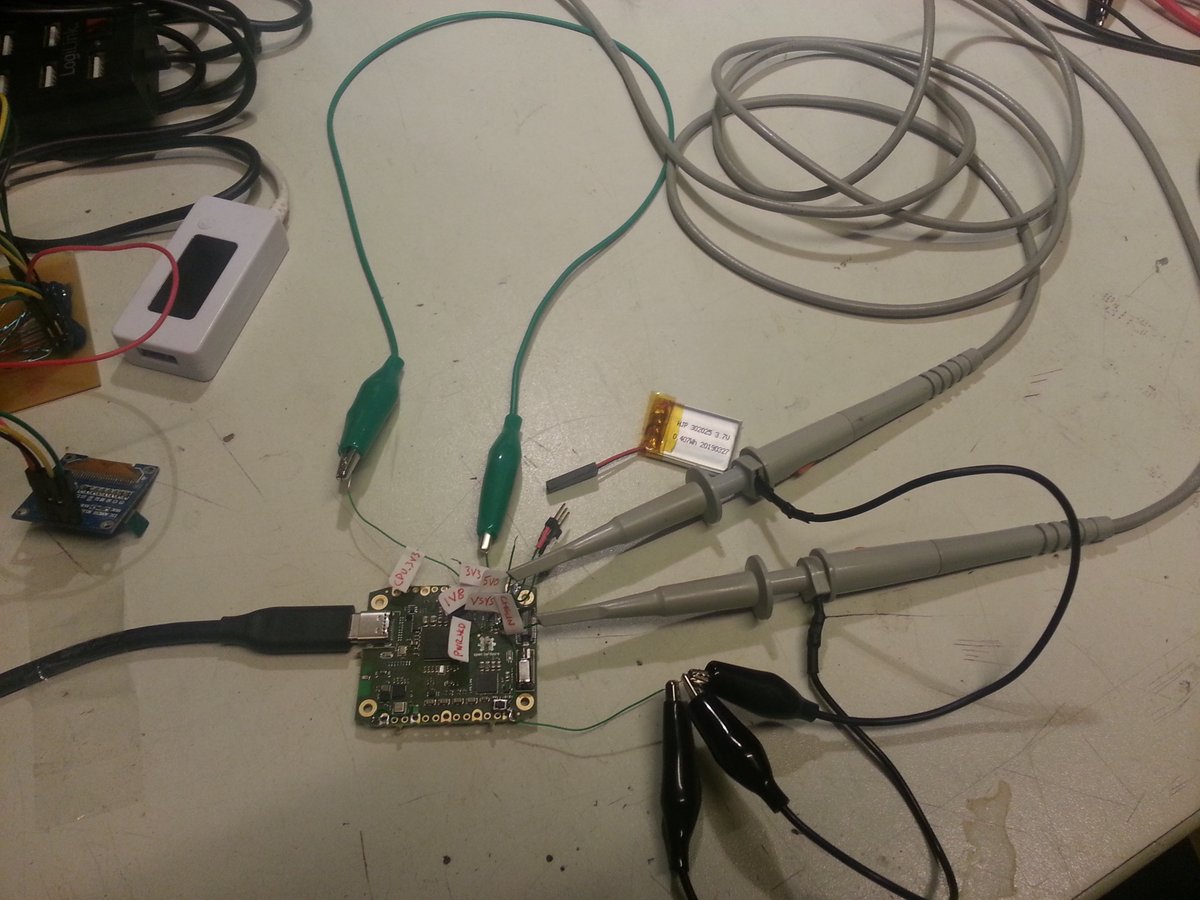

- How big is it? We need some free space for other components around it.
- Where is its connector located? It should not collide with the battery.
- Can it be replaced without soldering?
- How much does it cost?
The PMIC will not charge the battery unless instructed so by the CPU. The problem: The CPU can not start if the battery is empty.
We start to think about circuit level hacks to get around this issue.
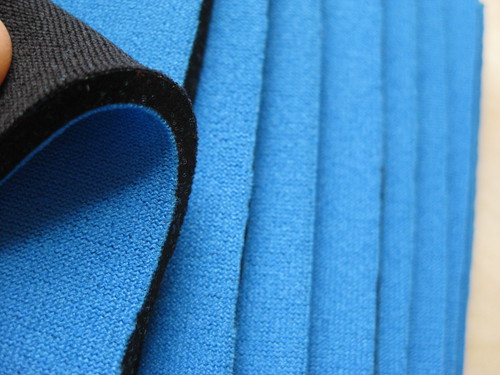
OLED:
- Off: 4 uA
- 1 pixel on: 77 uA
- all pixels on: 23 mA
IPS:
- Off: 0-10 uA
- 0% backlight: 2.1 mA
