Lots and lots of lift testing, mainly to get the chains reliable.
Most of the testing was with weights…
#robotwars #battlebots #robotcombat #robotics
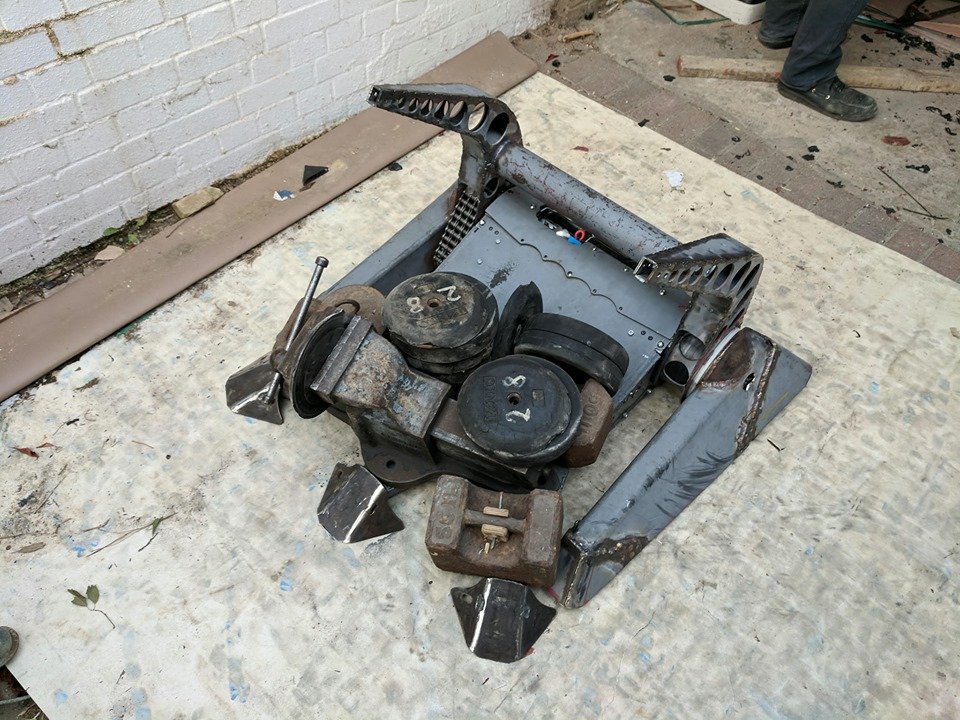
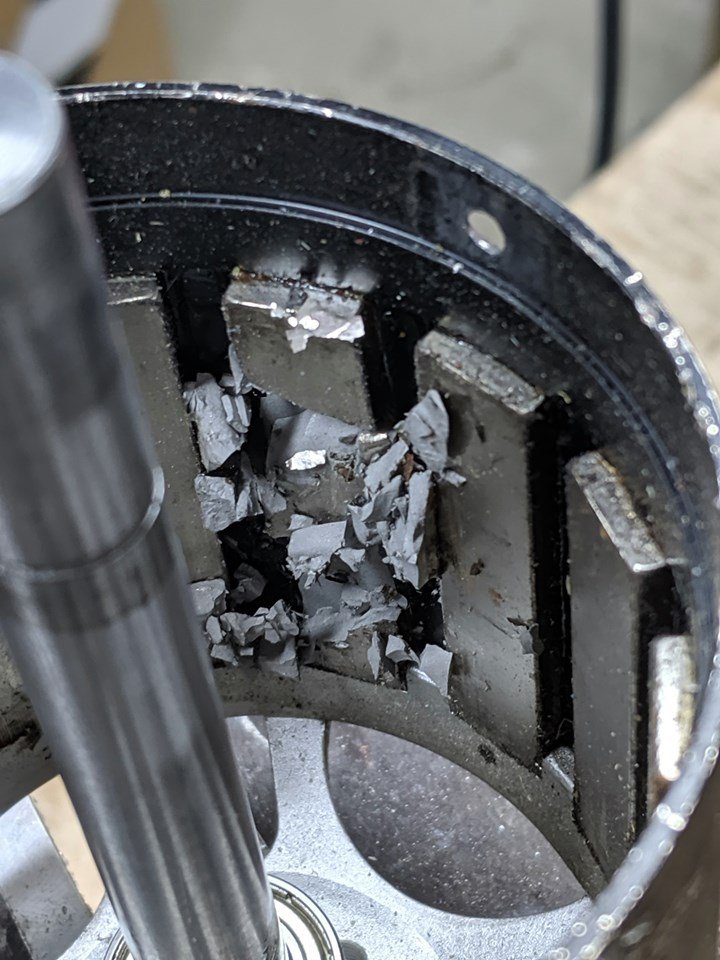
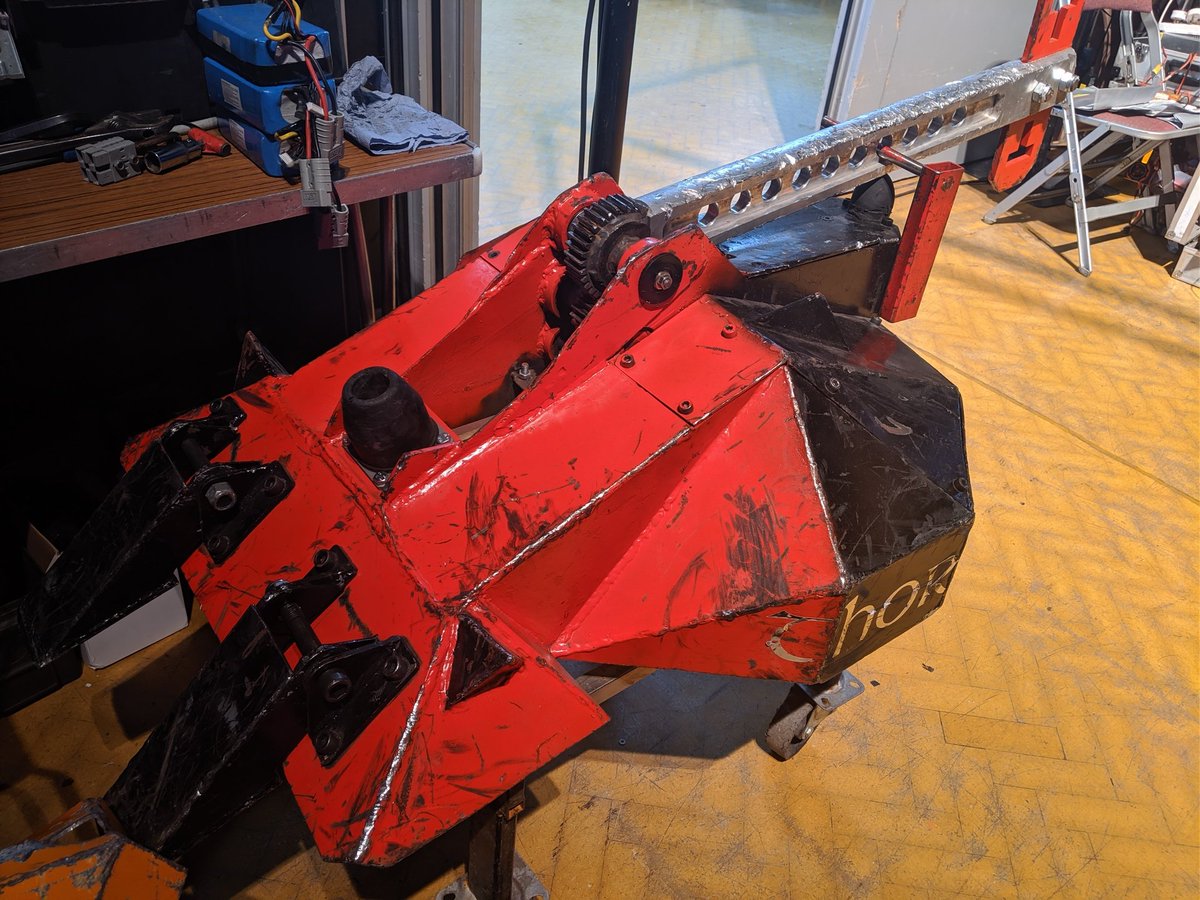
Twitter may remove this content at anytime, convert it as a PDF, save and print for later use!
1) Follow Thread Reader App on Twitter so you can easily mention us!
2) Go to a Twitter thread (series of Tweets by the same owner) and mention us with a keyword "unroll"
@threadreaderapp unroll
You can practice here first or read more on our help page!