Time for a brief introduction to some of our work on materials for jet engines.
(high res and source careers.rolls-royce.com/~/media/Files/…)
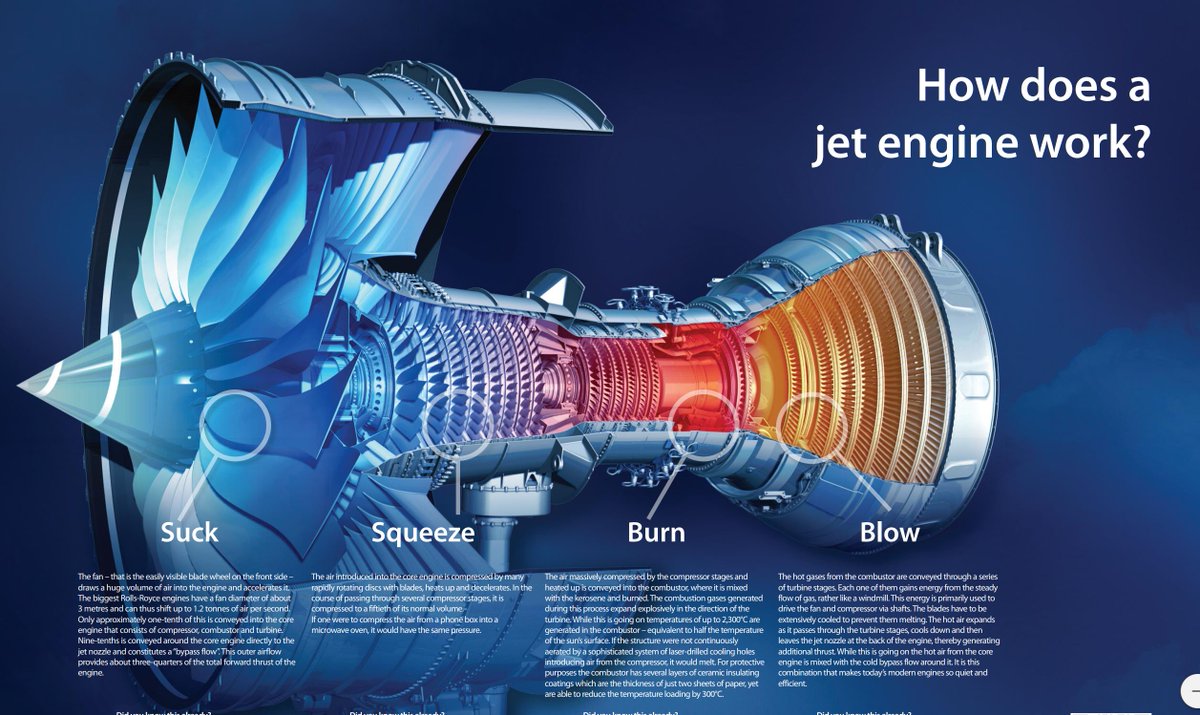
More: phase-trans.msm.cam.ac.uk/2003/Superallo…
Engine failure, & maintenance, are both disruptive and cost money - so the more we know about life the better.
Website: imperial.ac.uk/hexmat
This is all within ETOPS.
en.wikipedia.org/wiki/ETOPS
You are ~300x times more likely to get hurt walking than flying in a commercial plane. I also spend SIGNIFICANTLY more time walking than I do flying.
tjpalanca.com/2014/03/on-pro…