- 20% backlight: 5.4 mA
- 100% backlight: 20.7 mA
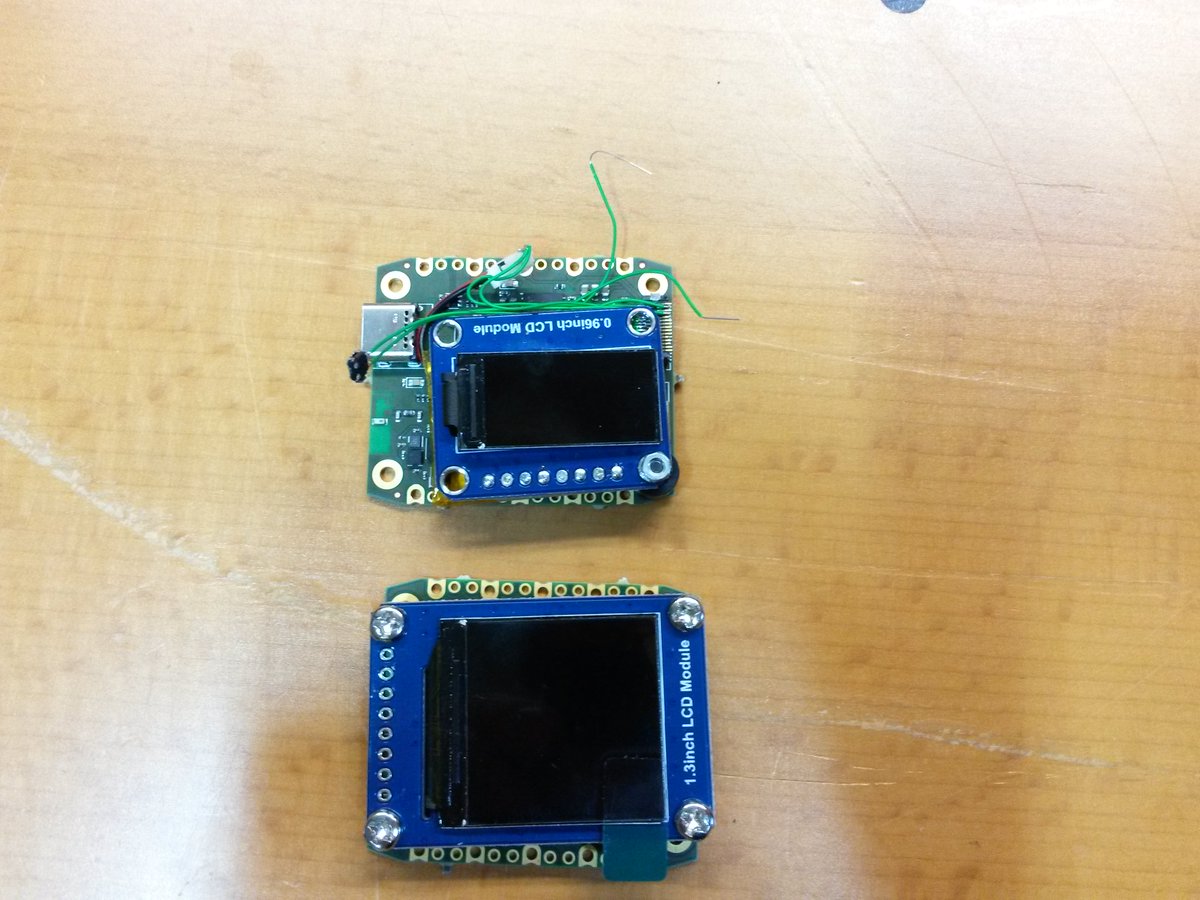
- We don't want the @card10badge to become a status symbol by selling it.
- We need to order parts soon but we don't know for how many badges.
- Producing fewer units will increase the price of each.
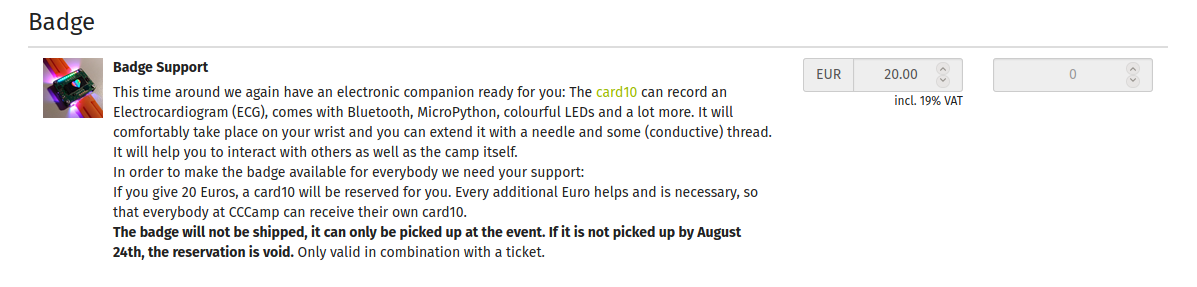
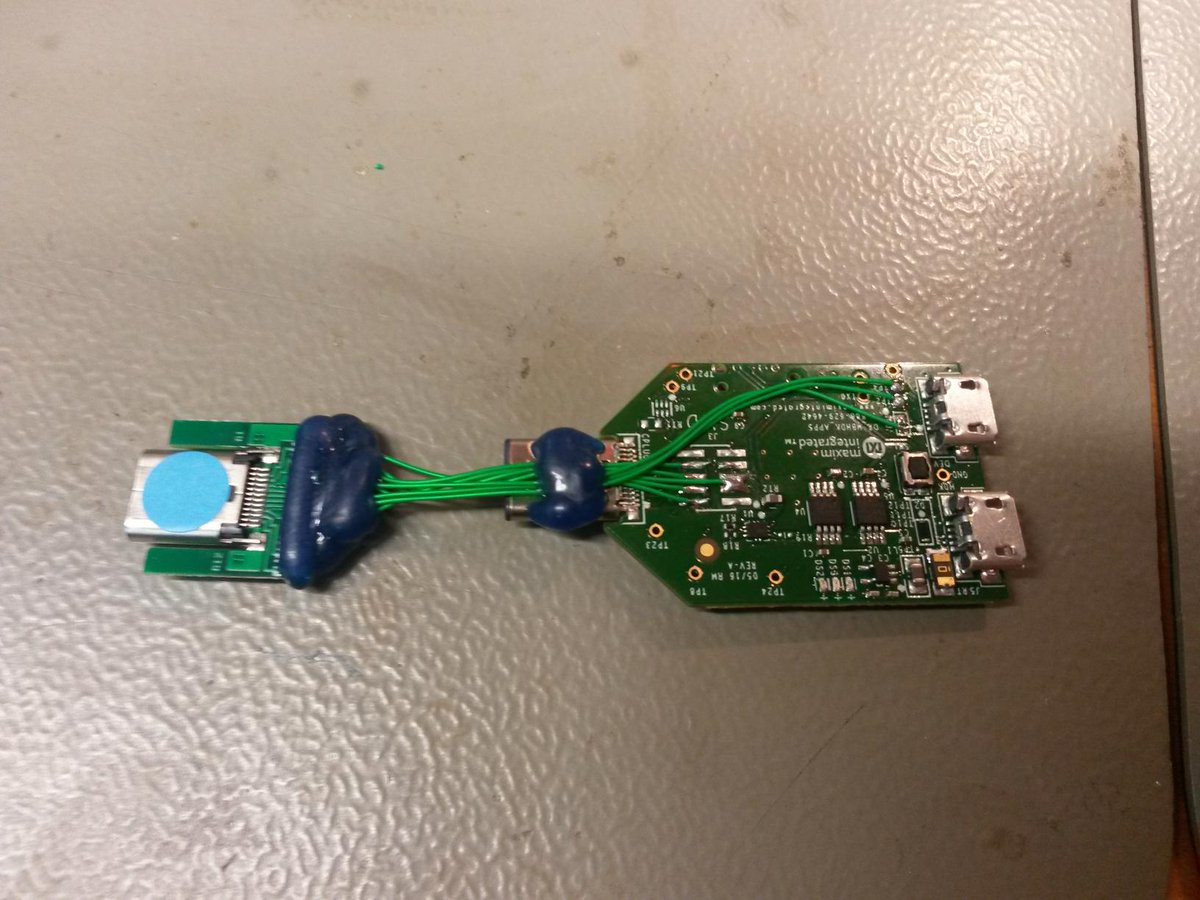
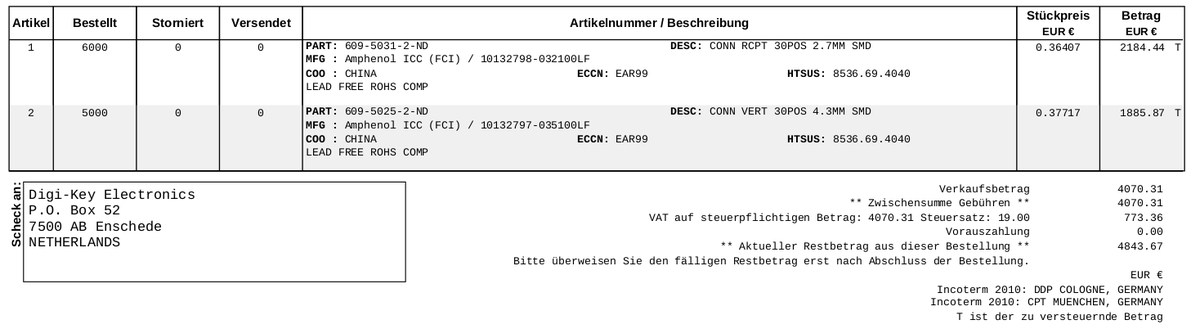
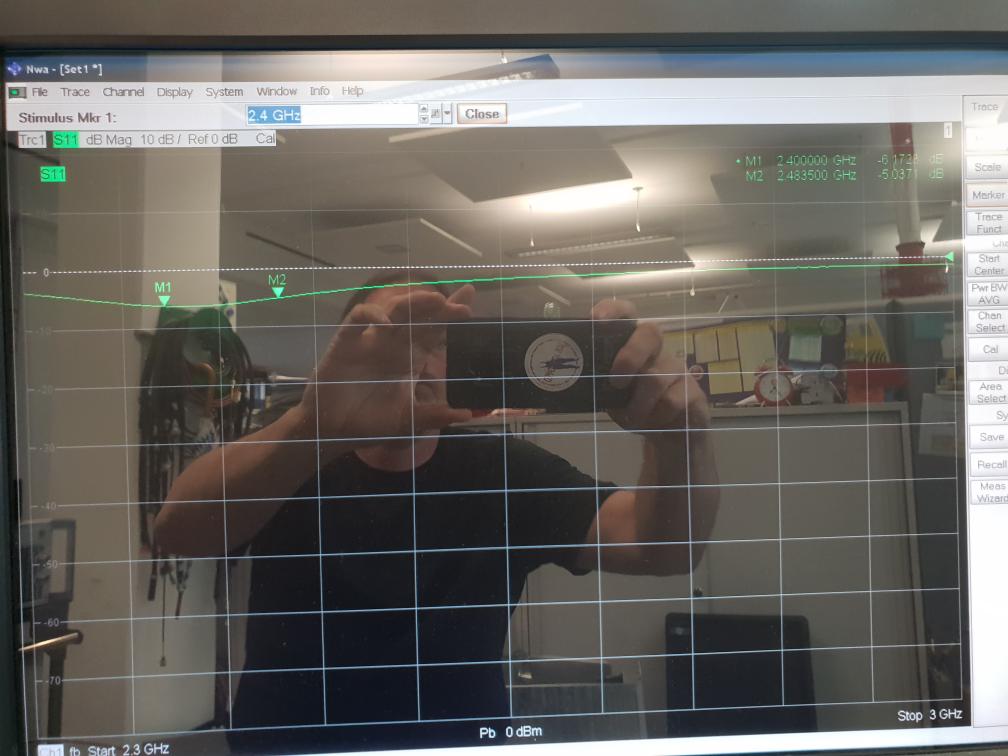
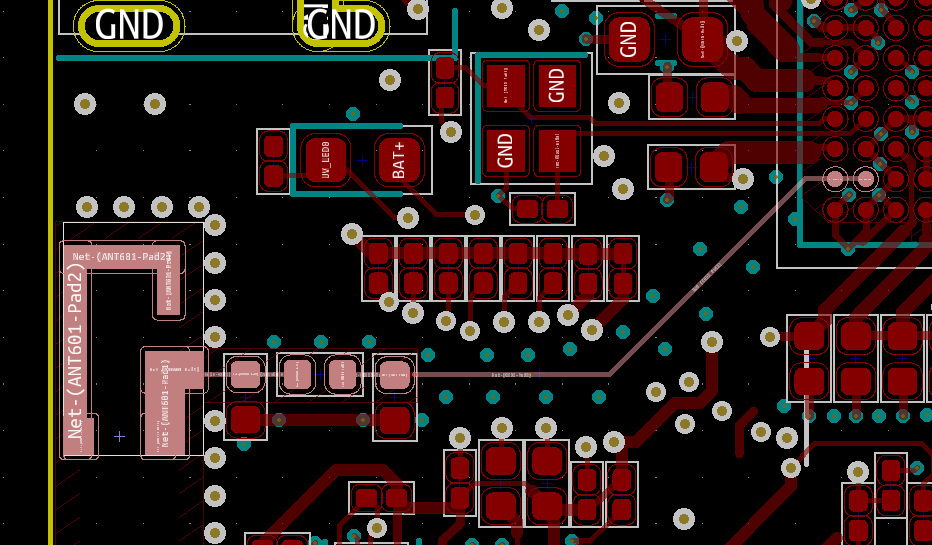
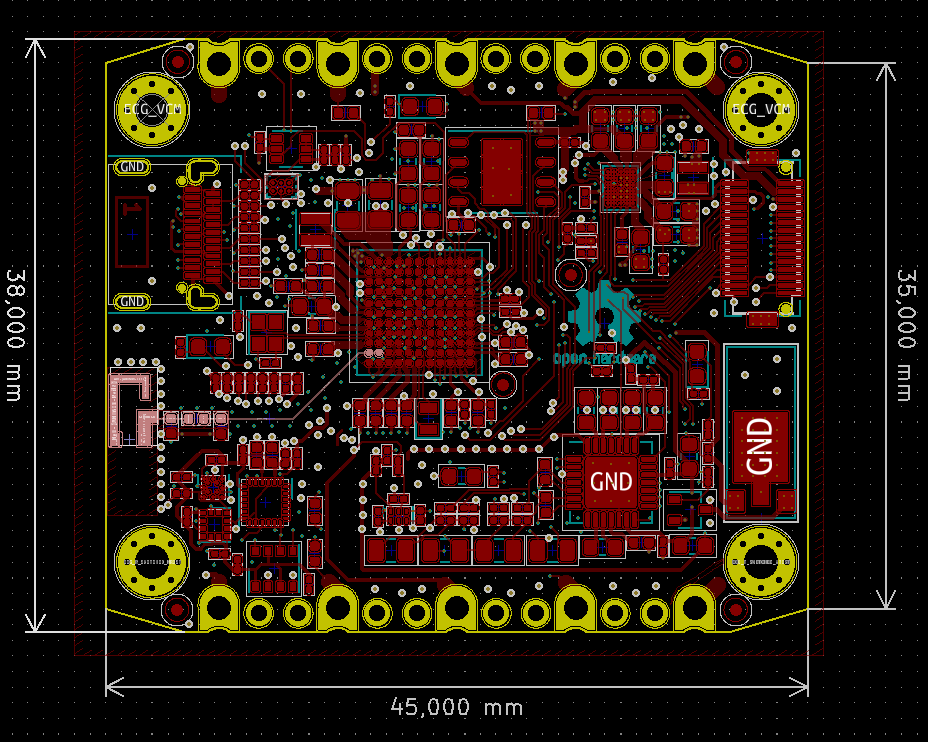
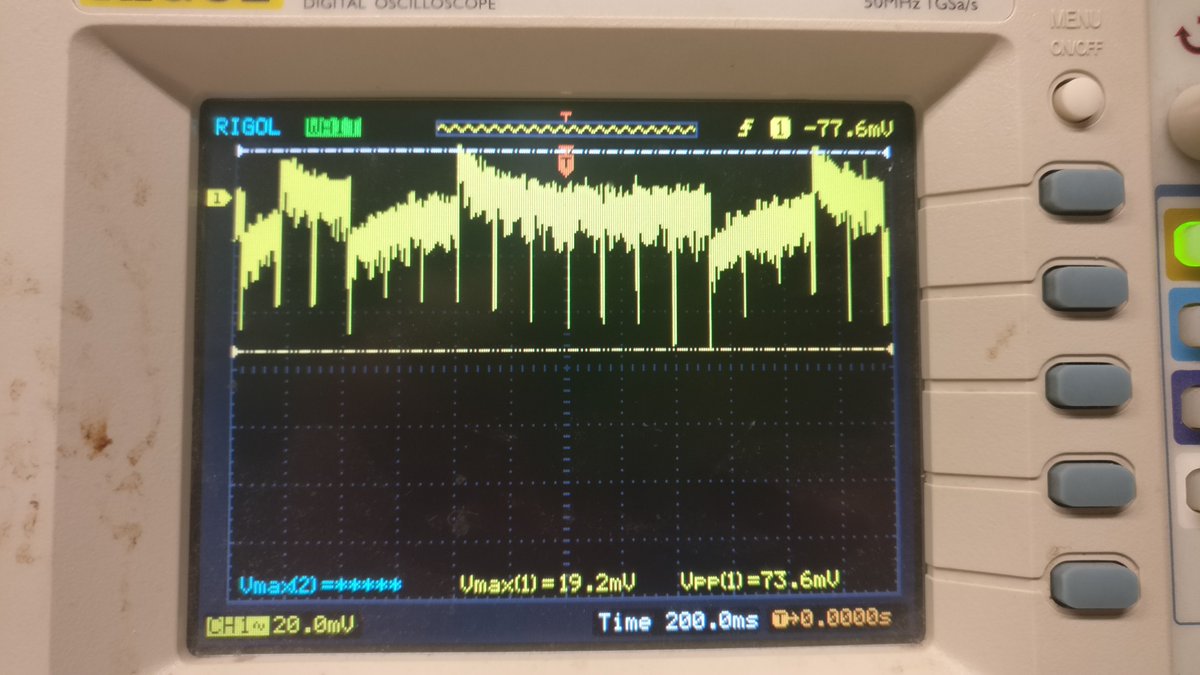
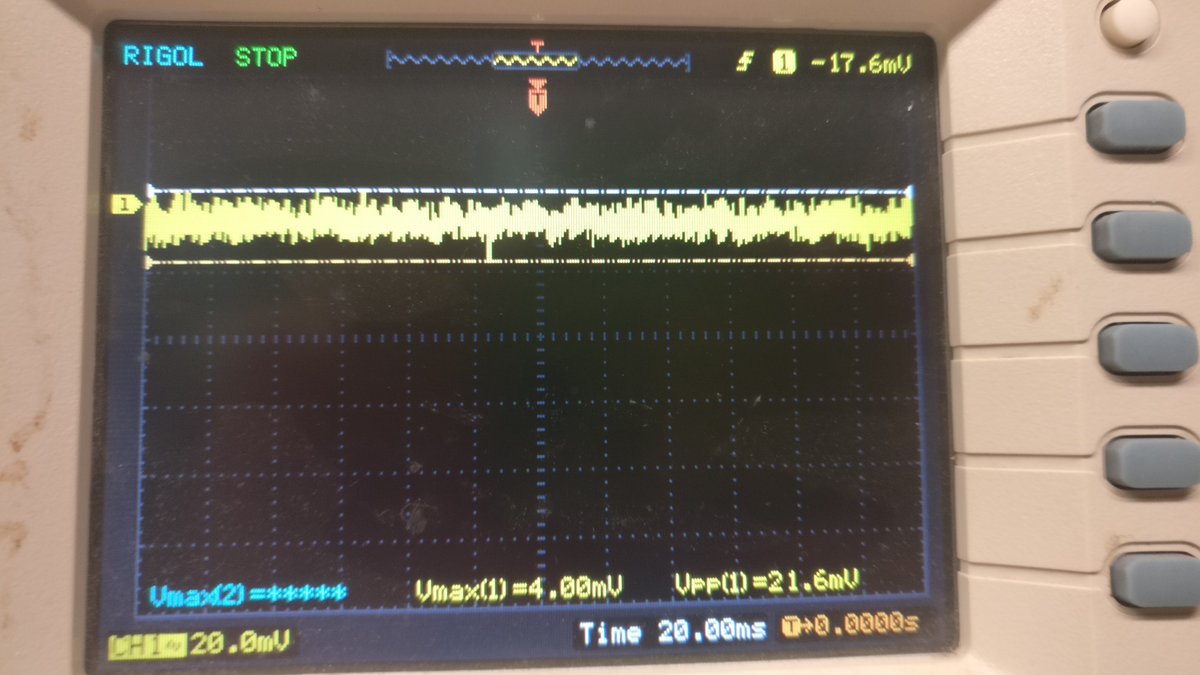
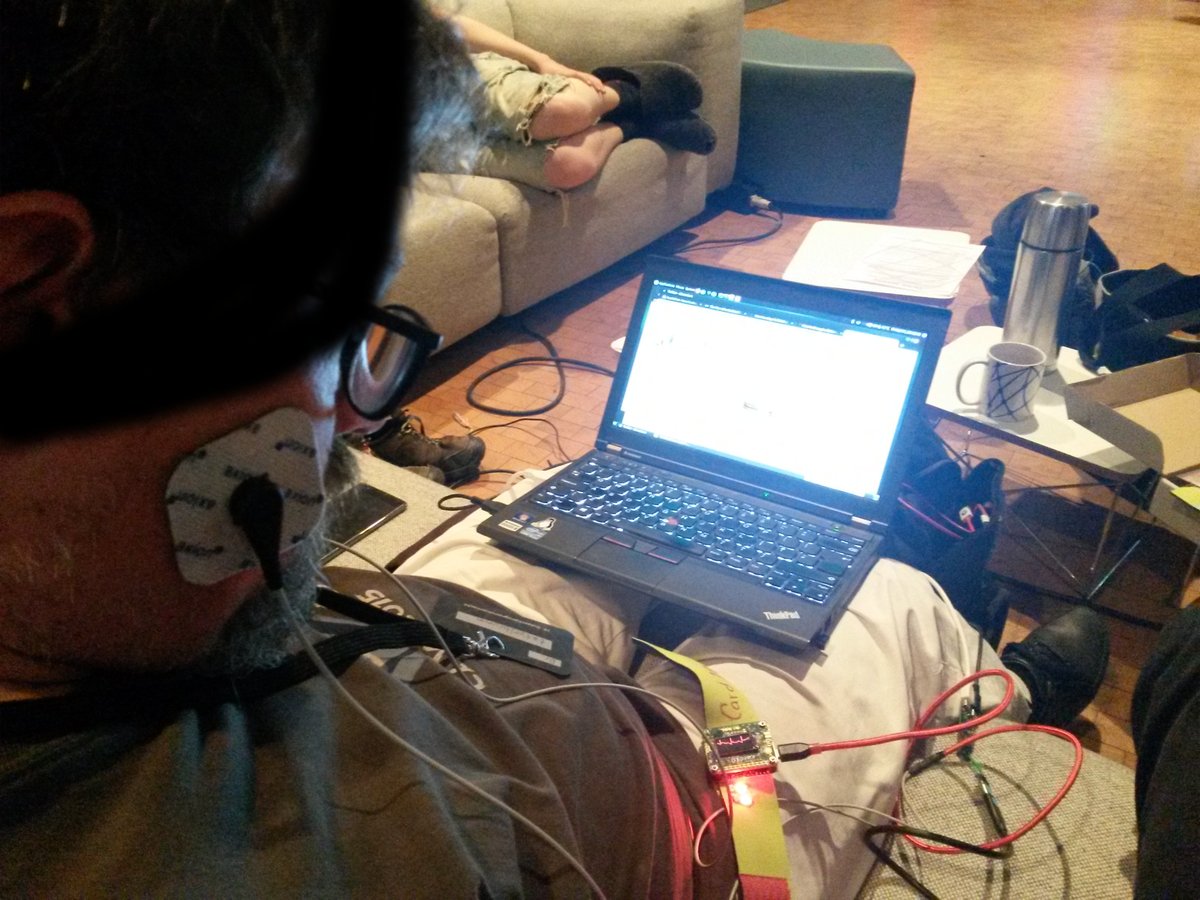
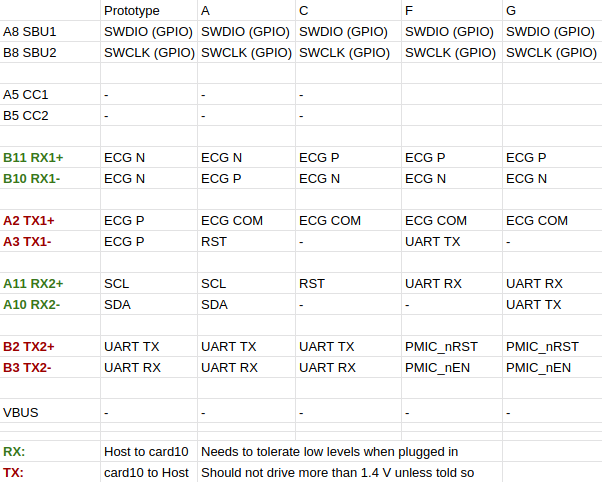

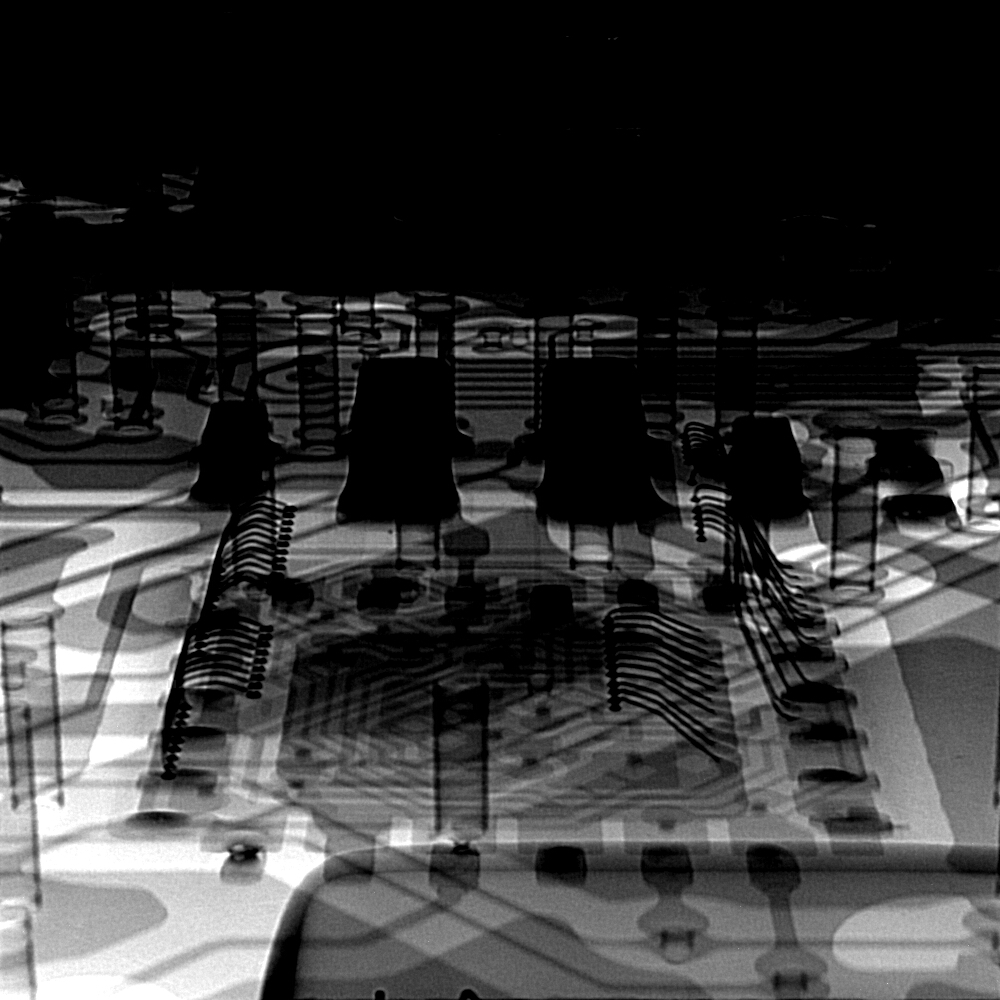
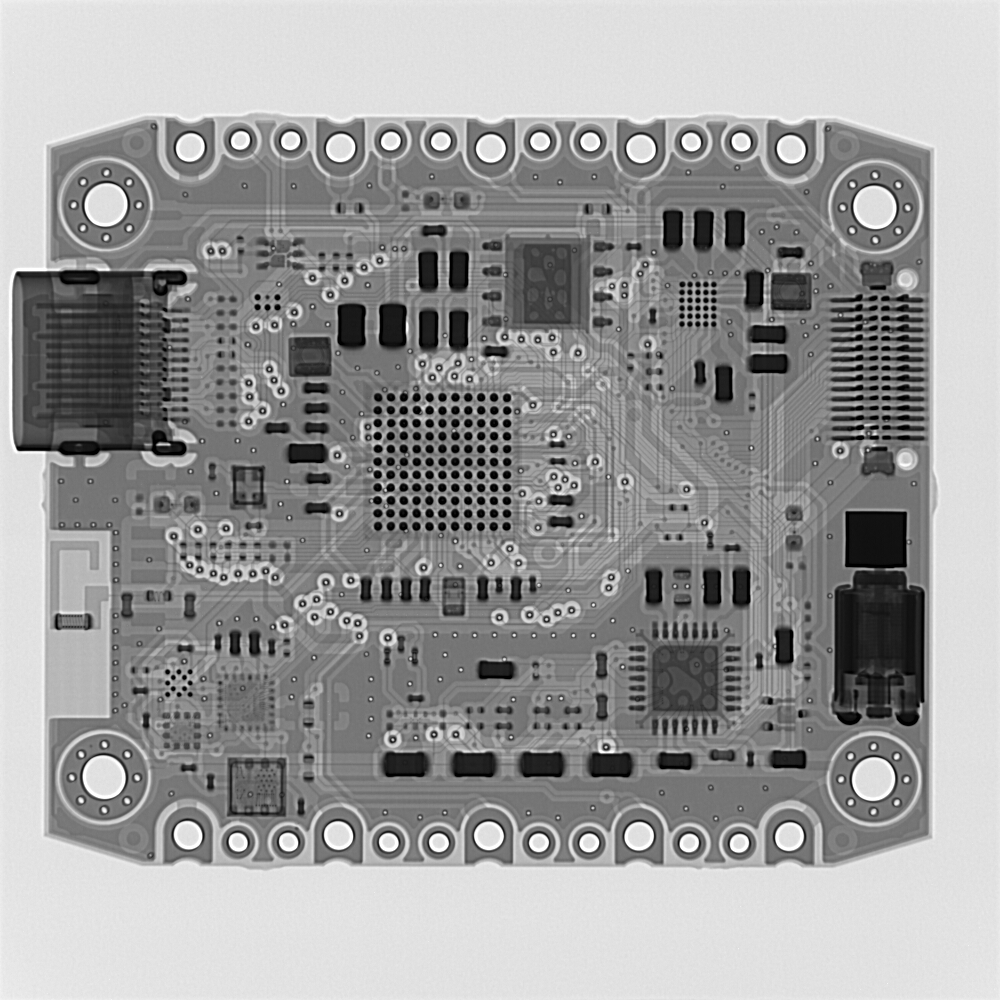
- Too little solder paste
- Voiding inside the solder joints
We figure that maybe the 80 um solder paste stencil really should have been a 100 um one. Maybe also bad handling during SMT
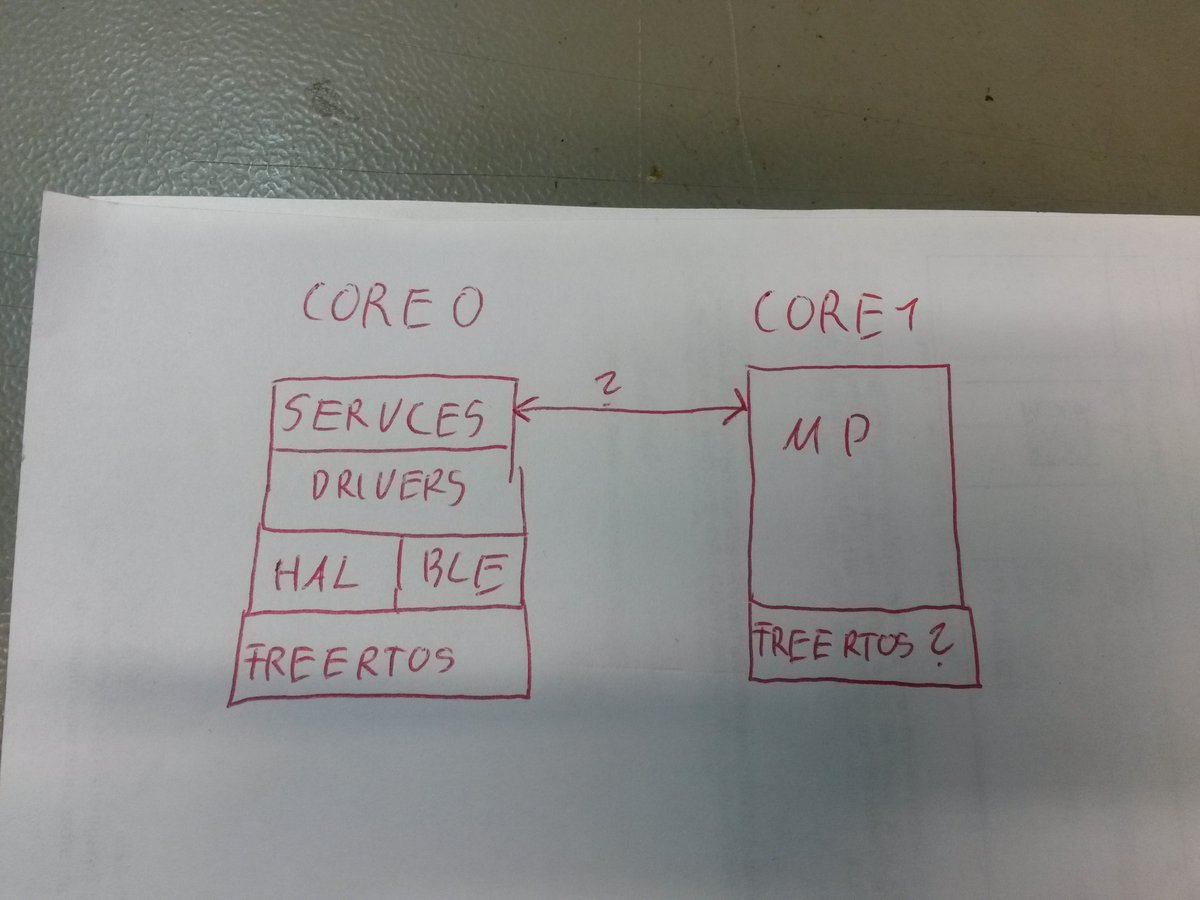
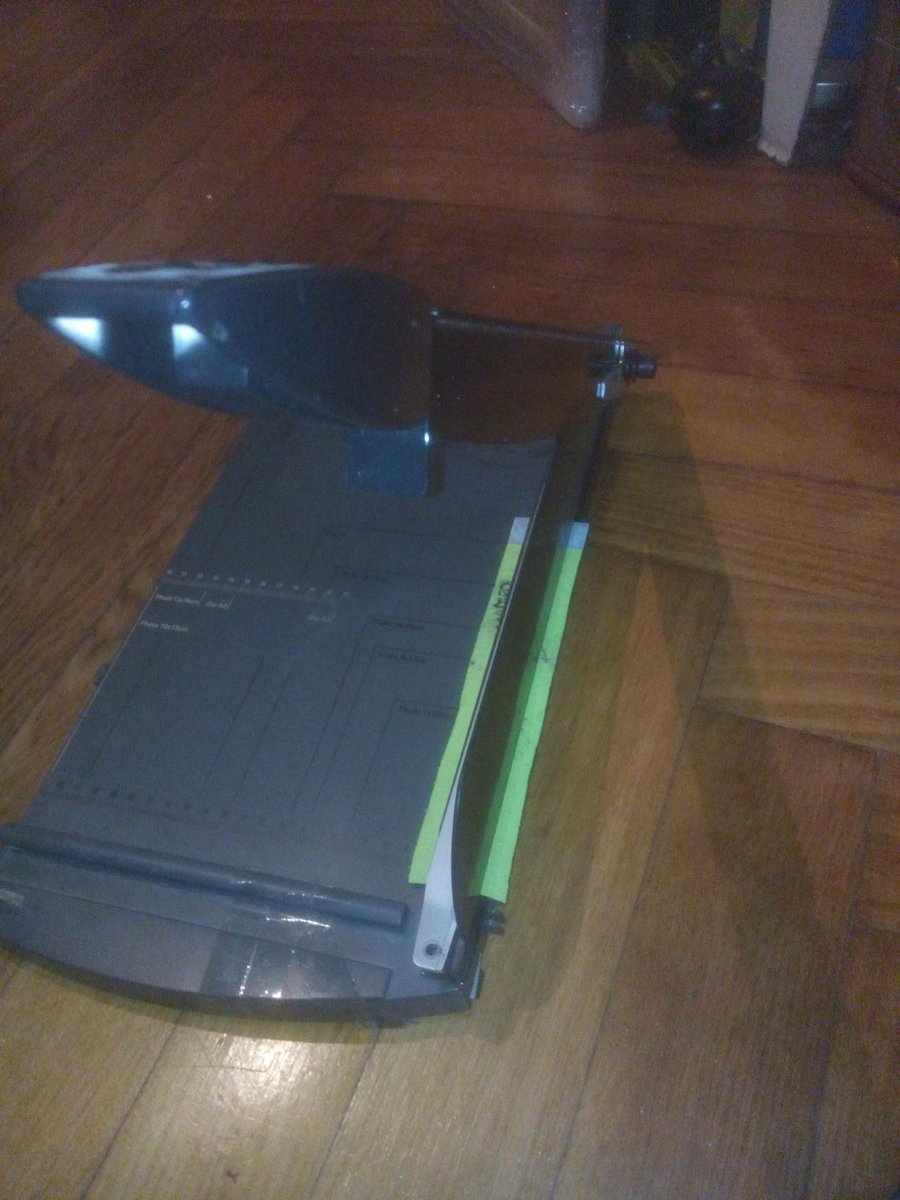
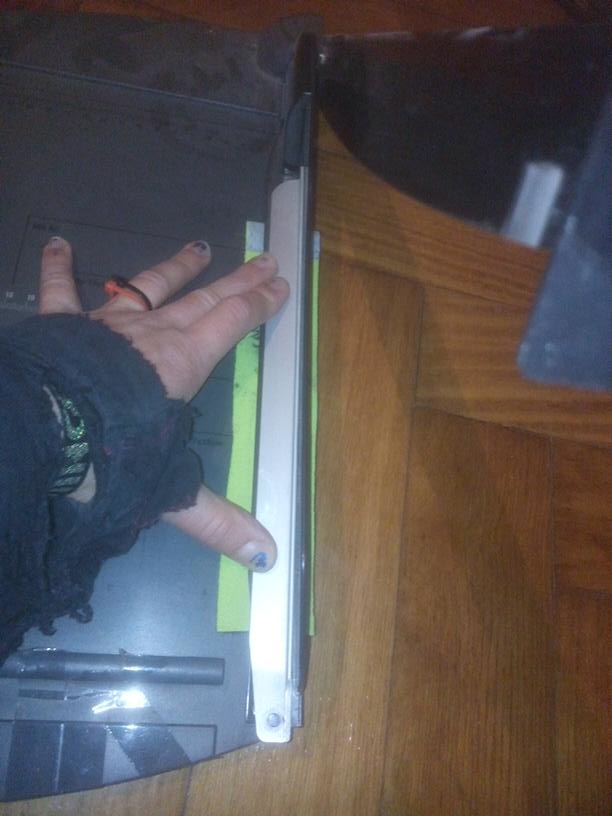
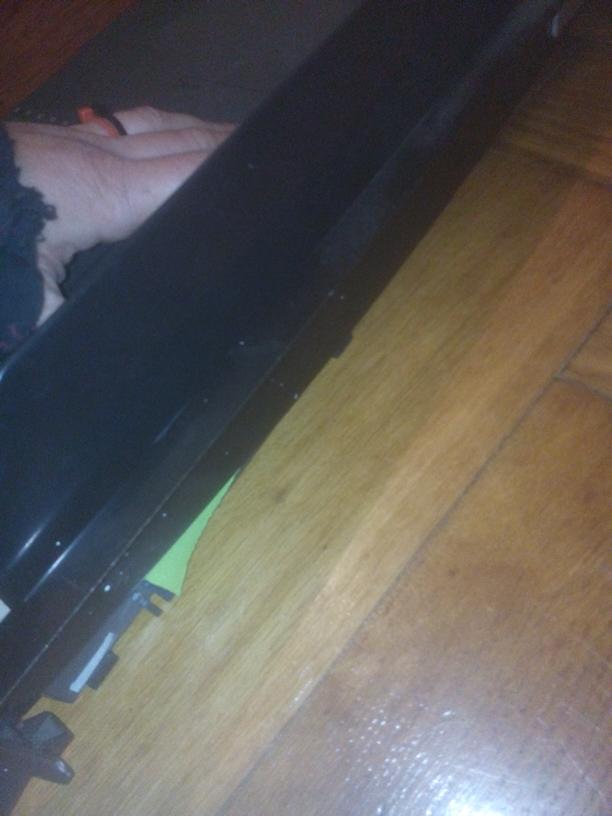
As usual we only send the Gerbers for a single board and a simple drawing for the panel.
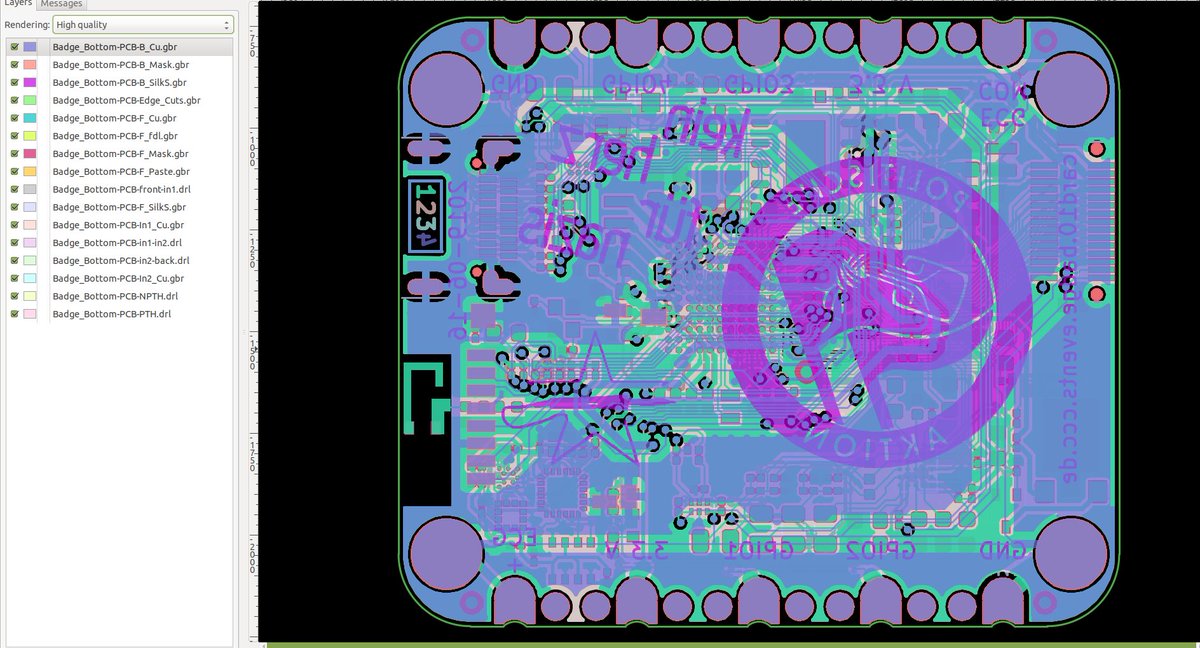
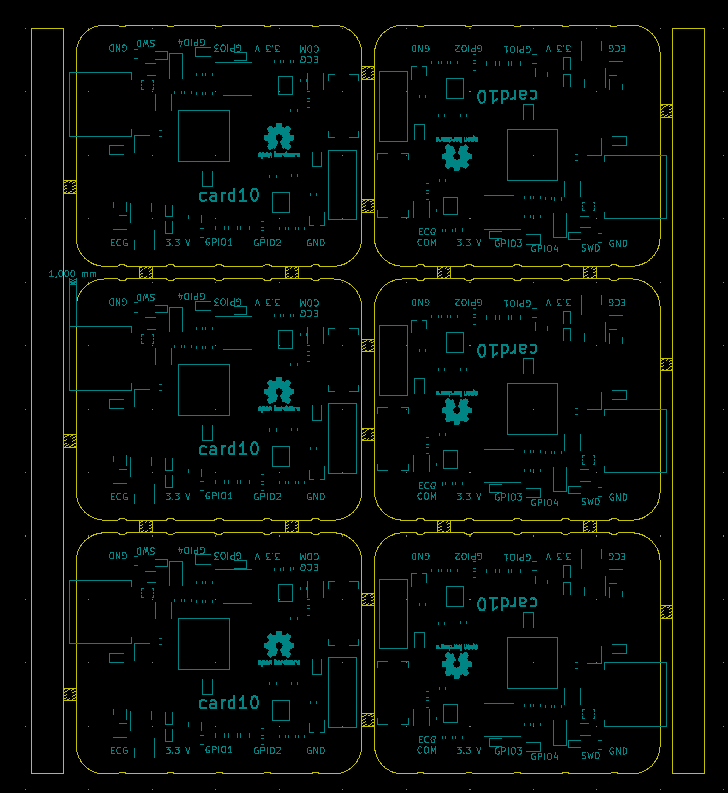
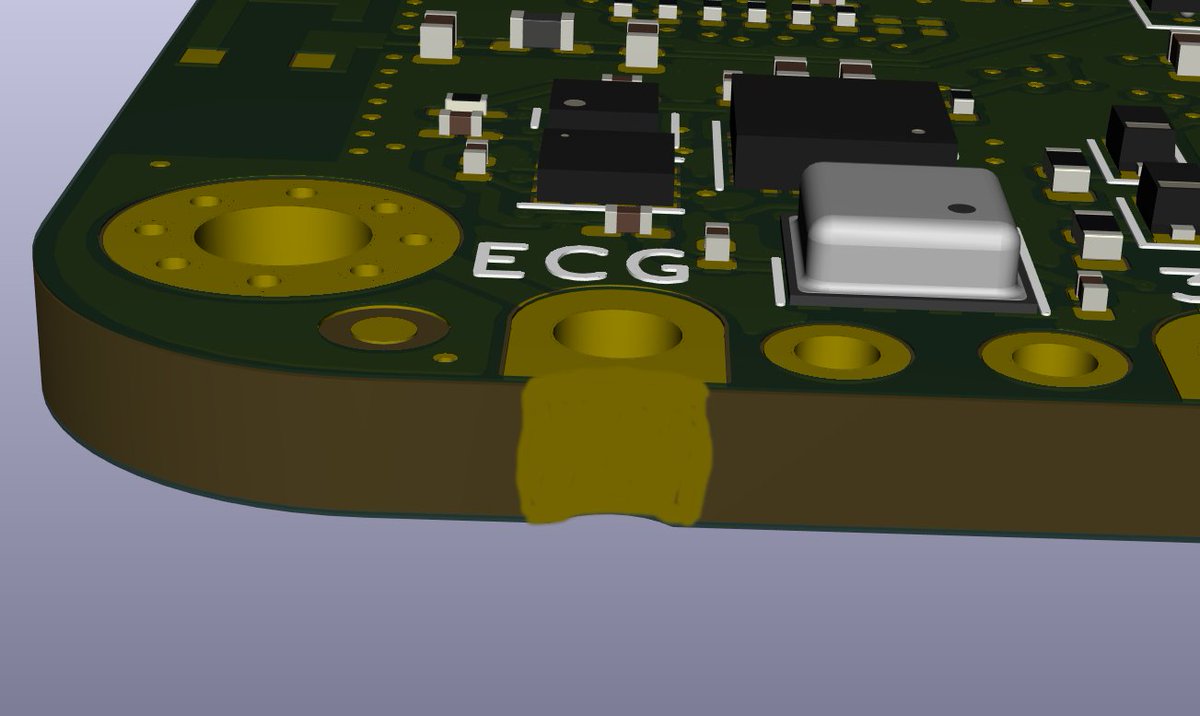
- The bypass diode hack
- A software switchable 3.3 V rail for low power operation
- Lots of 0 Ohm resistors for assembly variants
- The RGB-LEDs move from 3.3 V to the raw battery voltage
- Updated USB-C pinout
- ESD protection for the wirstband pins
- ECG chip changes from QFN to BGA
- Minor changes for better PCB yield
- Experimental windows above the LEDs of the bottom board
- Large pads for finger bases ECG measurements
- PPG sensor next to the ECG pads for blood pressure estimation
- New I2C port expander from @nxp
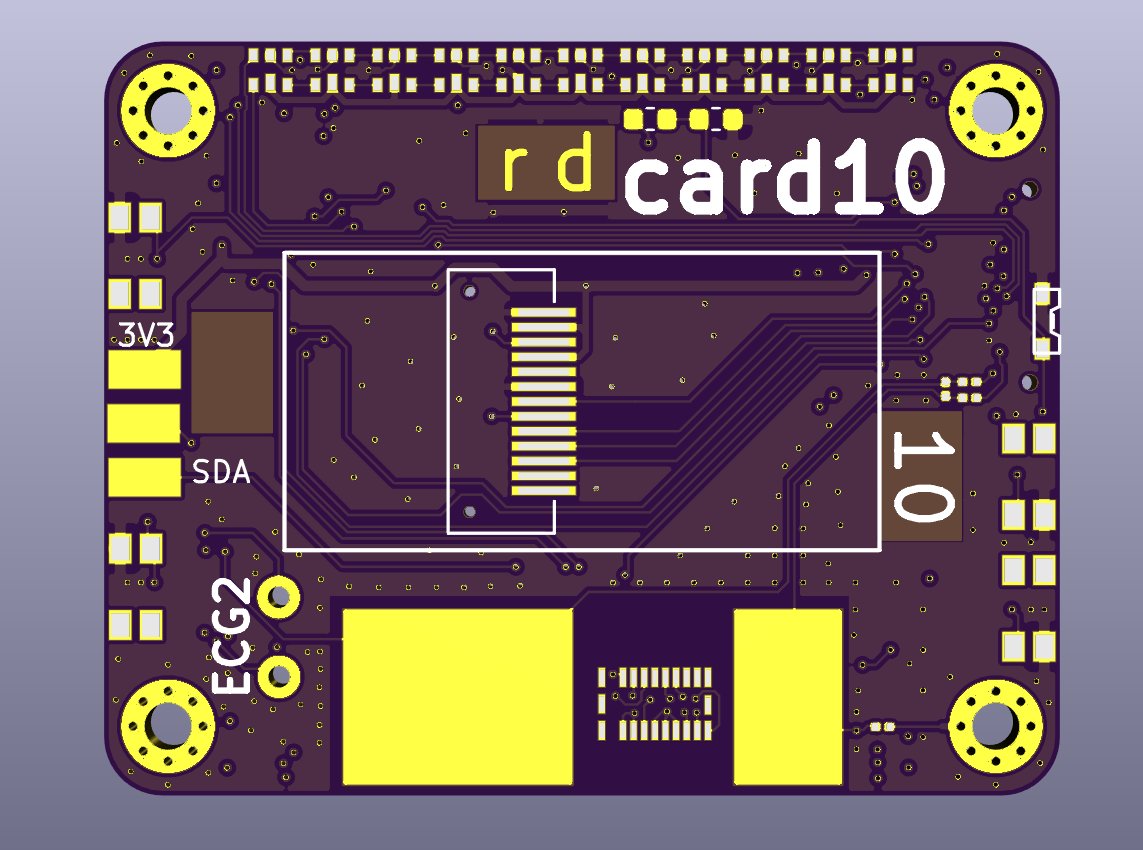
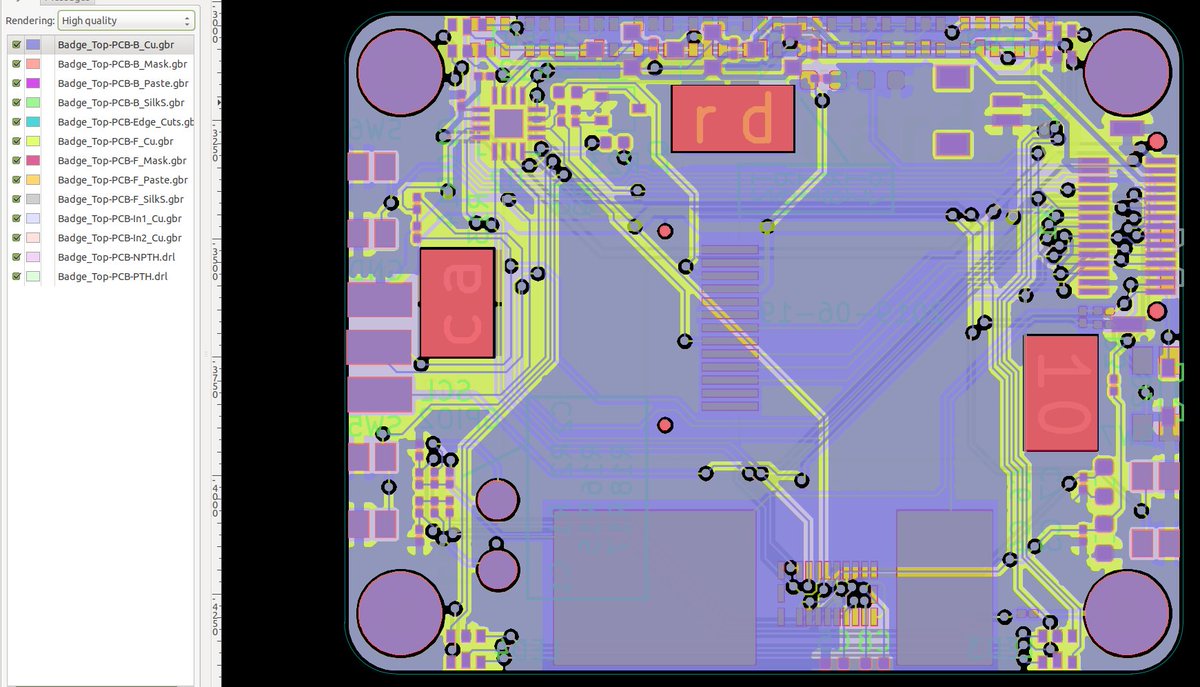
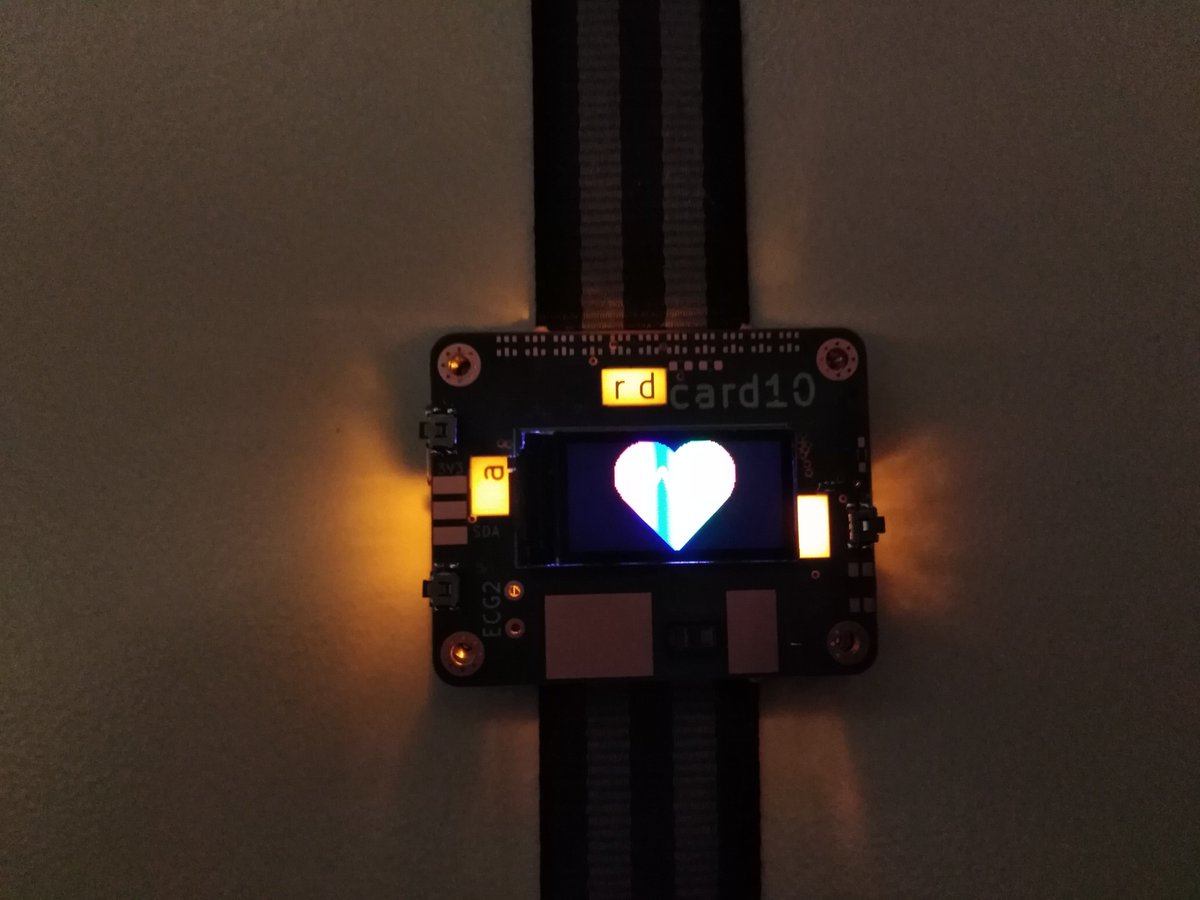
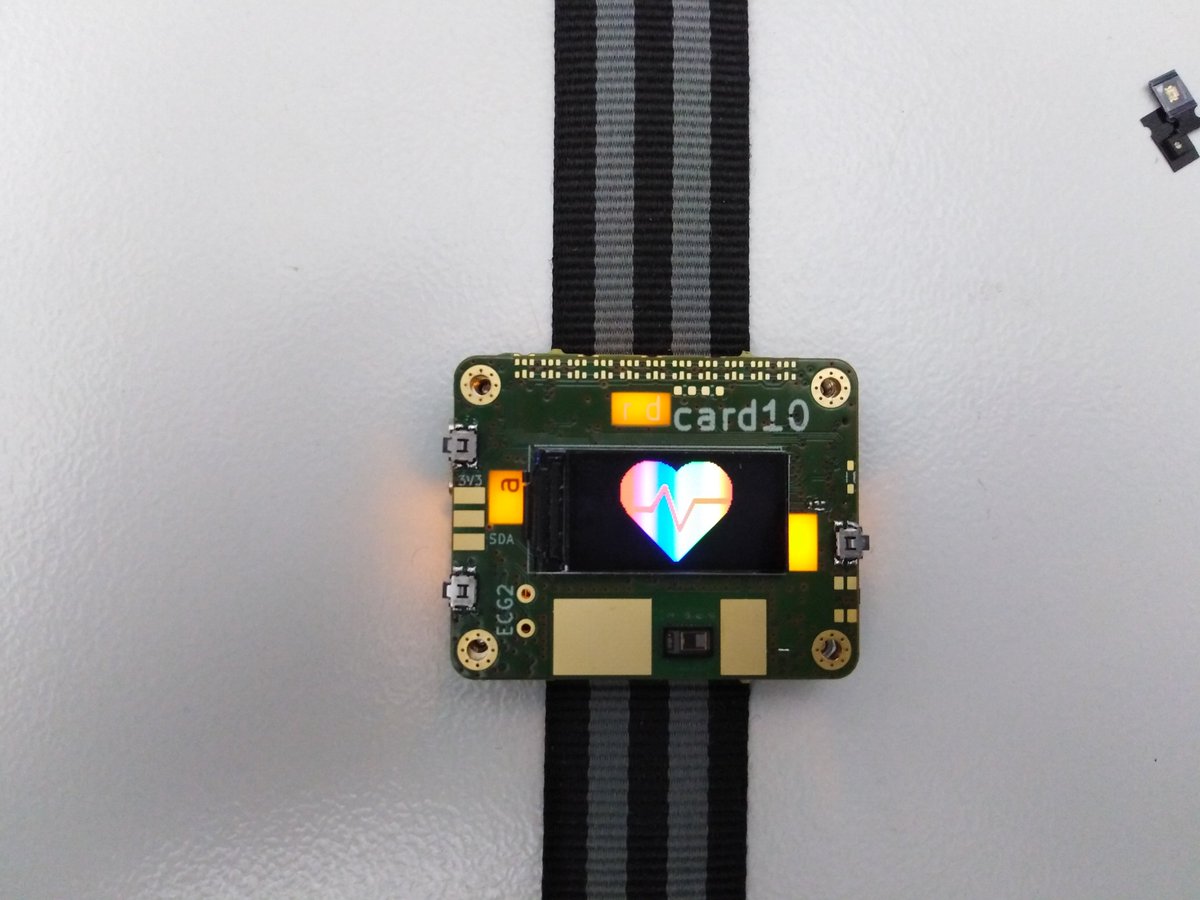
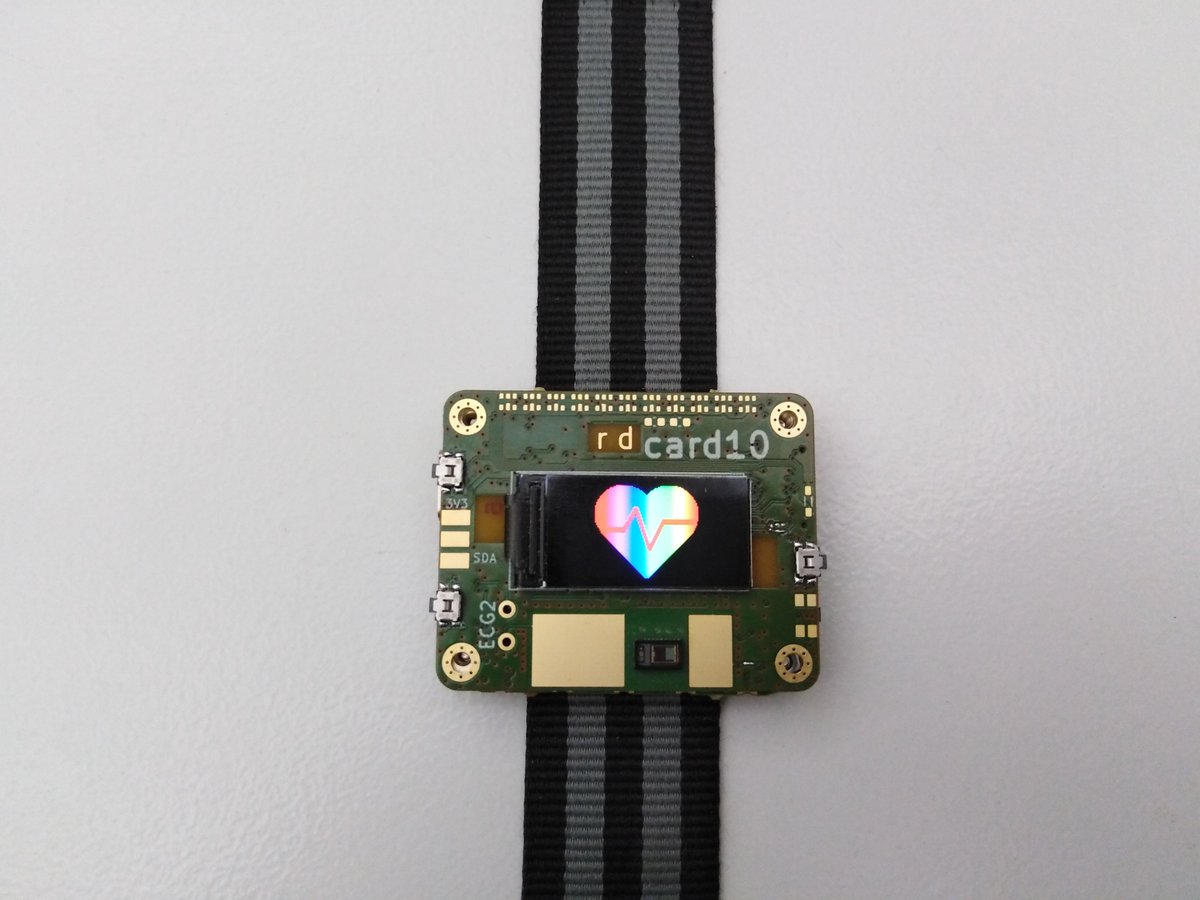
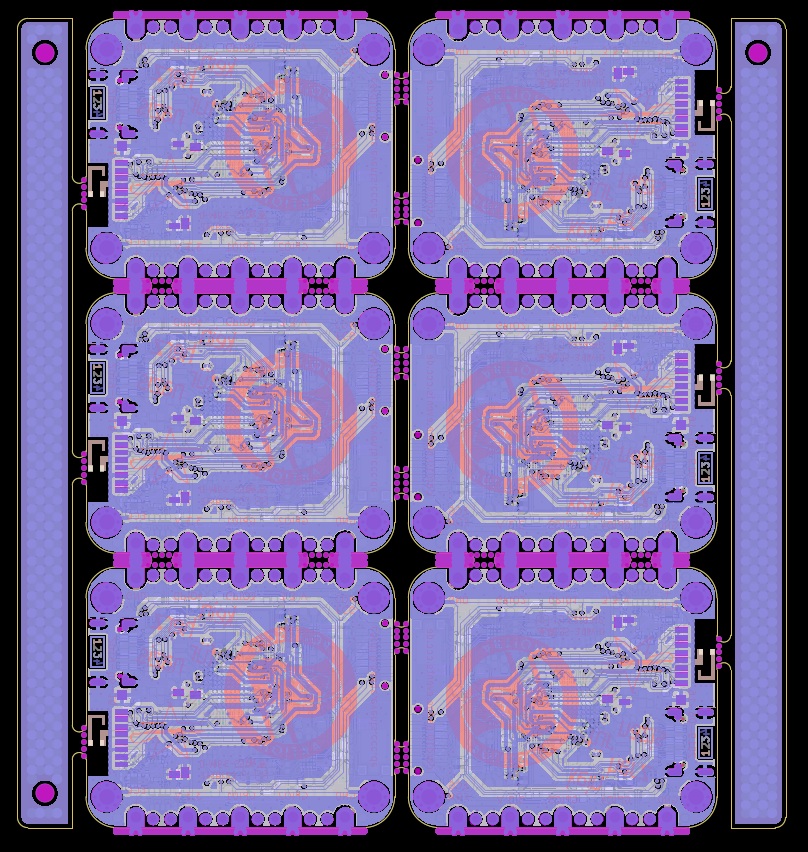
Our crystal dealer only has old stock from 2017 which we have to accept.
Only two days before #CCCamp2019!
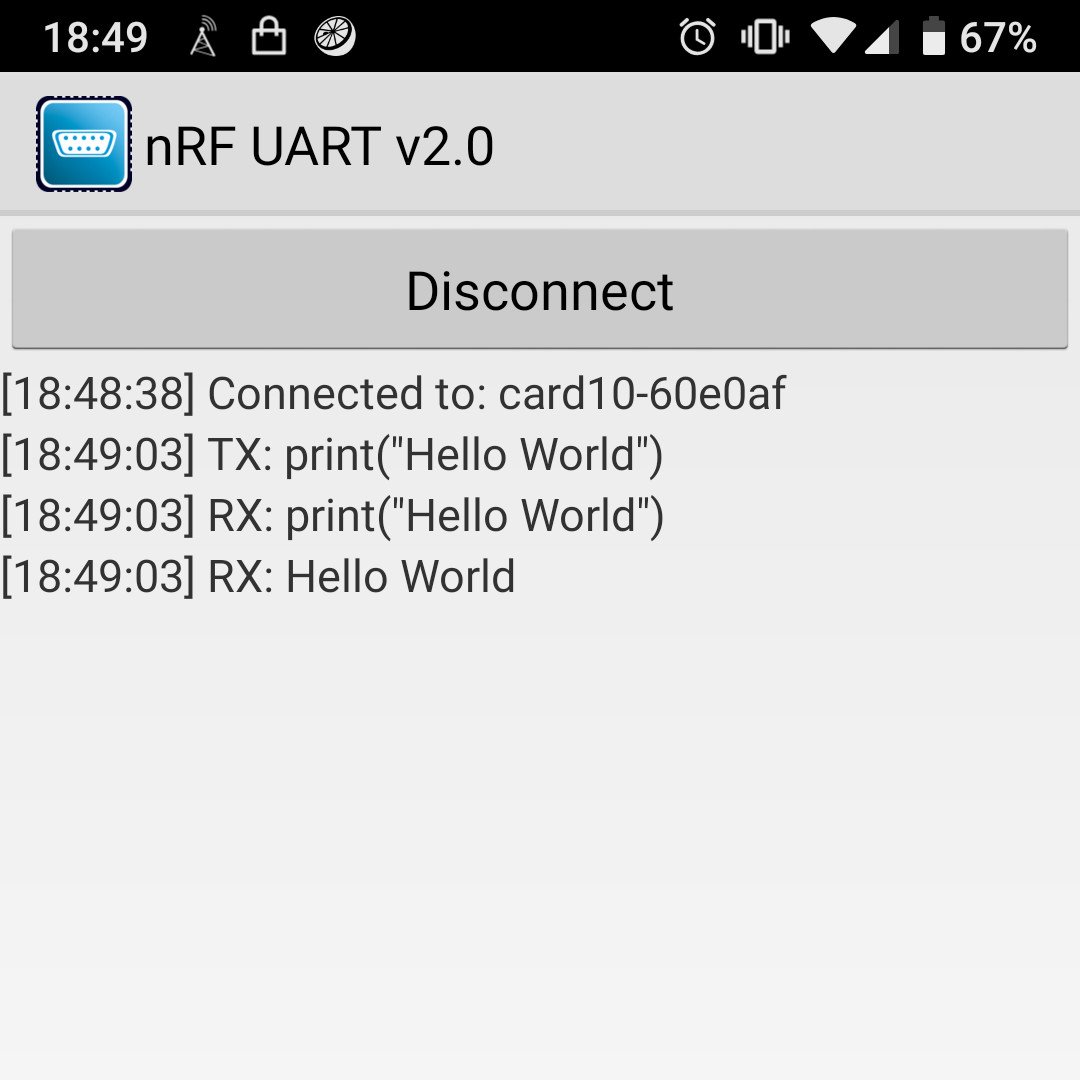
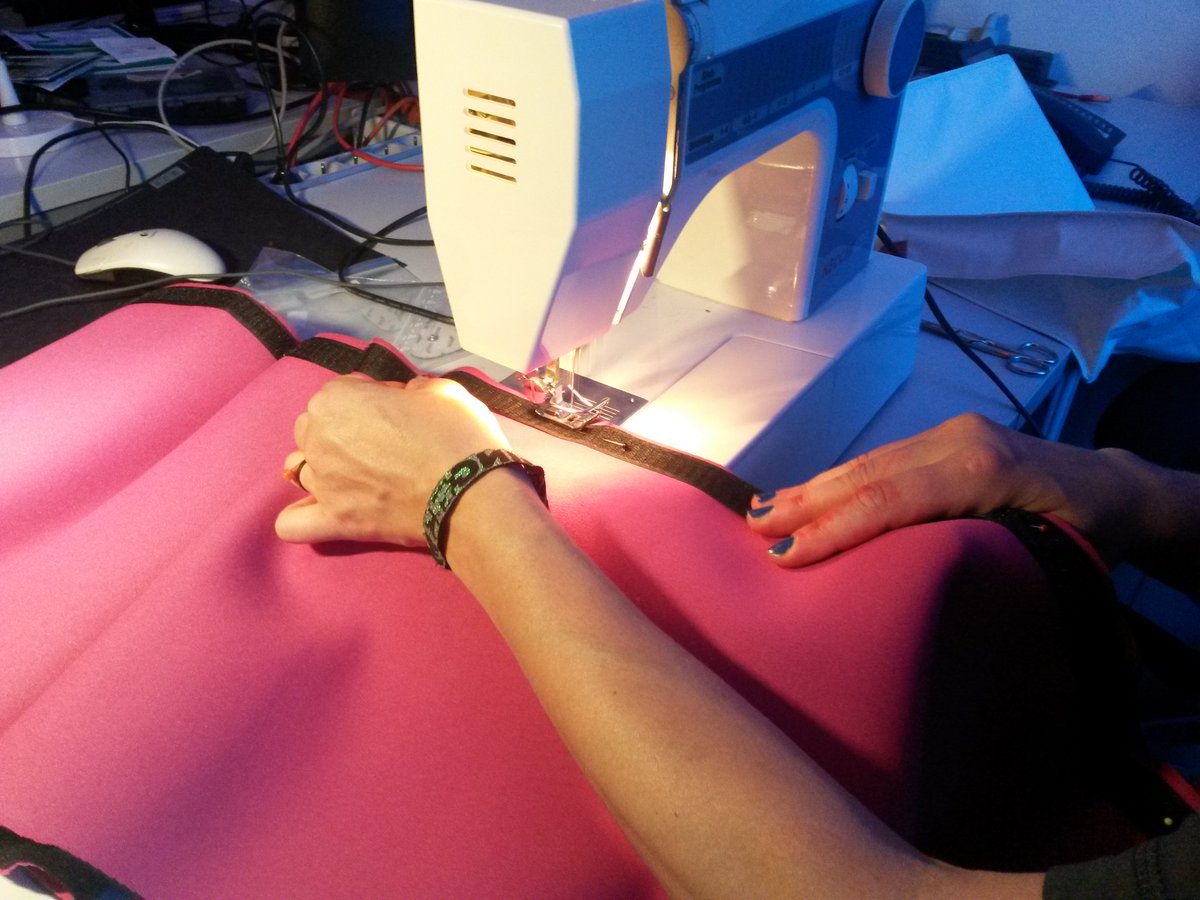
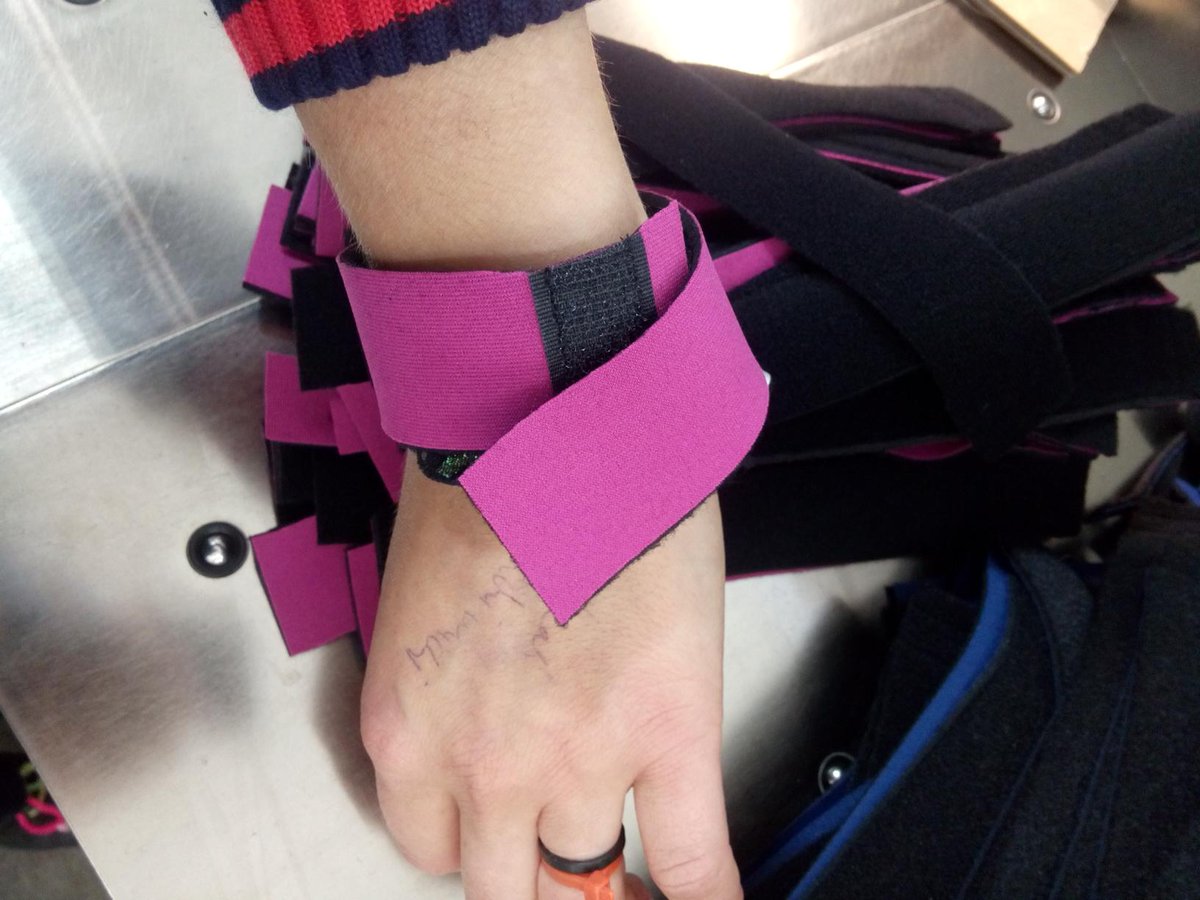
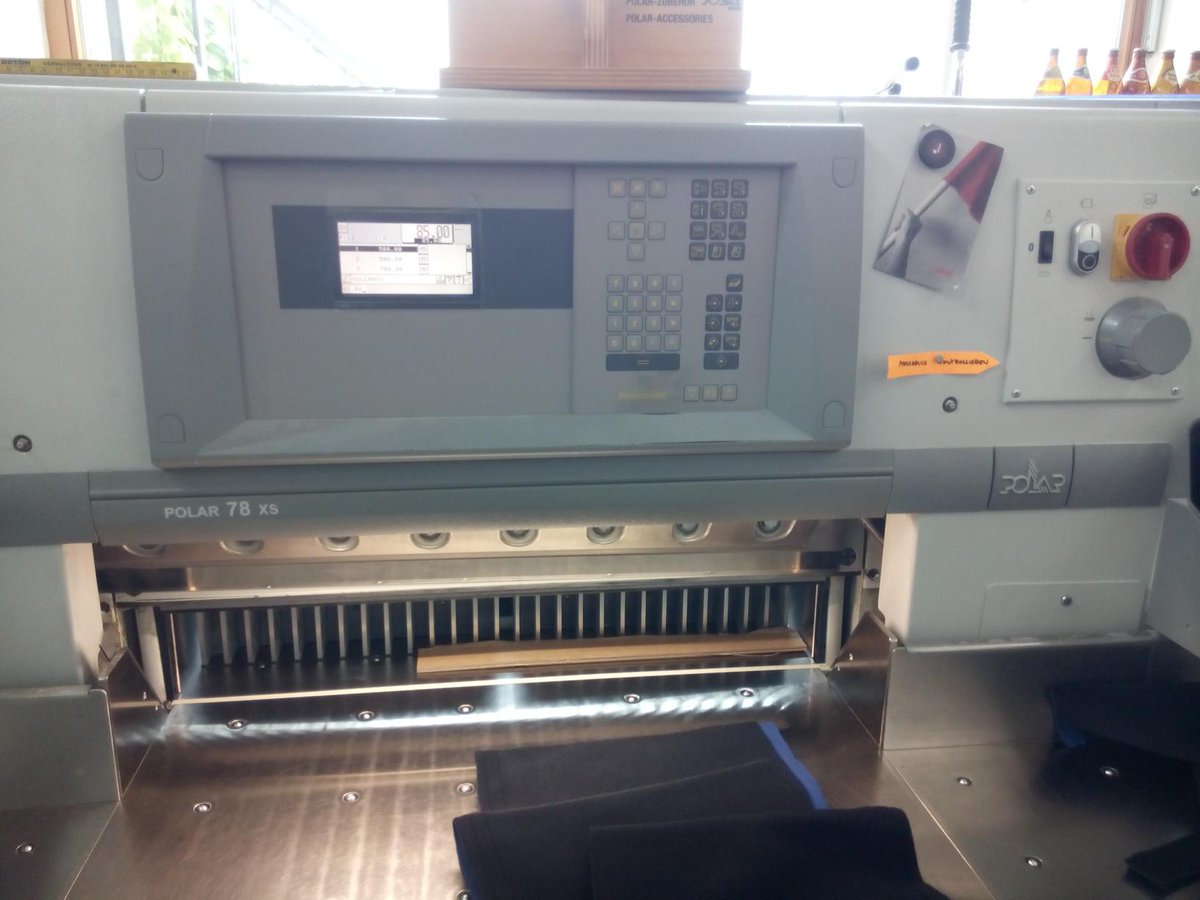
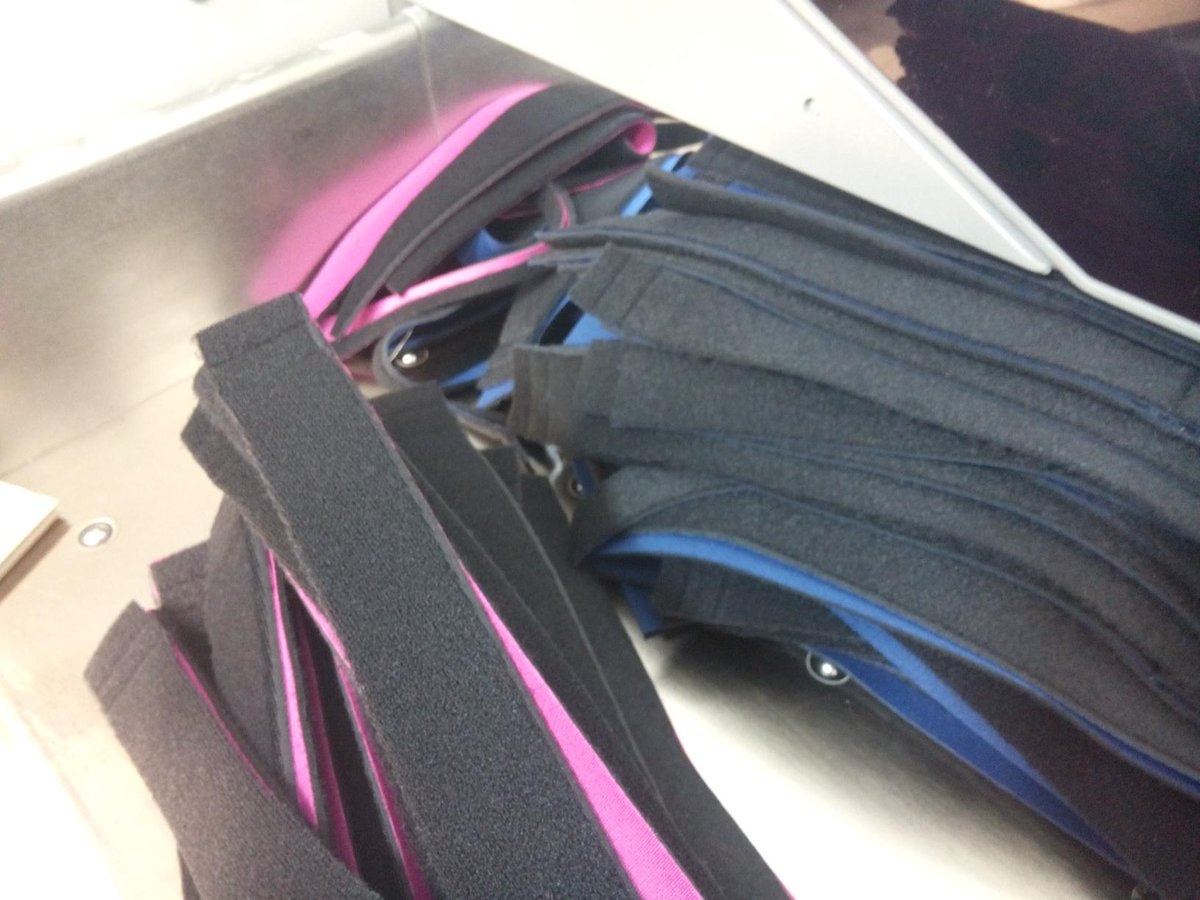
The problem: The tracking number we got is for a shipment addressed to someone else!
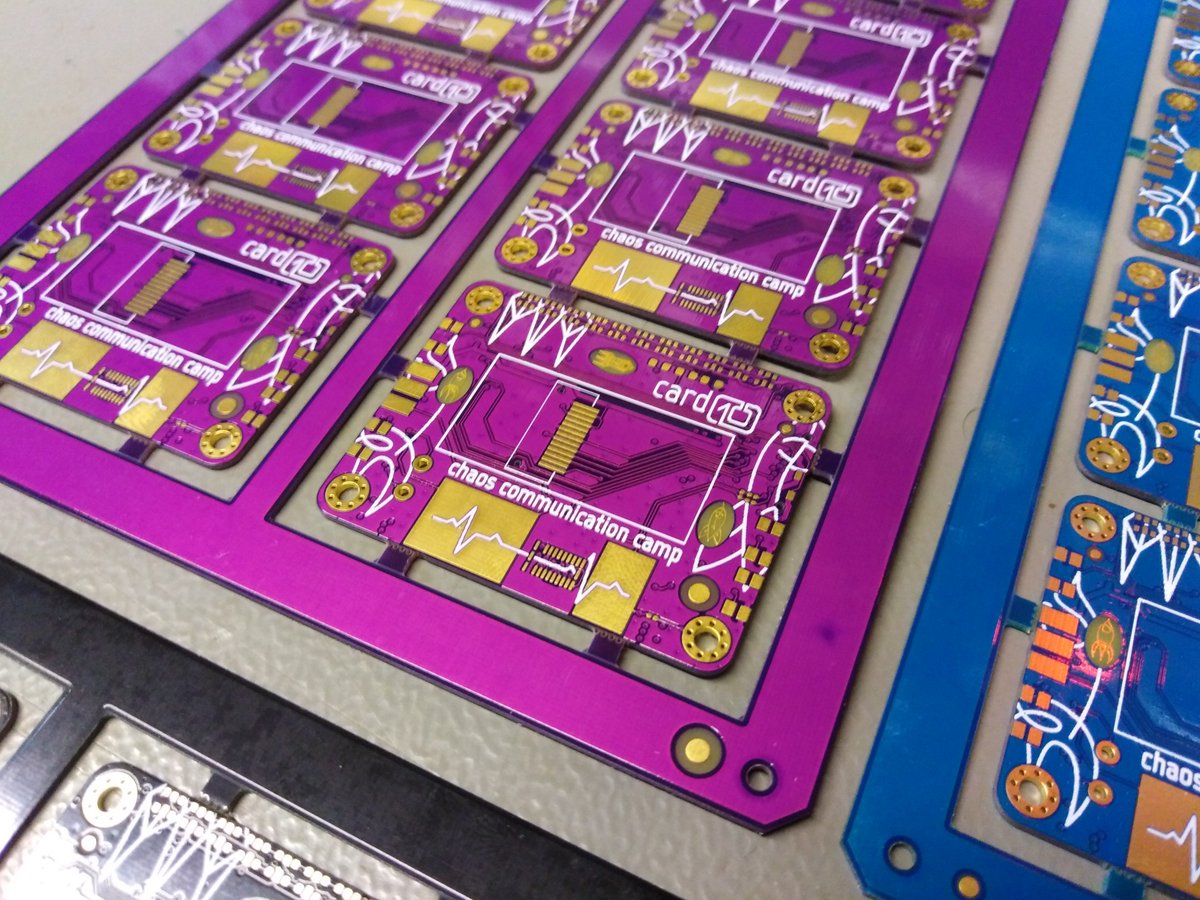
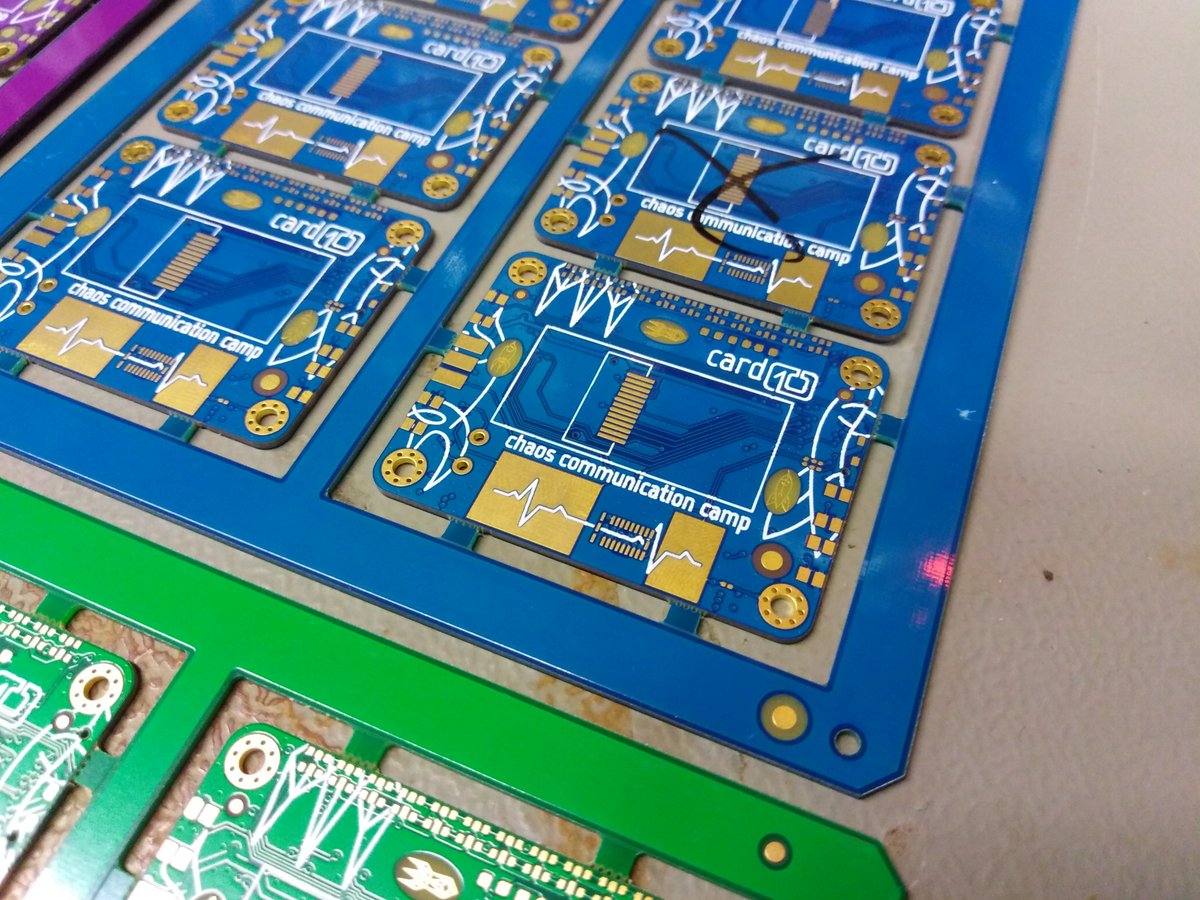
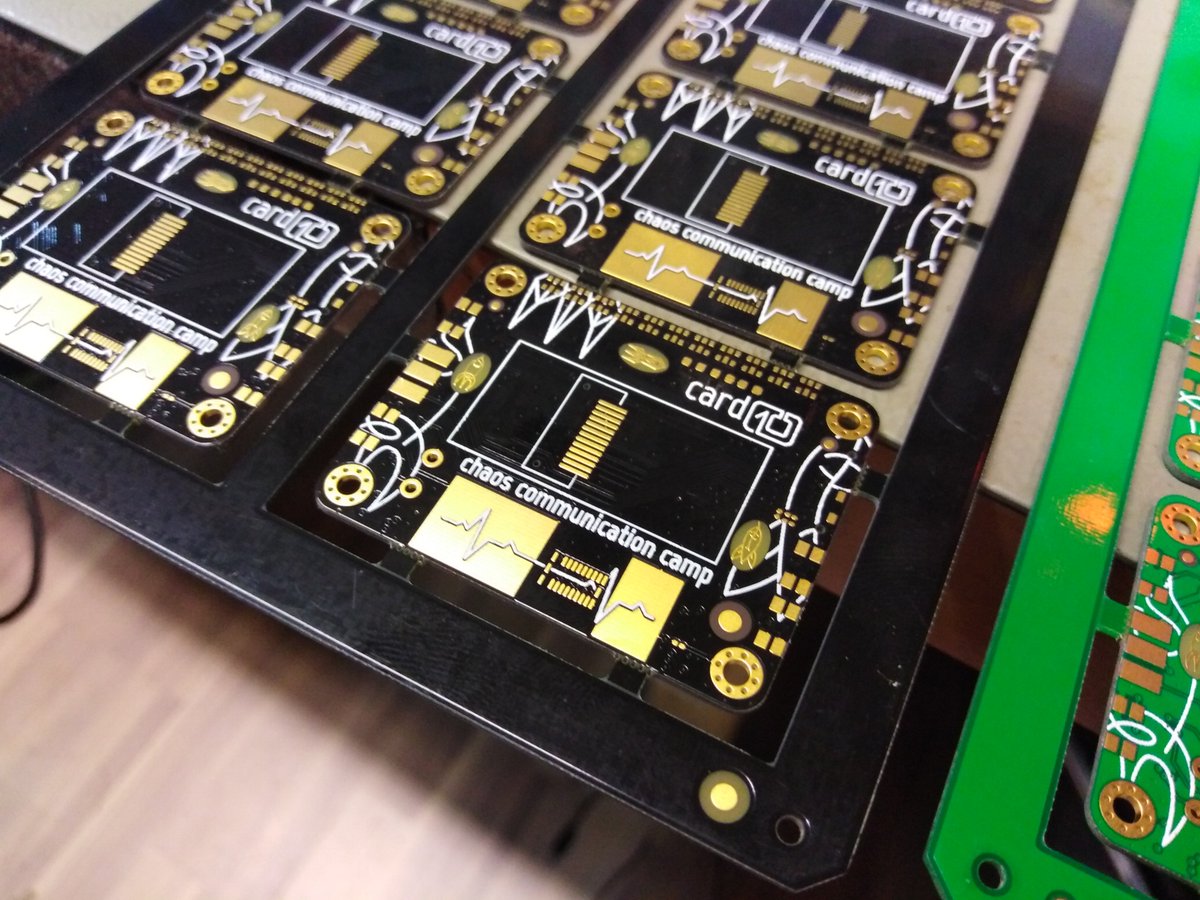
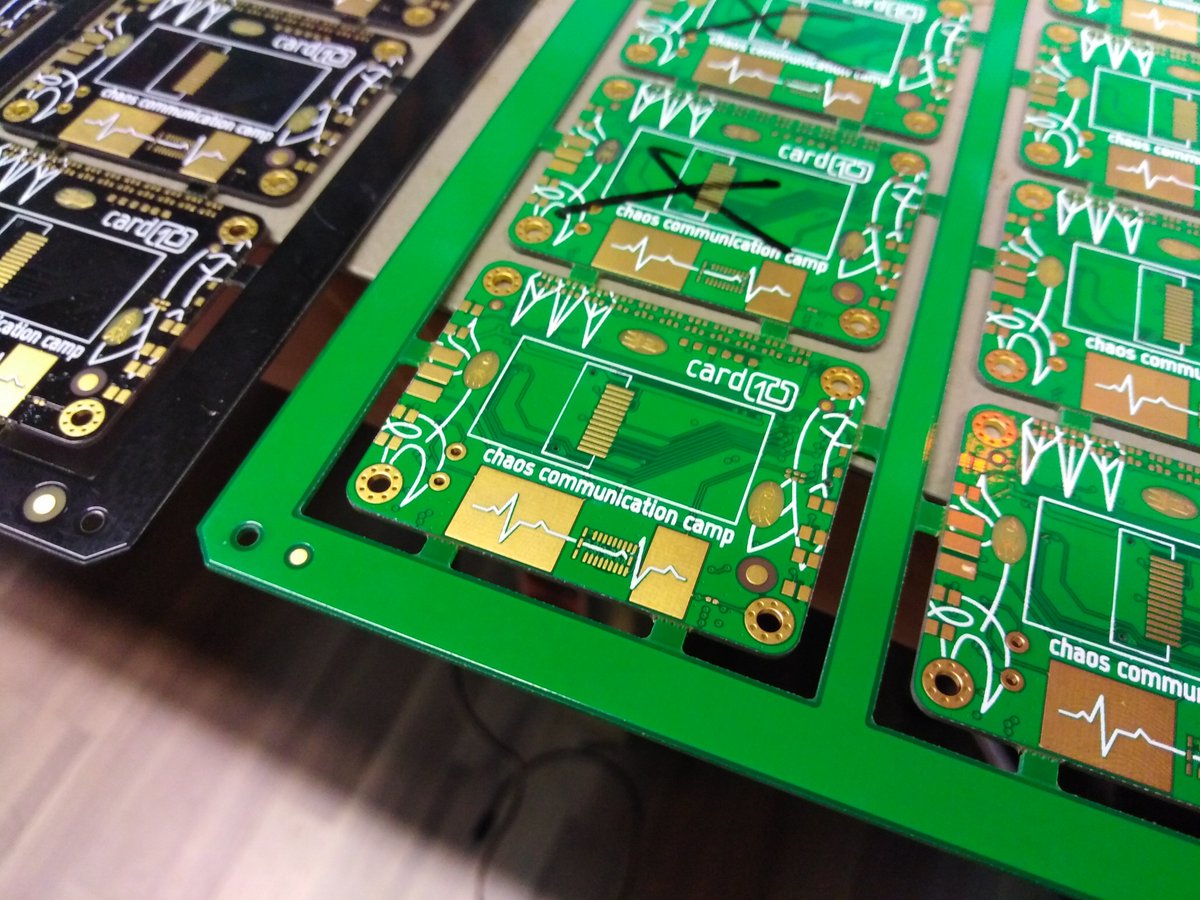
- Talk to our CM. Again.
- Try to get (at least some) CPUs earlier.
- Think about creative ways how to emergency assemble the CPU by hand at camp.
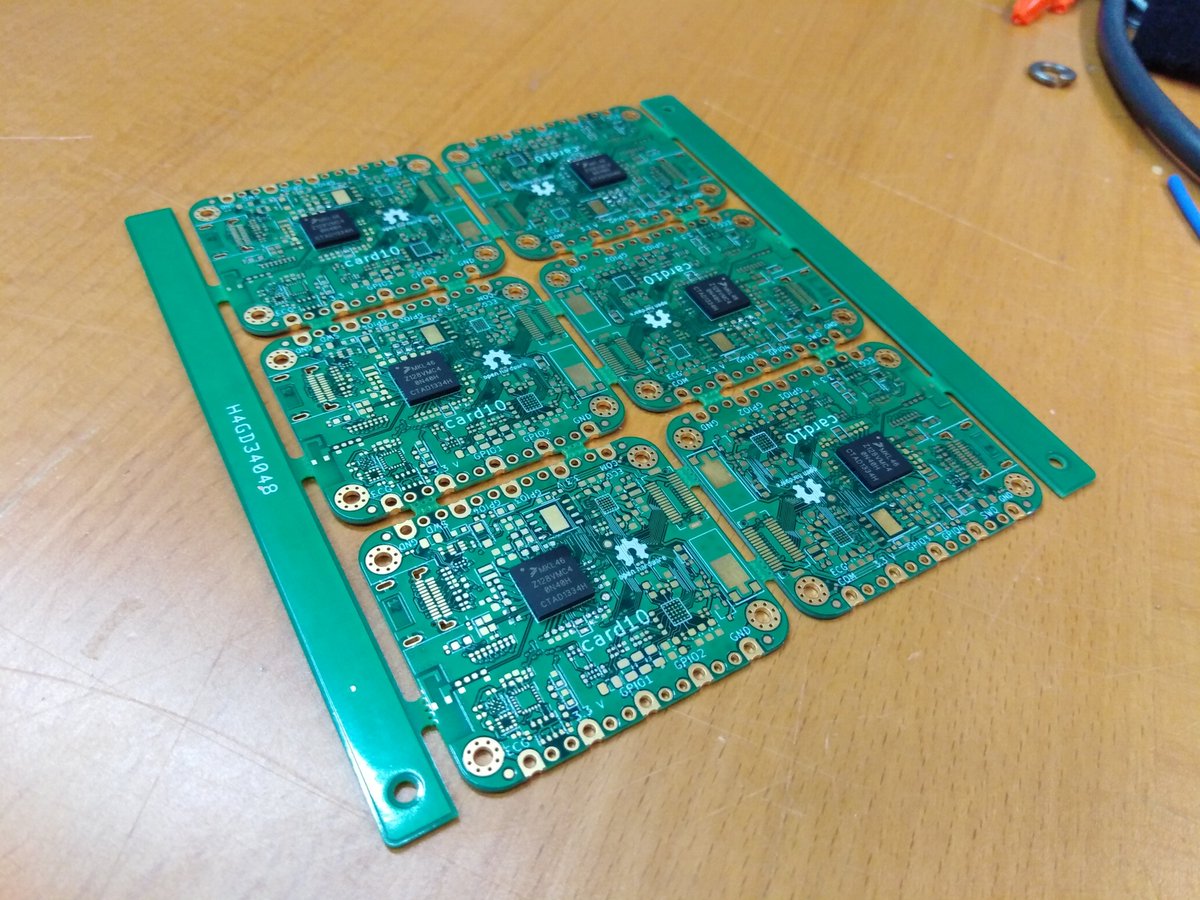
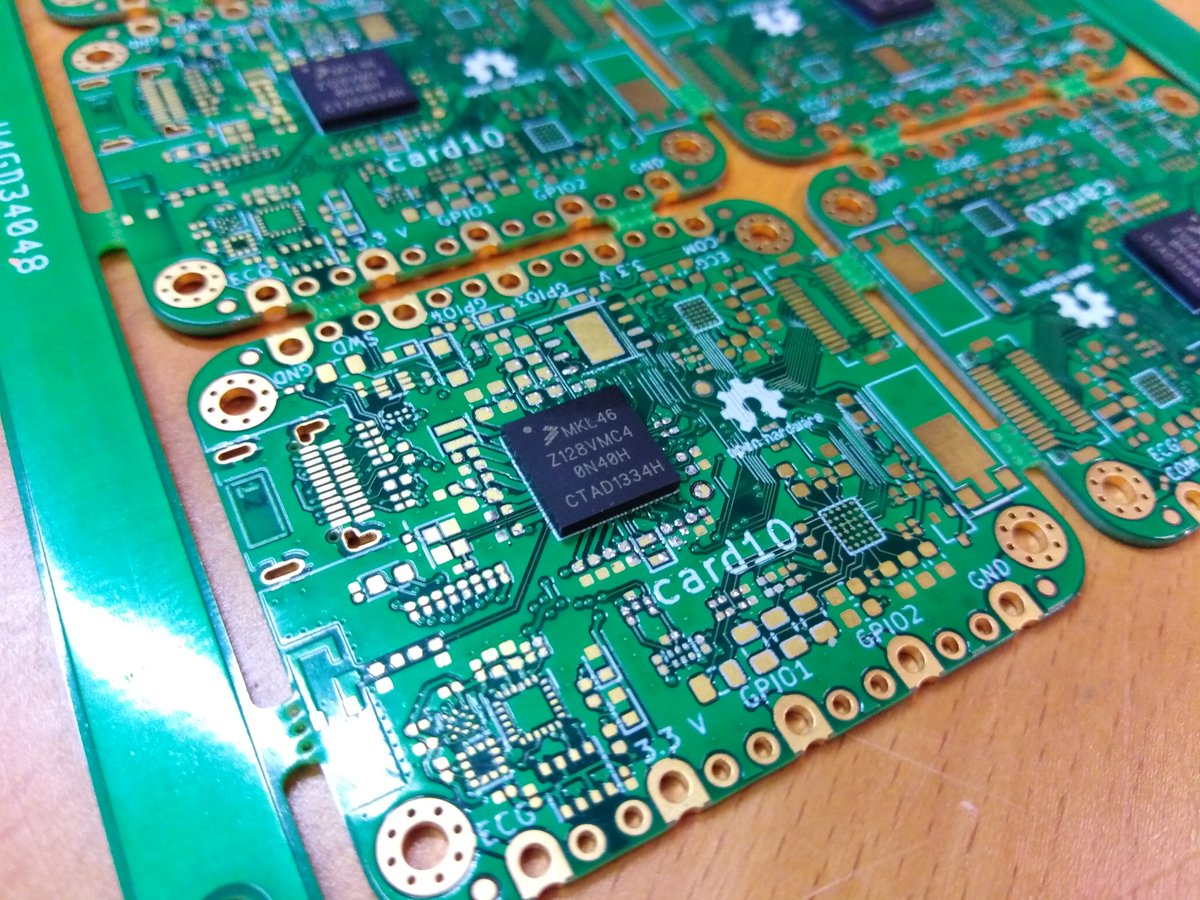
Thanks to a very dedicated team at @maximintegrated we will get a drop shipment directly from the IC test house in Taiwan to reduce shipping time. Next steps: Preparing customs/compliance documents so that there are no surprises.
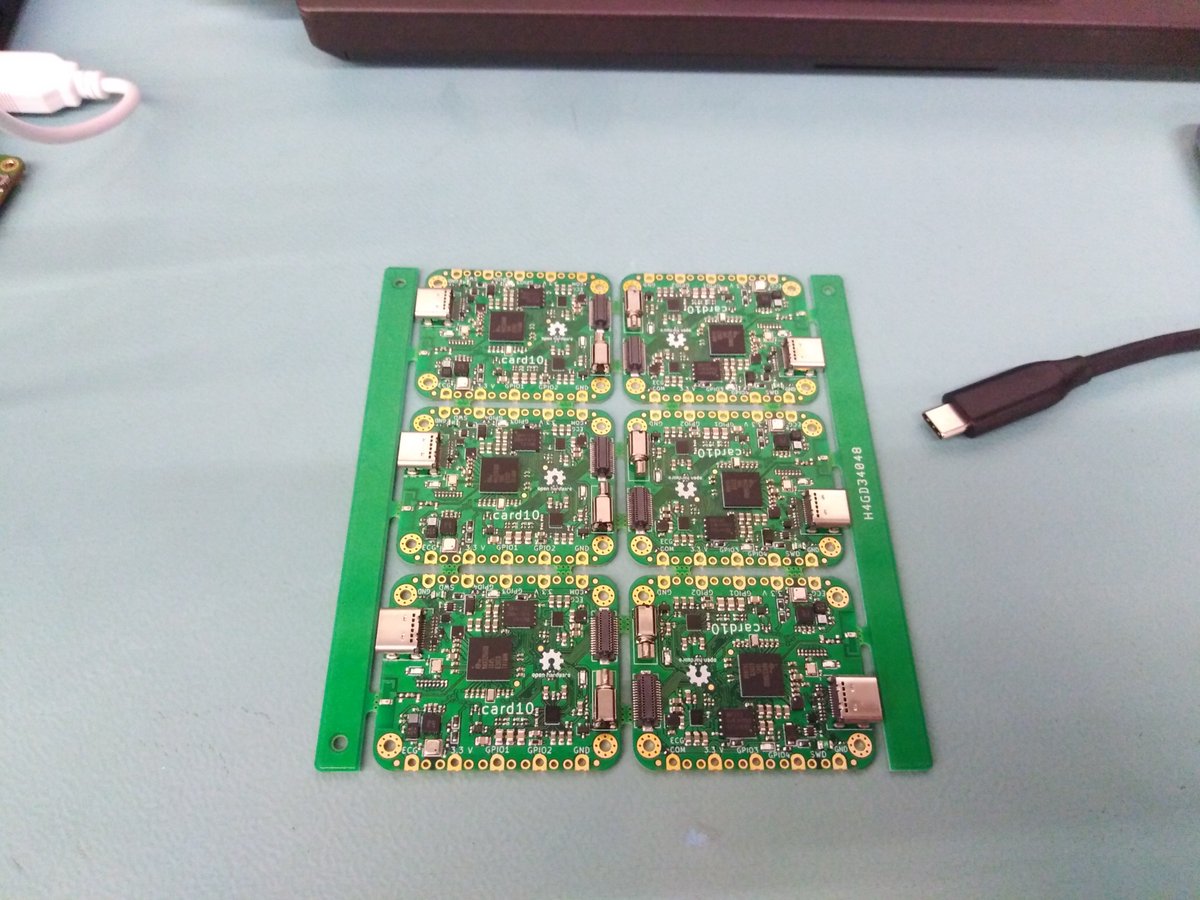
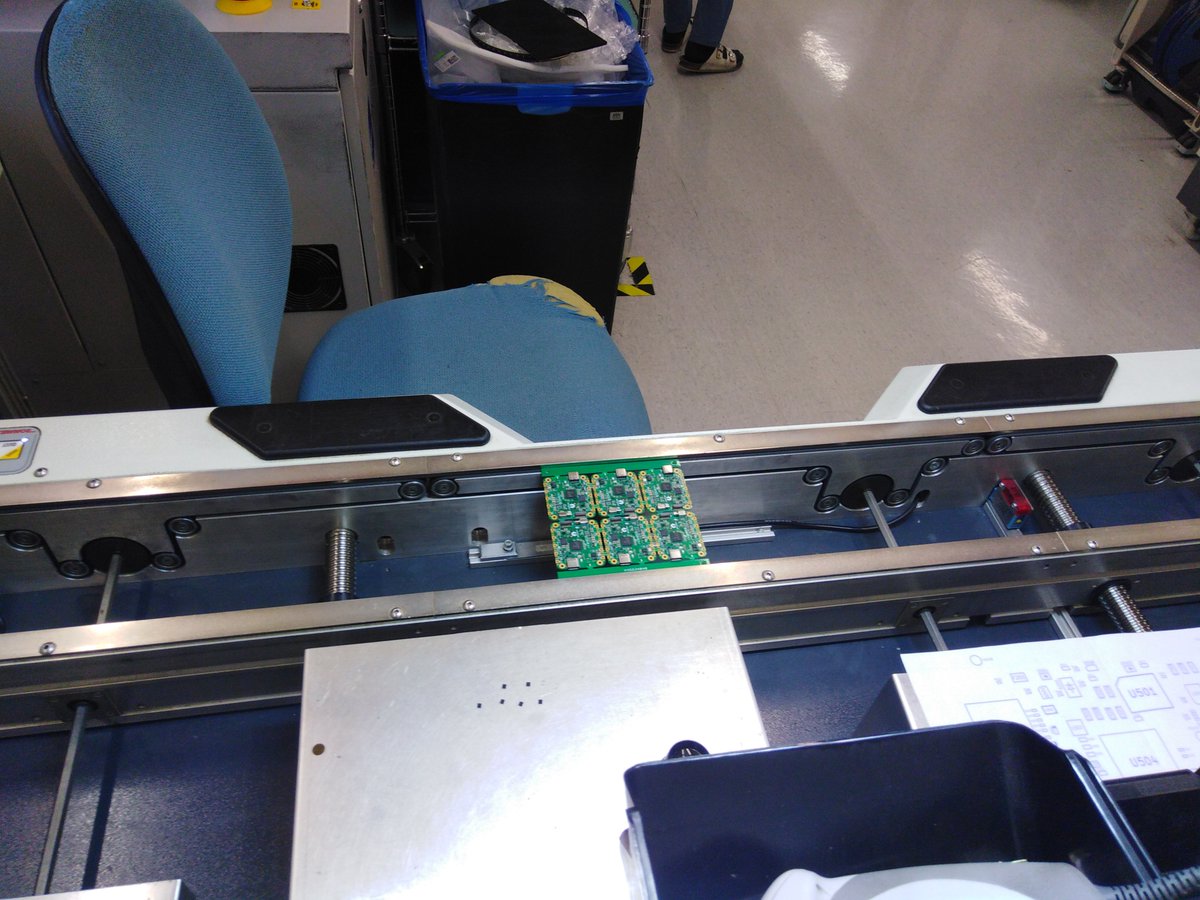
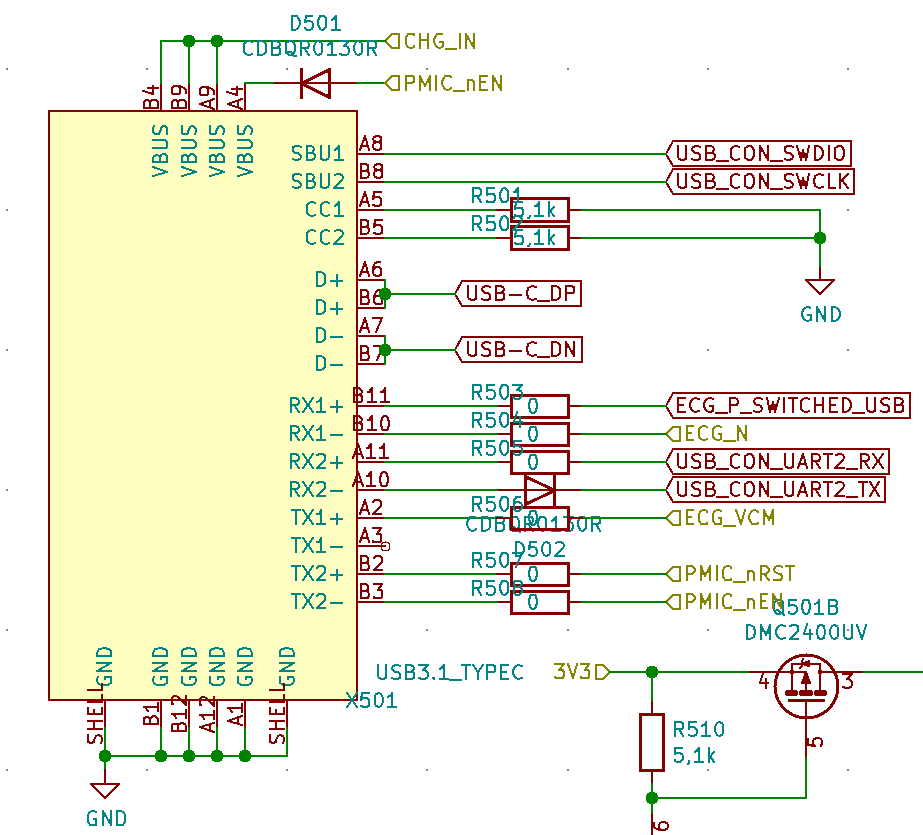
Tomorrow (Thursday) is a bank holiday and on Friday only a few people will be working...
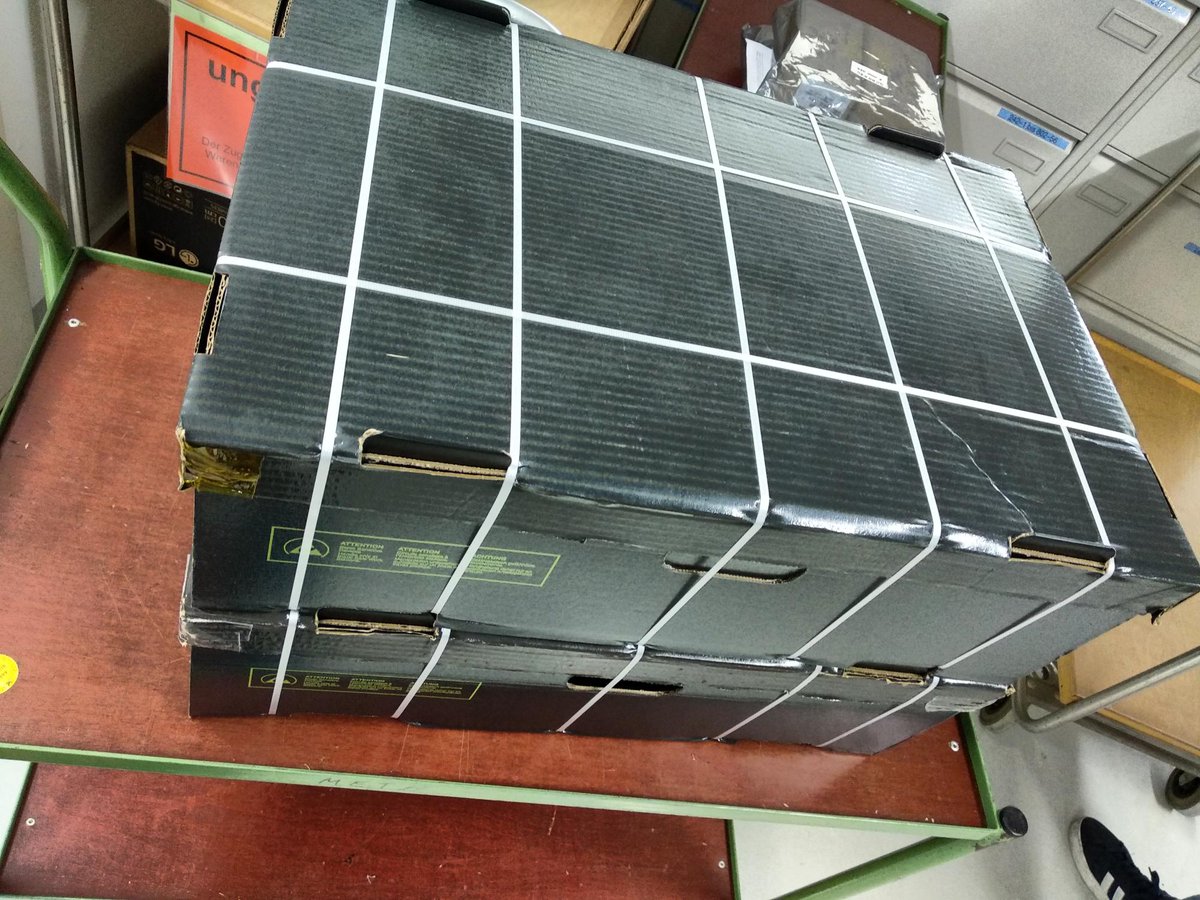
We are shocked. At that rate we will have no more than 30% done buy the _end_ of #CCCamp2019.
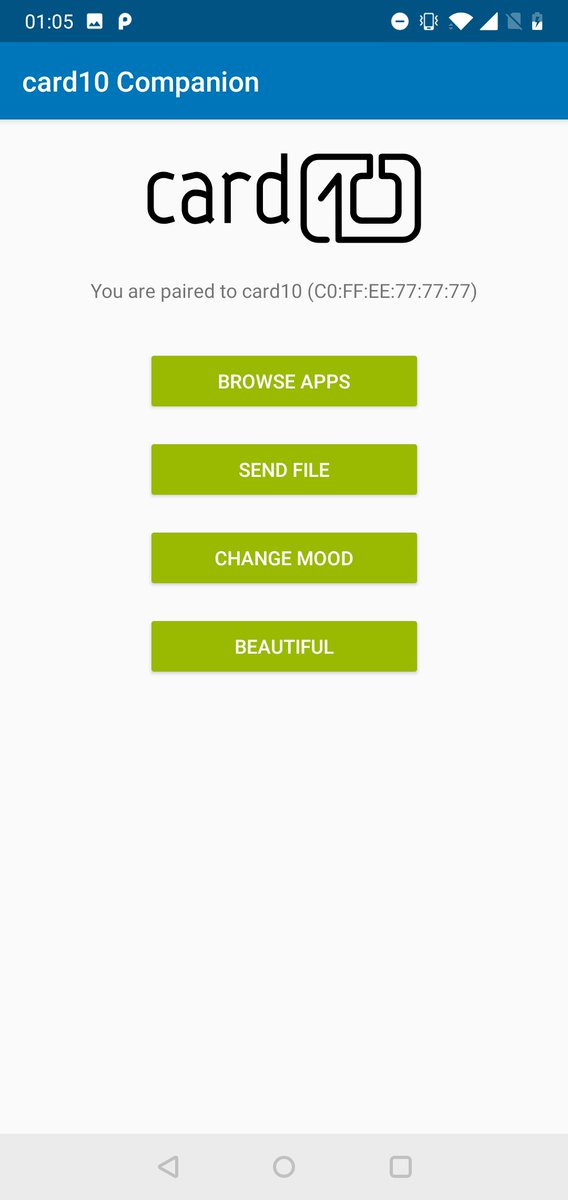
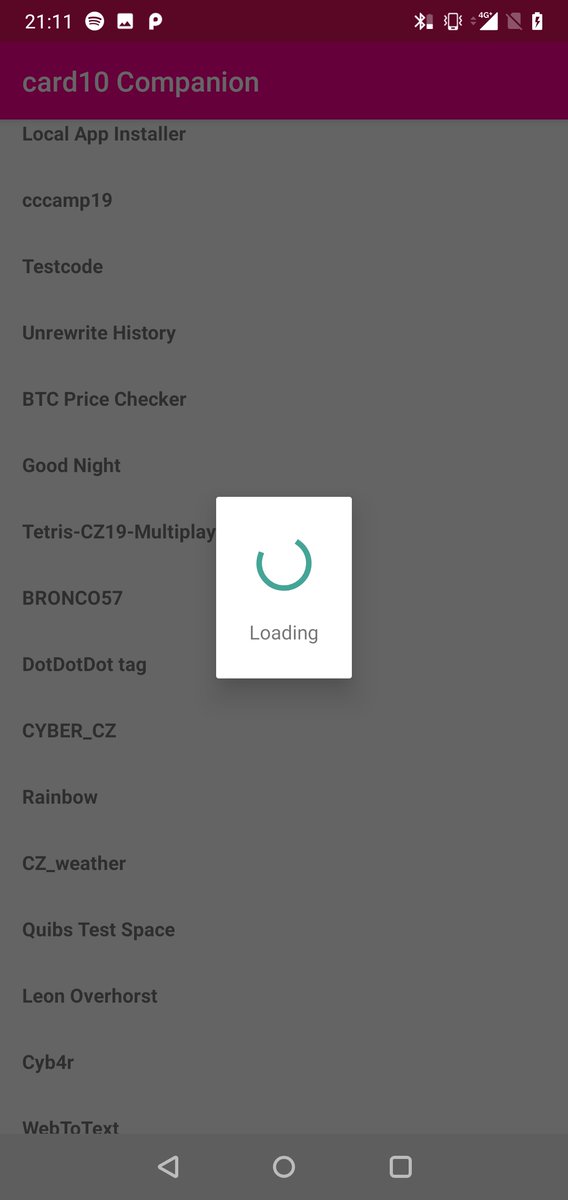
The problem: They have to manually rework a whole lot of the boards due to tomb stoning of components. That slows them down a lot.
No pictures of people due to privacy concerns.
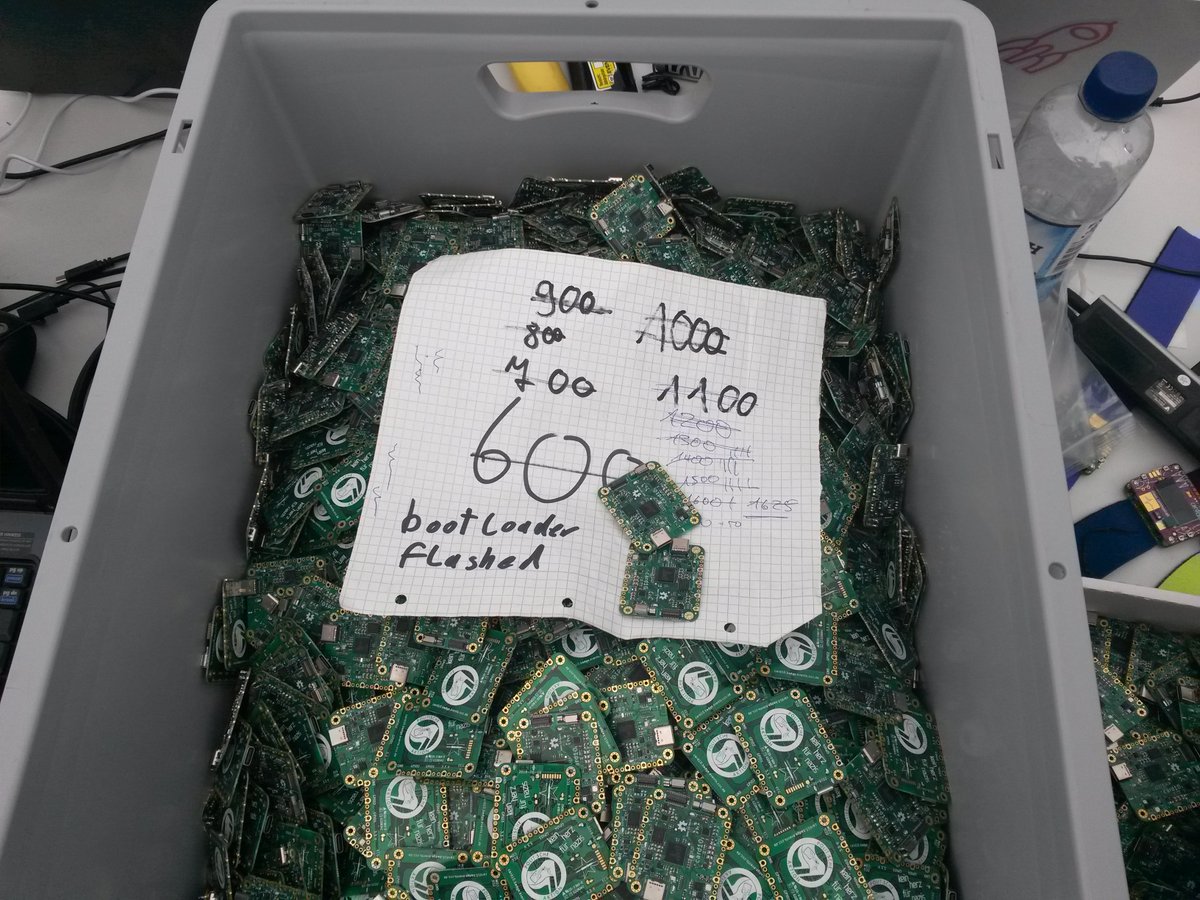
It will take us two more days to receive and distribute all remaining card10s.
media.ccc.de/v/Camp2019-103…
(I'm not on stage due to total burnout)